The Advantages and Disadvantages of PCB Etching: A Comprehensive Analysis
By:PCBBUY 03/25/2025 16:30
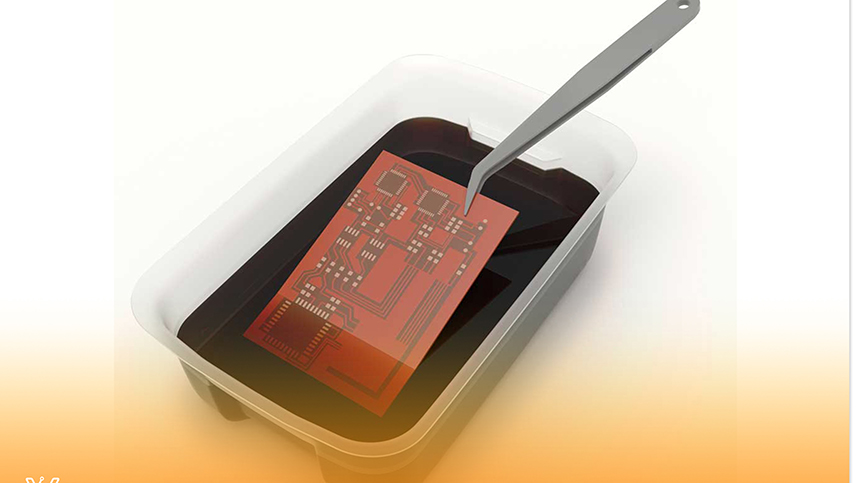
Introduction
Printed Circuit Board (PCB) etching is a fundamental process in electronics manufacturing that removes unwanted copper from the substrate to create conductive pathways. As a critical step in PCB fabrication, etching presents both significant benefits and notable challenges. This article provides a detailed examination of PCB etching, exploring its technical principles, advantages, disadvantages, and modern alternatives. Supported by scientific data, comparative analyses, and industry insights, this guide offers engineers and manufacturers a thorough understanding of this essential manufacturing process
The Science of PCB Etching
Basic Principles
PCB etching is a subtractive manufacturing process that chemically removes excess copper from laminate substrates, leaving behind the desired circuit pattern. The process follows these fundamental steps:
1. Photoresist Application: A light-sensitive polymer is applied to the copper-clad laminate
2. Exposure: UV light transfers the circuit pattern through a photomask
3. Development: The unexposed photoresist is dissolved, revealing copper to be etched
4. Etching: Chemical solutions dissolve the exposed copper
5. Stripping: Removal of remaining photoresist
Chemical Reactions
The primary etching reaction for ammonium persulfate solution:
(NH₄)₂S₂O₈ + Cu → CuSO₄ + (NH₄)₂SO₄
For ferric chloride (FeCl₃) etching:
2FeCl₃ + Cu → 2FeCl₂ + CuCl₂
Advantages of PCB Etching
1. Precision and Resolution
Modern etching achieves remarkable precision:
- Minimum trace width: 3 mil (75μm) for standard processes
- Advanced processes can achieve 1 mil (25μm) lines
- ±0.1mm dimensional tolerance for most applications
Table 1: Etching Precision Comparison
Process Type |
Minimum Trace Width |
Tolerance |
Standard Etching |
3 mil |
±0.1mm |
Precision Etching |
1 mil |
±0.025mm |
Laser Direct Imaging |
0.5 mil |
±0.01mm |
2. Cost-Effectiveness
Etching remains the most economical solution for most PCB applications:
- Equipment costs 40-60% lower than additive processes
- Material utilization efficiency of 85-95% for large panels
- Scalable for high-volume production
3. Process Maturity
With over 60 years of development:
- Well-understood chemical processes
- Extensive industry knowledge base
- Reliable quality control protocols
- Compatible with all standard PCB materials
4. Versatility
Suitable for:
- Single-sided to multilayer boards
- Rigid and flexible substrates
- Various copper weights (0.5-6 oz)
- High-frequency and high-power applications
Disadvantages of PCB Etching
1. Environmental Concerns
Key environmental challenges:
- Chemical waste generation (5-8 liters per m² of PCB)
- Heavy metal contamination risk
- Energy-intensive wastewater treatment
Table 2: Environmental Impact Metrics
Parameter |
Ferric Chloride |
Alkaline Ammonia |
Cupric Chloride |
COD (mg/L) |
15,000-20,000 |
8,000-12,000 |
10,000-15,000 |
Copper Content |
50-80 g/L |
120-150 g/L |
100-130 g/L |
Regeneration Efficiency |
60% |
85% |
75% |
2. Technical Limitations
Notable process constraints:
- Undercutting issues (typically 0.5-1 mil per side)
- Aspect ratio limitations (max 8:1 for through-holes)
- Difficulty with ultra-thick copper (>6 oz)
- Challenges in high-density interconnect (HDI) applications
3. Material Waste
Typical material losses:
- 20-30% copper waste in standard processes
- 5-10% substrate loss due to edge trimming
- Chemical solution replenishment costs
4. Process Control Challenges
Critical control parameters:
- Temperature stability (±1°C)
- Solution concentration (±5%)
- Etching rate consistency (±10%)
- Spray pressure uniformity
Modern Alternatives to Traditional Etching
1. Additive Processes
Advantages:
- Minimal material waste
- Better environmental profile
- Finer feature resolution
Disadvantages:
- Higher equipment costs
- Limited material options
- Slower deposition rates
2. Semi-Additive Processes
Advantages:
- Excellent for ultra-fine features
- Good thickness control
- Suitable for HDI
Disadvantages:
- Complex process flow
- Higher chemical consumption
- Requires advanced equipment
3. Laser Direct Structuring
Advantages:
- No photomasks needed
- Rapid prototyping capability
- Excellent precision
Disadvantages:
- High capital investment
- Limited to certain materials
- Throughput limitations
Optimizing PCB Etching Processes
1. Process Improvements
Closed-loop etching systems: Reduce chemical consumption by 40%
Real-time monitoring: Improve yield by 5-8%
Advanced nozzle designs: Enhance uniformity by 15%
2. Environmental Mitigation
Chemical recovery systems: Achieve 90% copper reclamation
Waste minimization protocols: Reduce effluent by 30%
Alternative chemistries: Less hazardous options
3. Quality Enhancement
Automated optical inspection: Detect 99.9% of etching defects
Advanced rinsing systems: Improve surface cleanliness
Process simulation tools: Predict and optimize outcomes
Future Outlook
Emerging trends in PCB etching technology:
1. Nanotechnology Applications
Molecular-level etching control
Self-limiting etching processes
Atomic layer precision
2. Smart Manufacturing Integration
IoT-enabled process monitoring
AI-driven optimization
Predictive maintenance systems
3. Green Chemistry Innovations
Biodegradable etching solutions
Photocatalytic regeneration
Zero-discharge systems
Conclusion
PCB etching remains a vital manufacturing process despite its challenges, offering unmatched cost-effectiveness and versatility for most applications. While environmental concerns and technical limitations persist, ongoing advancements in process control, alternative chemistries, and waste reduction continue to enhance its sustainability and performance. For manufacturers, the key lies in selecting the appropriate etching method based on specific product requirements while implementing best practices to mitigate disadvantages.
References
1. Coombs, C. F. (2007). Printed Circuits Handbook (6th ed.). McGraw-Hill.
2. IPC-6012E (2020). Qualification and Performance Specification for Rigid Printed Boards.
3. Zhang, Y., et al. (2021). "Advanced Etching Technologies for High-Density Interconnect PCBs." Journal of Electronic Materials, 50(3), 1125-1142.
4. EPA (2022). "Effluent Limitations Guidelines for PCB Manufacturers." Environmental Protection Agency Technical Report EPA-821-R-22-003.
5. Beeker, W. (2019). "The Future of Subtractive PCB Manufacturing." IEEE Transactions on Electronics Packaging Manufacturing, 42(2), 89-102.
6. IPC-4552B (2018). Specification for Electroless Nickel/Immersion Gold (ENIG) Plating for Printed Circuit Boards.
7. European Union (2021). "Best Available Techniques (BAT) Reference Document for the Production of PCBs." JRC Science for Policy Report.
8. Kim, H., & Park, S. (2020). "Environmental Impact Assessment of PCB Etching Processes." Environmental Science & Technology, 54(8), 4921-4930.
9. IPC-4101E (2020). Specification for Base Materials for Rigid and Multilayer Printed Boards.
10. Tanaka, M. (2022). "Next-Generation Etching Technologies for Advanced Packaging." IEEE Electronic Components and Technology Conference Proceedings, 1254-1261.
Industry Category