Top 5 Reasons of Using Halogen Free PCB Materials in Manufacturing Process
By:PCBBUY 09/27/2021 10:02
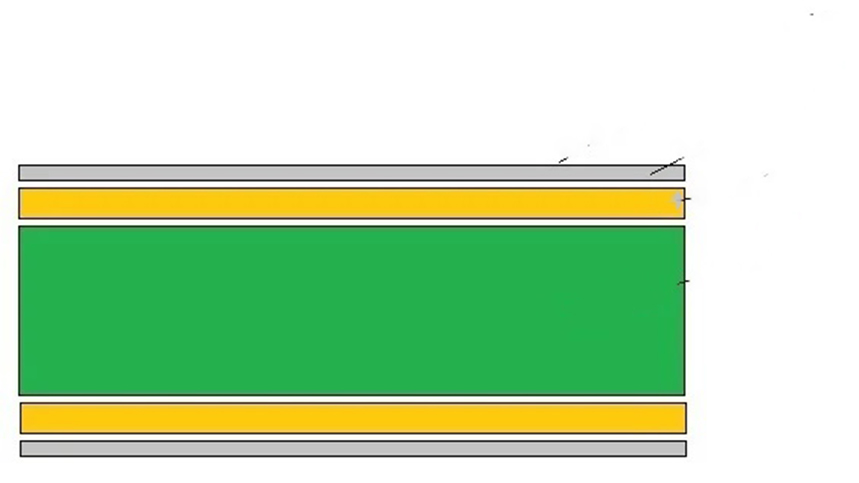
Like the RoHS lead free requirements, halogen free standards require CMs to use new materials and manufacturing methods. Now why is “halogen free” in quotations? It’s because meeting the standard doesn’t necessarily guarantee your board has no halogens in it. For example, the IPC specifies tests for detecting halogens in PCBs, and these tests generally detect ionically bonded halogens. However, most of the halogens found in fluxes are covalently bonded so the test won’t detect them. This means that to make a truly halogen free board, you’ll need to go beyond what the standards specify.
In this passage, we will provide every detail of halogen-free PCB. If you are going to learn more about why we use halogen-free material. Please check and read the content below to learn more professional information.
Why to use halogen-free material for PCB manufacturing?
1. The main advantages of halogen-free material
Halogen-free PCBs can be used in any industry or application where you would use electronic PCB boards, from consumer electronics to industrial automation and everything in between. What are the benefits of using halogen-free PCBs? First, it's important to understand that halogen is not a material in itself. It is a way to describe a class of elemental gases, including fluorine, chlorine, bromine, iodine and astatine. While PCBs containing halogen gases are generally safe, these elements are toxic and can cause reactions from blurred vision and nausea to difficulty breathing and a burning sensation in the eyes, nose and throat.
Although all companies can make use of halogen-free PCBs, they appear most often in companies made a forward commitment to being better to the environment, reducing their carbon footprint and being responsible about the toxins they emit into the atmosphere as a result of their production processes.
2. There are specific technologies of halogen-free material
As an important characteristic of the coating material, it is necessary to maintain sufficient softness while ensuring the flame retardancy. In order to ensure this softness, elastomer is usually introduced into the epoxy resin. However, doing so will have a more serious consequence, that is, the flame retardancy will become worse. Therefore, to solve this problem, researchers usually take the following measures.
· Phosphorous flame retardant is adopted. For example, the use of phosphate ester flame retardant, in the combustion of it can promote dehydration carbonization reaction, so that the surface of the material formed a layer of carbonization film, cut off the contact with oxygen, so that it is difficult to burn.
· Adopt nitrogen-containing flame retardant. Nitrogen atoms are introduced into the molecular structure of the resin to generate an inert gas to oxygen during combustion.
· Adopt inorganic flame retardant. For example, the addition of magnesium hydroxide, aluminum hydroxide and other inorganic filler, they release crystal water in the combustion, reduce the combustion temperature, thereby inhibiting the combustion.
· Resin with special structure is used. For example, epoxy resin containing phenyl alkyl is used in the resin combination.
3. The disadvantages of halogen material
As we mentioned above, Halogen means fluorine (F), chlorine (CL), bromine (Br), iodine (I), Atastatium (At). Additionally, it gets famous as all the halogen elements have numerous advantages for the flame retardant period. Particularly chlorine (CL) and bromine (Br) are frequently utilized in flame retardant for electronics matters.
So many often used printed circuit boards like FR4 PCB, and CEM3 PCB comprise halogen-containing flame retardants. Some institutions researched and have shown us regarding this matter that halogen-containing flame retardant equipment are very harmful to us as it emits a huge quantity of highly destructive and toxic gas with the terrible smell during it gets burning, that has the capacity of affecting our beloved environment furthermore carcinogenic to human beings.
4. Pay attention to the performance of halogen-free material
Insulation
Since P or N replaces halogen, the polarity of the molecular bond of the epoxy resin gets decreased a bit; as a result, it enhances the insulation resistance and the break-down voltage.
Thermal durability
The elements of nitrogen and phosphorus that occur in the halogen-free PCB are much greater than the traditional board; thereby, the grade of monomer molecular weight along with Tg are boosted. The halogen-free PCB has a relatively low coefficient of thermal expansion (CTE) since in the time of heating, the molecular mobility of a halogen-free PCB will exist less than the traditional epoxy resin board.
5. The features of halogen-free PCB pruducts
· Halogen-free material with a low transmission loss characteristic, contributing to higher-capacity and faster data transmission
· Enhanced reliability of equipment operation due to highly heat-resistant, high-reliability multi-layer circuit board material
· The halogen-free material employed improves ease of manufacturing and processing of multi-layer circuit boards with over 20 layers
Industry Category