Rigid-flex PCB applications
By:PCBBUY 07/24/2021 17:28
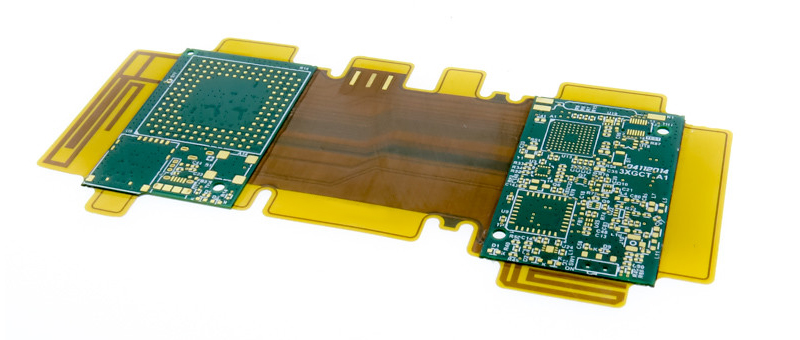
A rigid flex board is a hybrid of hardboard and flexible circuits. The manufacturing process resembles that of a traditional hardboard circuit, but some of the layers are flexible circuit that runs all the way through the hardboards. The board fabricator will then add plated through holes to connect layers of rigid circuit to regions of flexible circuit.
These configurations create a rigid flex PCB that can be assembled similarly to hardboards, but also fold to fit into a product with space constraints. They are also suitable for continuously flexing applications – also known as dynamic flex. Well designed, a rigid flex board can withstand hundreds of thousands of flex cycles without failure. In either case, the rigid and flexible substrates form one integrated unit that can be further manipulated into a 3D subassembly.
In this passage, we are going to talk about the applications of rigid-flex PCB. Please check and read the content below to learn more professional knowledge.
What are the types of rigid-flex PCB?
Flex type depends on the number of conductive layers, construction and materials, and the presence or absence of plated-through holes.
1. Single-sided flexible printed circuit board. This is the most common type of flex circuit, ideal for dynamic flex applications. Contains one conductive layer. Can be found with and without stiffeners. SMT lands accessible only on one side.
2. Double-sided flexible printed circuit boards. Contains two conductive layers with plated-through holes. Can be found with or without stiffeners. Copper is bonded on both sides of the base material, then drilled, plated, etched and insulated on both sides by a top and bottom dielectric cover layer.
3. Multilayer flexible printed circuit board. Contains three or more conductive layers with plated-through holes. The plated-through holes are used to create the interconnection of the conductive layers. Can be found with or without stiffeners.
4. Multilayer rigid and flexible material combinations containing three or more conductive layers with plated-through holes.
5. Flexible or rigid-flex printed circuit boards. Contains two of more conductive layers. No plated through-holes.
What are the applications of rigid-flex PCB?
Flex connections have mechanical advantages over conventional ribbon cables in various applications but in some cases, they also have better chemistry.
A flex circuit can be formed in complex shapes in three dimensions with branches to multiple connectors, which would be impossible to achieve with a ribbon cable. Moreover, flex circuits can be interfaced with rigid boards without the relatively tall and bulky connectors flat cables require, or in the case of rigid-flex construction, they can be integral with the boards and eliminate external connectors altogether. Furthermore, the conductor density of flex circuits can far exceed that of ribbon cables.
There are some subtle advantages of flex circuits versus conventional ribbon cables beyond the many clear distinctions. One of the materials commonly used for flex circuits, Kapton, has extremely low outgassing in ultra-high-vacuum environments, such as space. Though Kapton-insulated ribbon cables are available, they have a limited number of conductors and cannot be routed at angles in tight confines.
Ribbon cables insulated with Teflon and other plastic materials outgas fluorine or reactive compounds when subjected to high vacuums, which can attack electronics in closed containers if care is not taken to completely vent the gases.
Aerospace Applications
The heads-up display (HUD) as used in aerospace is a familiar technology with a clear purpose: displaying operational data directly in the pilot’s field of vision alleviates the need to look away from a potential target to read critical operational data during flight. A recent extension of the HUD, applied to wearable technology, provides remote 3D holographic images in a flip-down visor mounted to a helmet. The holographic waveguide helmet-mounted display (HWVD) from HoloEye Systems provides high-resolution true 3D imaging, using flexible PCB cables to drive the waveguide optical system, which uses HoloEye’s liquid crystal on silicon (LCOS) display technology. The flexibility, reliability, and performance of the flex PCB cables make the HWVD effective in realtime use for avionics, and the light overall weight makes it feasible to mount the display directly on the pilot’s helmet, instead of in the aircraft.
Medical Application
A medical device company utilizes flex PCB designs as important components of a new class of hearing-assist devices, providing higher range and resolution (125 Hz to 10,000 Hz) than currently available hearing devices. The underlying premise is revolutionary: a small photoreceptor and micro-actuator are placed inside the ear canal, with the micro-actuator in contact with the eardrum. Outside the ear, as in conventional hearing devices, a microphone captures the sound and a digital signal processor (DSP) converts it to digital signals to be sent into the ear. But here’s where things get exciting: the digital signals actuate an infrared laser located inside the ear canal, which in turn excite the photoreceptor, turning the digitized audio into a small current which drives the micro-actuator, causing the eardrum to vibrate.
Flex PCB design permitted the engineers to mount the microphone, DSP, and battery in a tiny, compact package that fits behind the ear, and which allows the laser to provide both power and signal to the passive photoreceptor and micro-actuator. While this is currently still an investigational device, the technology is promising and exciting.
The amount of applications and uses for flex PCBs within the consumer industry is too exhaustive to list. But simply put: if you wear it, carry it, or drive it, there’s a good chance it has flexible PCBs in it.
The first flex PCB most people think of is typically the connector between the keyboard and screen of a laptop. Similarly, flip phones use flex PCBs to connect the two halves of the phone. The moving print head of modern printers use flex PCBs in place of the older-style ribbon connectors; likewise, the read/write head of disk drives—which require billions of flexing operations during the product’s lifecycle—have benefited from the increased reliability and cost-effectiveness of flex PCBs.
Automotive applications, in particular, carry a number of advantages, not only in the usual arena of reliability but even more so for the weight savings that a flex PCB offers compared with a standard PCB and wiring harness. Weight is the enemy of fuel efficiency (or range, for electric/hybrid vehicles), and flex PCBs greatly reduce the labor involved in manufacturing a traditional automotive wiring harness. And the inherent resistance of flex PCBs to vibration makes them ideal for the harsh environment inside a motor vehicle.
Whether for cost reduction, longevity, improved product quality or performance, flexible PCBs offer an effective way to connect the various modules of an electronic system.
Computer Electronics
Many computer components rely on flexible circuit boards for operation. The components in hard drives, for example, need to be flexible to keep up with the high speeds at which they write data as well as relatively small and thin. If operating for extended periods of time, hard drives can also get hot, meaning the board must be able to withstand high temperatures. The boards in hard drives are often credited with enabling to last as long as they do.
These issues aren't exclusive to hard drives. Computer electronics today tend to be small and thin and can sometimes reach high temperatures. You can find flexible circuit boards in many other consumer electronics applications as well including televisions, gaming systems, printers and microwaves.
Automotive Electronics
When it comes to modern automobiles, the majority of their electronic hardware uses flexible printed circuit boards. This includes EMUs (engine management units or computers), anti-lock braking systems, air bag controllers, instrument panels and dash systems and much more.
Flexible boards can be designed to fit into smaller spaces and spaces with an irregular shape, which provides more flexibility to engineers. Circuits can also be synced up with other electronics without the need for bulky cable ties or connectors. In many vehicles, weight is also a concern. Even the smallest of add-ons can make a difference. Flexible boards are relatively lightweight and smaller than conventional parts.
Industry Category