Top 5 Effective Tips of PCB Trace Spacing Standard
By:PCBBUY 04/19/2022 10:11
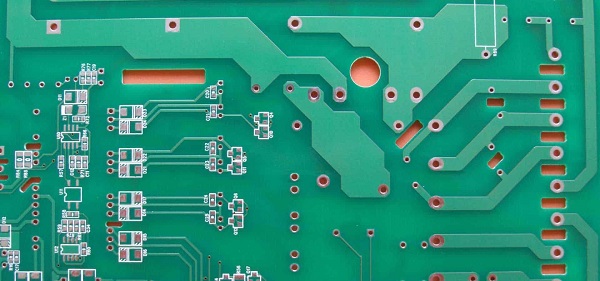
The relationship between trace width and current carrying capacity in your printed circuit boards is fairly straightforward. Specifically, a cross-sectional area of trace and temperature rise determines your current carrying capacity, with your cross-section of trace directly proportional to copper thickness and trace width.
However, this does not necessarily mean that trace carrying capacity is directly proportional to cross-sectional area. Calculating the maximum current that a trace is able to hold based solely on trace width and temperature rise is not always a simple calculation, as you may already have found.
For the beginners of PCB industry, are you searching for more information about the PCB trace spacing? If you are going to learn more about PCB trace spacing, please check and read the content in this passage for more information.
How Do We Determine Trace Impedance?
If we know the geometry of a trace and the properties of the material(s) surrounding it, how do we then calculate the trace’s impedance? In decades past we used various formulas for this. These formulas could be found in various application notes and industry standards, and they were “close enough” then to be suitable. But as requirements have become more precise, these older formulas are no longer considered reliable for the precision we now require. Our requirements became more difficult as we began to want formulas for edge-coupled differential traces, and there never have been reliable formulas for broadside-coupled differential traces.
How to apply the PCB trace resistance equation?
Another example of how this can play out is in resistance based current sensing circuits in power systems. If the sense resistor is 1 ohm and you use the same .025mm trace, the system will measure the resistance at 1100 ohms instead of the preferred 1000 ohms. That is quite a difference, and it can lead to a weaker currency than expected or even necessary.
There do exist ways to work with the trace width that does not involve complicated calculations. These solutions can save much time, and you should consider before performing more complex calculations. You can regard these options to determine the trace width without needing to calculate the PCB trace width.
The first of these can be done by merely eyeballing the width and increasing or lower it to see what kind of circuits are connected to it properly. It will do a couple of things. First, it will increase the area of copper, giving you a bit more room for experimentation with different ohm levels. Second, it will reduce the resistance of the copper on the board. It will also allow for a bit more testing to determine a proper trace width.
For grid array packages, this is not an option. The option here would be to use a thicker copper layer and place it along with the original circuit board. It will increase the area and reduce resistance. One thing that should be made aware of about this is that using a thicker copper layer does require that you purchase the proper materials that are needed to create a more adhesive copper layer. It will cost some money.
How to process standard PCB trace spacing?
PCB trace widths and spacings can affect the circuit board in many ways. Here are four areas to consider when deciding what width and spacing values to use:
Electrical Performance and Signal Integrity
Most digital routing on a circuit board will use a default value for its trace widths and spacings, but some nets will require different sizes. Controlled impedance nets, for instance, will need their trace widths calculated based on the configuration of the board layer stackup. Sensitive high-speed traces may require larger spacing values to prevent crosstalk and other signal integrity problems.
Analog routing may also require unique trace widths and spacings depending on the purpose of the circuitry. In some cases, the default trace width may be reduced in tight and constricted areas, but care has to be taken that this isn’t extended across the board. If the trace gets so thin that it gets compromised during PCB fabrication, then the signal integrity of the entire board could be compromised.
Power and Ground Routing
Traces used to route power and ground need to be wider to conduct greater amounts of current. If the traces are too thin, they can get hot and even burn through. Power traces routed on the internal layers of the board also need to be wider for heat dispersal than those routed on the external layers, as exposure to the air will provide more cooling. For those traces that are used in power supply circuitry, it is important to keep them as short and as wide as possible to handle the current, as well as to reduce inductance and noise in the circuit. It is important to increase the spacing for traces that are carrying higher current to prevent the power from arcing between them.
What are the rules of standard PCB trace width?
So far, we have looked at how trace width and spacing restrictions affect the performance of the board electrically, but there are also manufacturing concerns as well. Traces that are too close to each other or to other metal features of the board could potentially develop shorts during fabrication. Each fabricator will have its own minimum trace width that they will build, but 3 mils is a common minimum spacing value. Copper weight also must be factored in here as well.
Here are some other manufacturing considerations for trace width and spacing restrictions:
Traces running between the pads under small surface mount components may have the minimum trace to metal spacing, but can still cause manufacturing problems. The part may not sit squarely resulting in tombstoning, or form a solder bridge with a trace and cause damage if the part is lifted for re-work.
Metal that is too close to the edge of the board could present depanelization problems. Additionally, exposed copper could come into contact with other conductive elements and cause a short on the board.
Traces that are too wide on the surface mount pads could form solder bridges with adjacent pads or traces. These could cause excess current or shorts.
It is also important that drill hole sizes match the traces to which they connect. Although vias run through the board they serve the same function as traces that run along the surface. In many cases, they are extensions of them.
Industry Category