Top 5 Basic Design Rules PCB to Improve Manufacturing Process
By:PCBBUY 09/26/2021 09:38
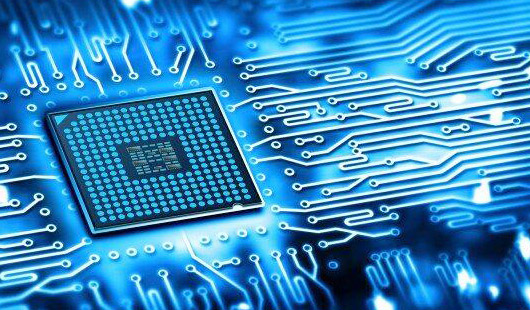
When designing PCB, it’s really important to get into know basic rules to improve the manufacturing process. And it will also affect the performance and quality of the finish boards. But at the end of the day, not providing ample time and focused effort on the PCB layout basics can lead to a design that translates poorly from the digital domain to physical reality, and could ultimately become troublesome for your manufacturer to fabricate.
In this passage, we will tell you every detail about the PCB design rules. If you are interested in the PCB design rules, check and read the content for more professional knowledge.
What is the importance of PCB design rules?
There are many different pieces to the puzzle of designing and building a well-functioning printed circuit board. These include how the parts are placed on the board, how the traces are routed between the parts, and how everything works together electrically to make the board work. The rules are also used by the automated online checking system, which will give the designer immediate notice that what they are attempting to move or edit is not allowed by the rules.
To ensure that the board can be built by PCB fabricators and assemblers, one portion of the rules that can be set up is the design for manufacturability, or DFM, rules. These include unique rules for designing for PCB fabrication, assembly, and test (DFF, DFA, and DFT). They include how close components can get to each other, where test points can be placed, and other manufacturing-specific rules.
What are the 5 basic PCB design rules?
1. Material rules for PCB design?
Consider during the layout phase the materials and components you plan to use for your board. You’ll first need to make sure the desired items are accessible. Some materials and parts are hard to find, while others are so expensive they’re cost-prohibitive. Different components and materials may also come with different designs needs.
Take time to ensure you’ve chosen the optimal materials and components for your board, and also that you’ve designed a board that plays to those items’ strengths.
2. The routing guidelines for PCB design
Printed circuit board design rules and PCB layout guidelines become more complex as the number of layers in your stackup increases. Your routing strategy will require alternating horizontal and vertical traces in alternating layers unless you separate each signal layer with a reference plane. In very complex boards for specialized applications, many of the commonly-touted PCB best practices may no longer apply, and you'll need to follow PCB design guidelines that are particular to your application.
Defining net widths
Your printed circuit board design will likely require different nets that will carry a wide range of currents, which will dictate the required net width. With this basic requirement in mind, it’s recommended to provide a 0.010” width for low current analog and digital signals. Printed circuit board traces that carry more than 0.3 A should be wider. Here’s a free Trace Width Calculator that makes this process easy. You can also use this calculation (based on IPC-2152) to determine your PCB trace width.
3. Board constrain guidelines for PCB design
These guidelines are linked with restrictions of the overall board's shape, size, and some design aspects that influence the concept or design of the PCB. It entails selecting the reference center that benefits the PCB manufacturing process. The reason for this is to have reference points or holes on the board, which are employed for test fixtures and place and pick machines. It also helps enable enough board ground for the circuit.
In most cases, the board's dimensions are elucidated by the size of the product; however, prior to manufacturing PCB designs, the evaluation must be made concerning the board size. It will also be easy to evaluate the layers needed to develop PCB at the start of the design. If more layers are included, then the overall production cost will rise. It is yet critical to ponder how the PCB will be mounted at the start of the design.
4. Ensure the component placement for PCB design
Analog circuit signals must be direct and short. To achieve this trick, you have to ensure a tight element placement for the parts requiring analog components. The importance of buying this idea is maintaining a digital and analog circuitry separate and simplifying the direct routing. Furthermore, do not forget to place noisy analog components around the center rather than along the board's perimeter. This will enable circuitry and ground planes on the circuit board to assist in reducing some of that noise.
5. Track rules for PCB design
Consideration about the aspects of the tracks on the printed circuit board themselves needs to be given at an early stage as there are trade-offs that may need to be made.
· Determine the standard track width to be used. It is necessary to balance the standard track size to be used within the design. If the tracks are too narrow and too close there is a greater possibility of short occurring. Additionally if they are too wide and too far apart then it can restrict the number of tracks in a given area and this may force the use of additional planes in the boards to ensure the PCB design can be routed.
· Consider track size for lines carrying current. The thin tracks used in today's printed circuit boards can only carry a limited current. Consideration needs to be given to the size of track for any that carries power rails rather than low level signals. The table below gives some track widths or a 10degree C temperature rise for different thickness copper boards.
Industry Category