Standard PCB Trace Widths
By:PCBBUY 08/31/2021 09:03
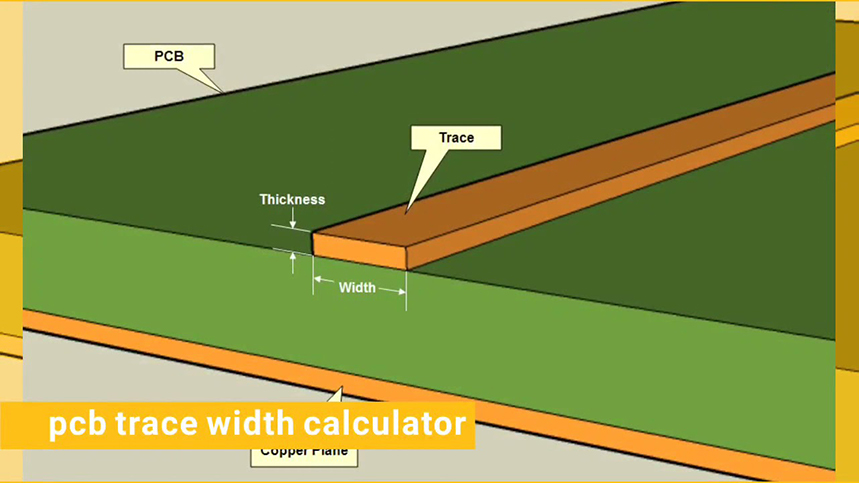
Designers who make the wrong choices on the trace widths for their routing may find that they have problems in one or all of three different areas of their printed circuit board. These areas are fabrication, performance, and assembly。
Follow us and read the content below, we will provide you everything about the standard PCB trace width. You can learn more knowledge about it. Come and check it!
What is the basic introduction of standard PCB trace width?
Let’s start with the basics. What exactly is trace width and why is specifying a particular trace width so important? The point of a PCB trace is to connect any kind of electrical signal, whether it is analog, digital, or power, from one junction to another.
The junction can be the pin of a component, a branch off of a larger trace or plane, or an empty pad or test-point intended for probing. Trace widths are often measured in mils, or thousands of an inch. A standard trace width for an ordinary signal (no special requirements) may be in the 7-12 mil range and be as long as a few inches, but there are many things that should be considered when defining the width and length of a trace.
What are the rules of standard PCB trace width?
So far, we have looked at how trace width and spacing restrictions affect the performance of the board electrically, but there are also manufacturing concerns as well. Traces that are too close to each other or to other metal features of the board could potentially develop shorts during fabrication. Each fabricator will have its own minimum trace width that they will build, but 3 mils is a common minimum spacing value. Copper weight also must be factored in here as well.
Here are some other manufacturing considerations for trace width and spacing restrictions:
· Traces running between the pads under small surface mount components may have the minimum trace to metal spacing, but can still cause manufacturing problems. The part may not sit squarely resulting in tombstoning, or form a solder bridge with a trace and cause damage if the part is lifted for re-work.
· Metal that is too close to the edge of the board could present depanelization problems. Additionally, exposed copper could come into contact with other conductive elements and cause a short on the board.
· Traces that are too wide on the surface mount pads could form solder bridges with adjacent pads or traces. These could cause excess current or shorts.
· It is also important that drill hole sizes match the traces to which they connect. Although vias run through the board they serve the same function as traces that run along the surface. In many cases, they are extensions of them.
How to determine standard PCB trace width?
Let's walk through the process of calculating for a certain trace width for a power signal delivering current from one power component to a peripheral. In this example, we’ll be calculating the minimum trace width for a power-path used for a DC motor. The power-path starts at a fuse, travels through an H-bridge (a component used to manage power delivery across a DC’s motor windings), and ends at the motor’s connector. The average continuous max current demanded by the DC motor will be around 2 Amps.
Now, a PCB trace acts as a resistor and the longer and narrower the trace, the more resistance is added. If the trace isn’t properly defined, the high current could damage the trace and/or introduce significant voltage drop to the motor (resulting in a slower speed). NetC21_2 shown in Figure 3 is about 0.8” long and needs to carry 2 Amps max. If we assume some general things like a 1-ounce copper pour and ambient room-temperature during normal operation, we have what we need to calculate both the minimum trace width and expected voltage drop at that width.
These trace width calculators will prompt you to enter design specifications such as the thickness of copper, the maximum amperage that will pass through the trace, the length of the trace, and the acceptable increase in temperature due to the resistance of the trace dissipating power. After entering these values you will be presented with a calculated trace width. It is important to note that this value is a minimum width required to meet the design criteria inputs.
Now, a PCB trace acts as a resistor and the longer and narrower the trace, the more resistance is added. If we assume some general things like a 1-ounce copper pour and ambient room-temperature during normal operation, we have what we need to calculate both the minimum trace width and expected voltage drop at that width.
Trace spacing
The size of a PCB is directly connected to the cost of the PCB, so in general PCBs are kept as small as possible. The downside of reducing board size is that it can limit the available space to route traces. For low power signal traces it is generally advised to keep traces small to increase the available space available for routing. Excessively large traces consume valuable PCB space while offering highly diminished returns. 6 to 30 mils is typical for most signal trace widths.
Trace ampere capacity
For any given trace on a PCB there is a maximum amount of current it can handle before failure. Passing large currents through a trace will cause it to dissipate heat, and given enough current (and time) the trace will be destroyed by either burning through, or delaminating from the PCB and breaking the trace. Often we think of traces as zero resistance connecting wires between two components, but this is certainly not the case. All traces will have resistance and it is important to consider this when selecting widths. Knowing the resistance of a trace and the maximum current that will be passed through it will help inform which width to use.
Calculating the resistance of a trace is not trivial and can involve a lot of work. Luckily, there are a handful of trace width calculators available online that will help guide the choice of trace width when considering ampere capacity.
Industry Category