Teardrops in PCB layout
By:PCBBUY 08/11/2021 17:19
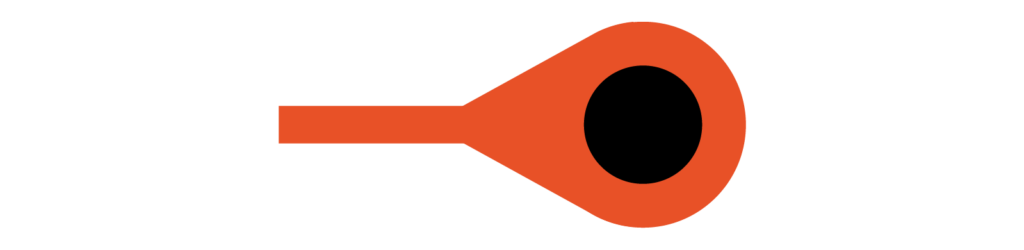
Teardrops are a simple addition to a trace that makes a connection to a landing pad. An example is shown below, where I2C lines are connected to vias in a PCB layout. In the image below, the PCB teardrop is some extra copper that fillets out from the trace to the edge of the via's annular ring. By adding this extra copper, the trace has a stronger connection to the annular ring on the via. The format shown below is probably the most common style of PCB teardrop used on vias. The other teardrop style is sometimes called the snowman style as it adds a small circular section at the trace-to-via connection, rather than using a filleted copper section.
In this passage, we are going to provide detailed information of teardrops in PCB. Please check our content below for more professional knowledge.
Why to use PCB teardrops?
During the PCB fabrication processes, are two potential problems that can occur when drilling a typical PCB:
1. The drill bit may wander during fabrication as there is some very slight inaccuracy and hysteresis in CNC translation stages. As such, the hole and drill can get slightly misaligned, and the drill hole may not line up perfectly with the pad location.
2. Layers can shift very slightly during lamination, which results in misalignment of pads on different layers. The drill can hit perfectly on one layer, but it may be misaligned on another layer.
PCB teardrops are your insurance policy against drill wander and layer misalignment during fabrication. If misalignment is severe, there is still a high chance the drill hit will not sever the connection between the pad and via. The extra copper will still provide a connection that can be plated.
The other reason teardrops are used in a PCB layout is to provide extra strength so that the vias can withstand thermal and mechanical stress. By placing a fillet, we don't have stress concentration at the connection between a thin trace and the pad or via ring. Instead, force on the trace-pad interface will be spread over a larger area, which reduces mechanical stress.
Mechanical and thermal stress can arise in a PCB layout during fabrication and during actual operation. In cases with extreme thermal cycling or mechanical shock, a weak interface between a trace and pad can separate or even fracture. This can occur in both rigid and flexible designs. If this happens during fabrication or assembly, a board will have to be scrapped.
Where to add teardrops in PCB?
· Add teardrops for thru-holes where the trace to pad ratio is small.
· Add teardrops for high density boards where the annular ring around vias should be kept.
· Add teardrops on flex boards to reduce the stress where the trace joins the pad.
· Add teardrops under BGA where have lots of vias.
· Add teardrops when traces exist the pad whether it is a solid pad or a pad with a via.
· Add teardrops when the trace become narrow.
· No need to add teardrops when conductor more than 20mil.
How to add teardrops in PCB?
· It is always better, and recommends to ask the PCB layout engineer to do the teardrops.
· This way you get the same result with any PCB manufacturer how will product your PCB board.
· In some cases, this feature is simply a check box on your CAD system or something that your PCB designer will do for you -you just have to ask.
· In RF or high frequency boards, it is important to have full control of your PCB layout. Teardrops should be added at the design stage itself.
· The PCB fabricator has teardrop creation engine. When auto teardrop creation is allowed to the PCB manufacturer, teardrops connections can be made so DFM routes will be kept.
· In any case we recommend you design with tear drops or give acceptance to PCB manufacturer to add tear drops in working Gerber making stage.
· In some cases, a teardrop cannot be added, most PCB layout software “know” when to add and when it not possible to add teardrop, not need worry about that.
What is the relationship of PCB teardrops and IPC standard?
The IPC standards for reliability are divided into Class 1-3. Designs adhering to Class 3 are intended to have highest possible reliability, with applications areas including military electronics and life support equipment. Devices classified as Class 3 need to have minimum possible downtime and longest possible lifetime. Class 3 products also have exacting fabrication and assembly standards that are intended to ensure reliability.
Various IPC standards call out specific and generic requirements for Class 3 products. Among the various design and fabrication standards, IPC 6012 and IPC 2221A specify requirements on annular rings, blind/buried vias, and component overhang, solder joints, and much more. Although IPC standards do not place specific design requirements on teardrops, they are mentioned in IPC 2221A as a recommended method to ensure reliability. In Class 3 designs, it's highly recommended to use teardrops on annular rings for all vias.
Industry Category