Pth Drill
By:PCBBUY 03/29/2024 16:53
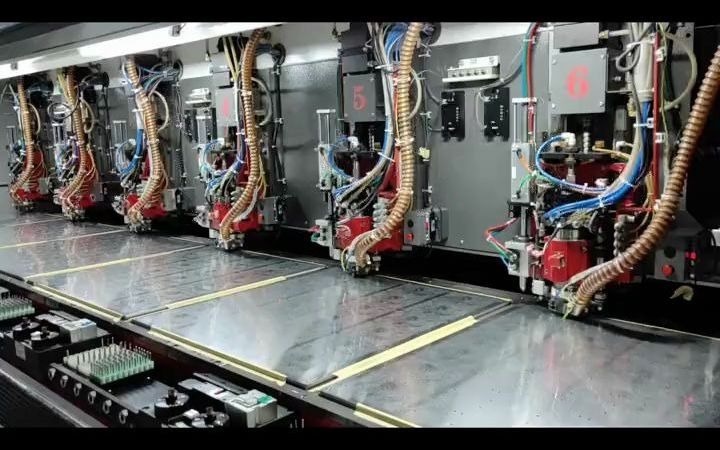
PCB drilling technology is a crucial aspect of electronic manufacturing, playing a vital role in the fabrication of printed circuit boards (PCBs). The primary purpose of drilling is to create vias (conductive holes) and mounting holes on PCBs, facilitating interconnection between different layers or component installation. These holes not only enable the transmission of current and signals between different layers but also form the foundation for PCB functionality. This article will delve into the principles, applications, implementation steps, and future trends of PCB drilling technology.
Basic Principles of PCB Drilling Technology
The fundamental principle of PCB drilling technology involves the utilization of specialized drilling equipment to create the required holes on the PCB. Mechanical drilling involves the removal of PCB material through the rotational and feed movements of a drill bit, utilizing the cutting action of the drill tip to form holes. Laser drilling, on the other hand, employs a high-energy laser beam to rapidly melt, vaporize, or reach the ignition point of the PCB material, while high-speed airflow removes the melted or burned material, thereby forming holes.
Applications of PCB Drilling Technology
PCB drilling technology finds wide applications in various electronic product manufacturing processes, including computers, communication equipment, consumer electronics, etc. In the PCB manufacturing process, drilling is a critical step in achieving multilayer board interconnection and component installation. Through drilling, conductive vias can be formed between different layers to facilitate current transmission and signal transfer. Additionally, drilling is also used for mounting various electronic components, such as sockets, pads, and surface-mount components.
Implementation Steps of PCB Drilling Technology
(A) Implementation Steps for Mechanical Drilling
1. Preparation Stage: Select appropriate drill bits and drilling equipment based on design requirements, and set drilling parameters such as speed and feed rate.
2. Positioning Stage: Secure the PCB on the drilling equipment's worktable and use positioning devices to ensure accurate drilling positions.
3. Drilling Stage: Initiate the drilling equipment, where the drill bit rotates and feeds downward, cutting through the PCB material to form holes.
4. Cleaning Stage: After drilling, clean the drill chips and residues, and inspect the quality and dimensions of the holes to ensure compliance with requirements.
(B) Implementation Steps for Laser Drilling
1. Preparation Stage: Select suitable laser equipment and drilling parameters such as laser power and pulse frequency based on design requirements.
2. Positioning Stage: Utilize laser positioning systems to accurately align the laser beam with the drilling positions.
3. Drilling Stage: Activate the laser equipment, allowing the high-energy laser beam to irradiate the PCB material, melting, vaporizing, or burning it, while high-speed airflow removes the material to form holes.
4. Cleaning Stage: After drilling, clean the residues and smoke, and inspect the quality and dimensions of the holes for compliance.
Future Trends in PCB Drilling Technology
With the continuous miniaturization and high-performance requirements of electronic products, the demands on PCB drilling technology are increasing. In the future, PCB drilling technology will evolve in the following directions:
1. High Precision: The demand for high precision in hole positions and dimensions on PCBs is increasing with the enhanced functionality of electronic products. Therefore, improving drilling technology's precision will be a key focus of future development.
2. High Efficiency: To enhance production efficiency and reduce manufacturing costs, future drilling technology will emphasize achieving higher efficiency. This may involve optimizing the structure and performance of drilling equipment to increase drilling speed and efficiency.
3. Intelligence and Automation: With the development of smart manufacturing technology, future PCB drilling technology will focus more on intelligence and automation. For example, utilizing machine vision and sensor technology to achieve automatic positioning and inspection, thereby improving drilling accuracy and stability.
4. Green Environmental Protection: The drilling process generates a large amount of waste and harmful gases, causing environmental pollution. Therefore, future drilling technology will emphasize improving environmental performance, such as using eco-friendly materials and processes and reducing waste and harmful gas emissions.
In summary, PCB drilling technology is a crucial aspect of electronic manufacturing, playing a vital role in the fabrication of PCBs. In the future, with the continuous advancement of technology, PCB drilling technology will continue to innovate and improve, providing more efficient, precise, and environmentally friendly solutions for electronic product manufacturing.
Industry Category