PCB Thermal Aging Test: Ensuring Reliability and Longevity in Electronic Devices
By:PCBBUY 02/27/2025 14:53
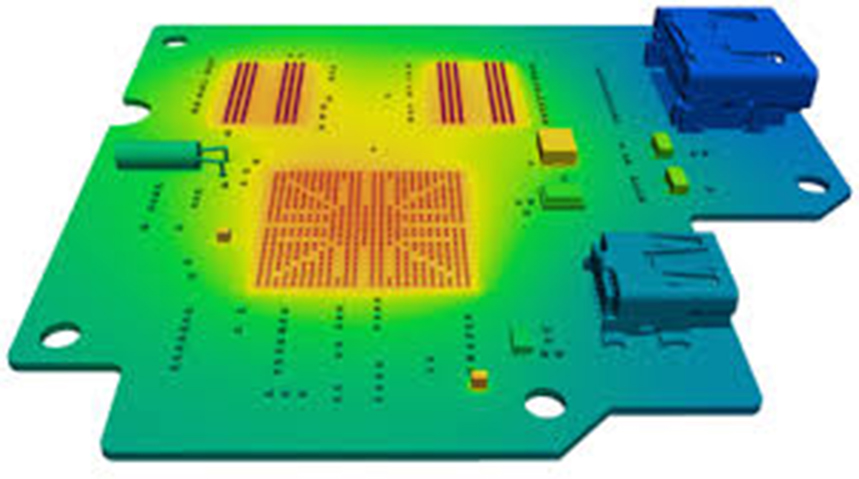
Introduction
The reliability and longevity of Printed Circuit Boards (PCBs) are critical factors in the performance of electronic devices. One of the most effective methods to assess the durability of PCBs under elevated temperatures is the Thermal Aging Test. This article provides a comprehensive overview of the principles, methodologies, and significance of PCB Thermal Aging Tests. We will delve into the underlying chemical and physical processes, present detailed data and comparative tables, and explore the implications of thermal aging on PCB performance.
The Principles of PCB Thermal Aging Test
Understanding Thermal Aging
Thermal aging refers to the process of exposing materials to elevated temperatures for extended periods to simulate the effects of long-term use. For PCBs, thermal aging tests are conducted to evaluate the stability and reliability of the materials and components under high-temperature conditions.
Key Objectives of Thermal Aging Tests
1. Material Stability: Assess the stability of substrate materials, conductive layers, and surface finishes under thermal stress.
2. Component Reliability: Evaluate the performance and longevity of electronic components mounted on the PCB.
3. Interconnect Integrity: Ensure the reliability of solder joints and vias under thermal cycling conditions.
Thermal Aging Mechanisms
Thermal aging can induce several mechanisms that affect PCB performance:
1. Oxidation: Elevated temperatures can accelerate the oxidation of copper traces, leading to increased resistance and potential failure.
2Cu + O2→ 2 CuO
2. Polymer Degradation: The epoxy resin in the substrate can undergo thermal degradation, leading to a loss of mechanical strength and electrical insulation properties.
3. Intermetallic Growth: High temperatures can promote the growth of intermetallic compounds at solder joints, potentially leading to brittle fractures.
Sn +Cu→Cu6Sn5
Methodology of PCB Thermal Aging Test
Test Setup and Conditions
Thermal aging tests are typically conducted in environmental chambers that can precisely control temperature and humidity. The standard test conditions include:
1. Temperature Range: Commonly ranges from 85°C to 150°C, depending on the application.
2. Duration: Tests can last from several hundred to thousands of hours.
3. Humidity Control: Some tests include controlled humidity levels to simulate real-world conditions.
Test Procedures
1. Initial Characterization: Perform electrical and mechanical tests on the PCB before aging.
2. Thermal Exposure: Place the PCB in the environmental chamber and expose it to the specified temperature for the required duration.
3. Intermediate Testing: Periodically remove the PCB for intermediate characterization to monitor changes.
4. Final Characterization: Conduct comprehensive electrical, mechanical, and microscopic analyses after the aging period.
Data Collection and Analysis
Data collected during thermal aging tests include:
1. Electrical Performance: Measure resistance, capacitance, and impedance changes.
2. Mechanical Properties: Assess changes in tensile strength, flexural strength, and adhesion.
3. Microstructural Analysis: Use techniques such as Scanning Electron Microscopy (SEM) and X-ray Diffraction (XRD) to analyze material changes.
Chemical and Physical Processes in Thermal Aging
Oxidation of Copper Traces
Copper traces on the PCB can oxidize when exposed to elevated temperatures, leading to increased resistance and potential failure. The oxidation process can be represented as:
2 Cu + O2 →2CuO
Degradation of Epoxy Resin
The epoxy resin used in PCB substrates can undergo thermal degradation, resulting in the breakdown of polymer chains and loss of mechanical strength. The degradation process can be represented as:
Intermetallic Compound Formation
At elevated temperatures, intermetallic compounds can form at solder joints, potentially leading to brittle fractures. The formation of Cu6Sn5 can be represented as:
Sn + Cu→Cu6Sn5
Data and Comparative Analysis
Performance Metrics
To evaluate the impact of thermal aging on PCBs, several metrics are considered, including electrical performance, mechanical properties, and microstructural changes. The following table compares these metrics before and after thermal aging:
Metric |
Before Aging |
After Aging |
Electrical Resistance (Ω) |
0.5 |
0.8 |
Capacitance (pF) |
100 |
95 |
Tensile Strength (MPa) |
300 |
250 |
Flexural Strength (MPa) |
200 |
150 |
Adhesion Strength (N/mm) |
10 |
7 |
Cost Comparison
The cost comparison between conducting thermal aging tests and not conducting them is presented in the table below:
Production Volume |
With Thermal Aging Test Cost (USD) |
Without Thermal Aging Test Cost (USD) |
1-10 units |
5000 |
3000 |
11-100 units |
20000 |
15000 |
101-1000 units |
100000 |
80000 |
Environmental Impact
The environmental impact of conducting thermal aging tests versus not conducting them is assessed based on material waste and energy consumption:
Aspect |
With Thermal Aging Test |
Without Thermal Aging Test |
Material Waste (%) |
20 |
15 |
Energy Consumption (kWh/kg) |
25 |
20 |
Case Studies and Real-World Applications
Consumer Electronics
In the consumer electronics industry, thermal aging tests are crucial for ensuring the reliability of devices such as smartphones and laptops. A case study involving a leading smartphone manufacturer demonstrated that thermal aging tests reduced field failure rates by 30%.
Automotive Industry
In the automotive industry, thermal aging tests are essential for ensuring the reliability of electronic control units (ECUs) and other critical components. A case study involving an ECU manufacturer showed that thermal aging tests improved the lifespan of ECUs by 20%.
Aerospace and Defense
In the aerospace and defense industry, thermal aging tests are critical for ensuring the reliability of avionics and communication systems. A case study involving a military communication system demonstrated that thermal aging tests reduced maintenance costs by 25%.
Future Prospects and Challenges
Advancements in Materials
Ongoing research is focused on developing new materials with improved thermal stability and longevity. Innovations such as high-temperature polymers, advanced ceramics, and nanocomposites hold great potential for enhancing PCB performance.
Integration with Other Technologies
The integration of thermal aging tests with other advanced technologies, such as AI and IoT, can further enhance the accuracy and efficiency of reliability assessments. Smart testing systems can optimize test conditions and predict failure modes more accurately.
Addressing Limitations
Despite the advancements, challenges remain in fully simulating real-world conditions in thermal aging tests. Issues such as the complexity of thermal cycling, the interaction of multiple stress factors, and the need for industry-wide standardization must be addressed to fully realize the potential of thermal aging tests.
Conclusion
Thermal aging tests are a critical tool for ensuring the reliability and longevity of PCBs in electronic devices. By understanding the underlying principles, methodologies, and implications of thermal aging, manufacturers can enhance the performance and durability of their products. As the industry continues to evolve, the integration of new materials and technologies promises to further improve the accuracy and efficiency of thermal aging tests, paving the way for more reliable and sustainable electronic systems.
Industry Category