PCB embedded components
By:PCBBUY 08/03/2021 17:32
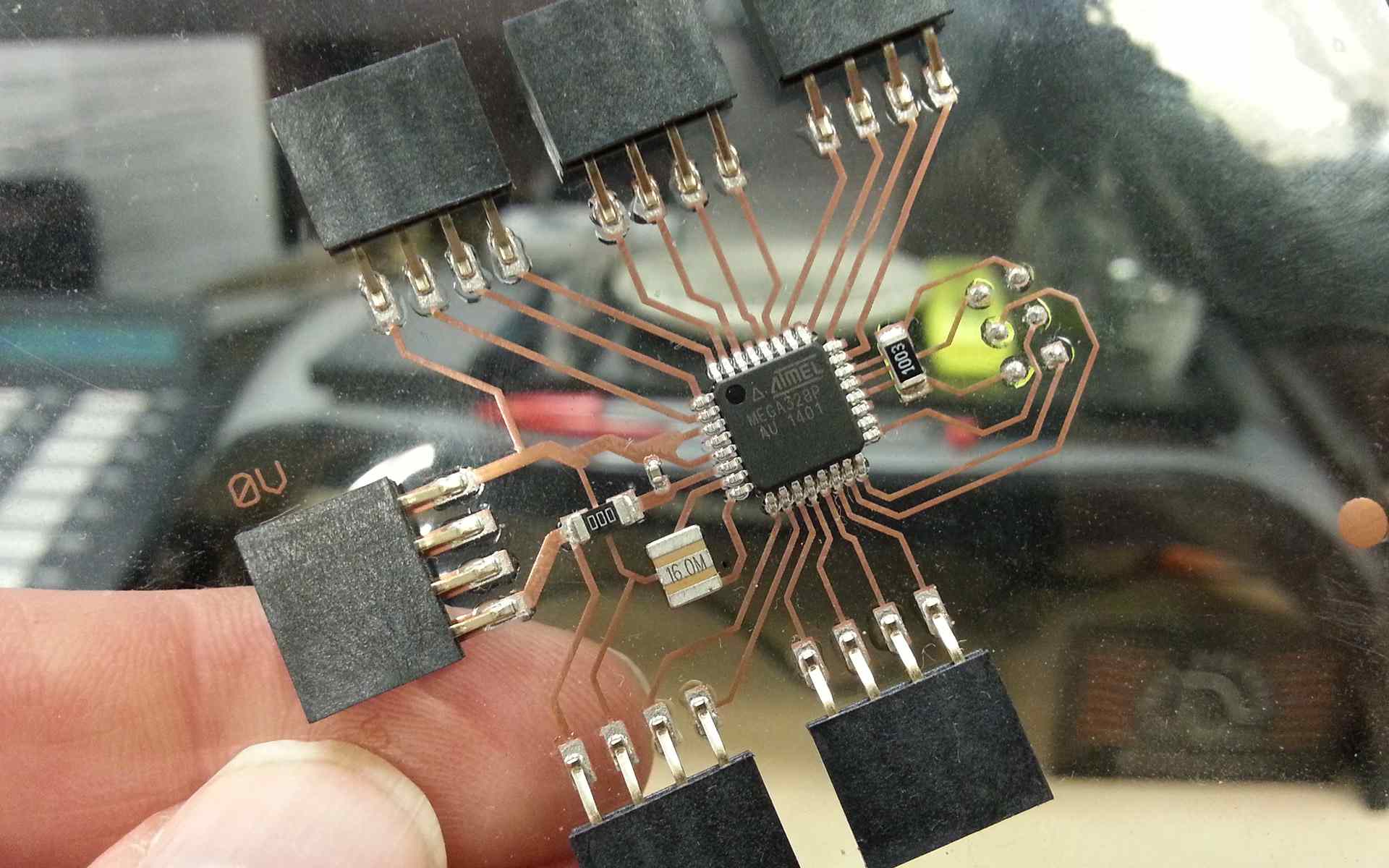
Embedded technology plays an active role in shrinking interconnect path between components and reducing transmission loss. In order to explore a better solution, some designers consider embedding components such as inductors, resistors and capacitors into the internal part of PCB board so that high density and miniaturization of electronics products can be obtained.
In this passage, we will provide you everything about PCB embedded components. Please check and read the content below for more information about it.
What are the types of PCB embedded components?
• Embedded Resistors and Capacitors
Different fabrication technologies are available for component embedment. When it comes to embedded resistors, material with high resistance is first applied; nickel-phosphorus nickel-coated substrate material is then used; next, ceramic thick film pre-burning method or LTCC (low temperature co-fired ceramic) is leveraged. Finally, all kinds of planar resistors with different resistance can be fabricated.
A better method of embedded capacitor fabrication is direct lamination of polymer in metal sheets. Embedded capacitor fabrication technologies include dielectric membrane application, thick or thin film dielectric generation and high temperature firing thick membrane application with high dielectric constant.
Based on the introduction above, PCB manufacturers mainly place resistors and capacitors on the surface of internal layer of PCB board by etching or printing. Then they are embedded into internal board through lamination and multi-layer PCB fabrication technology. Component embedment replaces passive component soldering on PCB board surface with component assembly and tracing freedom dramatically rising.
• Embedded Inductors
Inductors embedment is shape formation like spiral or bending through etching or copper plating or spiral multi-layer structure formation through through-hole between layers. Up to now, high-frequency module is most widely applied. PCB manufacturers place inductors on the internal layer of PCB board through etching or printing based on internal fabrication technology of a multi-layer circuit board.
Among inductors are inductors containing magnetic core. This type of inductors holds magnetic cores and rounding coil with which AC magnetic field energy is stored in DC/AC with corresponding current functions implemented. Magnetic cores can be either inlaid or embedded while coil can only be designed in via. Inductor embedded products primarily come in two types: solidly embedded inductor and hollowly embedded inductor. The former is fixed into PCB with embedded inductor laminated by peripheral prepreg. The latter vibrates with the movement of PCB with embedded inductors inside circuit board.
• Embedded Thermal Copper Blocks
Constantly shrinking of electronic product volume and increasingly higher density has made thermal dissipation of electronic products a huge challenge of industrial design. Up to now, leading thermal dissipation methods include PCB fabricated with metal as substrate, metal base soldering on circuit board and through-hole with conductive paste filled in. The first two types lead to a large consumption of metal material and are suitable for single-side PCB fabrication. The rest of methods feature so complicated processes and thermal dissipation fails to meet demands called by design.
Copper blocks embedment defeats the issue of high cost and can effectively solve thermal dissipation problem. Leading types of thermal dissipation include:
a. Copper Block Penetration. Thickness of embedded copper block is equivalent to that of finished board. Copper block goes through top and bottom layer.
b. Semi-Embedded Copper Block. The thickness of embedded copper block is smaller than that of finished board. One side of copper block remains at the same height with bottom layer while the other side remains at the same height with one internal layer.
What are the difficulties of PCB embedded components?
• Embedded Resistors and Capacitors
Resistor-embedded products derive most from resistor embedment through etching receiving relatively wide applications. Leading materials for resistor embedment widely accepted by industry are Ni-P alloy and Ni-Cr alloy whose performances are different and that call for different etching solutions. Up to now, the leading problem faced during the process of resistor-embedded material etching is how to control resistance and corresponding tolerance, that is, line compensation of resistor's position, which becomes especially significant when it comes to resistor materials with low square resistance because etching will bring forward more influence to resistance.
Embedded capacitors are a type of capacitance materials that can be embedded into PCB board. Because this type of materials features high capacitance density, it plays a role as decoupling and filtering in power supply system, which then further reduces free capacitance. This type of material is capable of improving electronic products' performance and decreasing circuit board size. The primary difficulty for capacitor embedded electronic products is relatively thin dielectric of embedded material. As a result, tracing and etching has to be completed in single side.
• Magnetic Core Component Embedment
a. Milling Tank Control. After material cutting for PCB board, a circular tank should be milled out on core board.
b. Complete Magnetic Core Lamination with Gel Fully Filled. Prior to PCB lamination, magnetic core is placed in the milling tank, which needs to consider complete magnetic core lamination with gel fully filled. Lamination structure and layout mode should be monitored.
c. Laminate Structure Design. Two design methods are available for lamination structure design of magnetic core embedded PCB: application of magnetic core during lamination and magnetic core lamination.
d. Lamination Layout Mode. To stop magnetic core from falling off, magnetic core side should be upwards during layout and to stop magnetic core from breaking with stress concentrating, crash pad should be used during layout.
e. Plated Through Hole Manufacturing around Magnetic Core. To guarantee that drilling won't damage magnetic core and stop short circuits from taking place after plating, the secure distance between holes and magnetic core should be at least 0.2mm during design phase.
• Electronic Products with Copper Blocks Embedded
a. As far as copper block penetration-type embedment, milling tank size control should be equivalent to that of magnetic core embedment.
b. For products with copper blocks semi-embedded, depth of milling tank should be focused on.
c. When it comes to connection between copper blocks and prepreg, one side of copper block should be brownized.
d. Lamination Layout. Copper block should be placed upward to stop copper blocks falling down. Crash pad should be used during lamination layout to stop defects from occurring to gel absence.
The implementation of component embedded technology is one of essential solutions to power module miniaturization and development demand towards miniaturization and multiple functions of electronic products. PCB surface area can be greatly optimized with capacitors, inductors and resistors embedded into internal PCB. Furthermore, copper block embedded products can both effectively reduce cost of high-frequency products and improve thermal dissipation performance.
Industry Category