Top 7 Elements of Impedance Control in PCB Manufacturing
By:PCBBUY 10/30/2021 09:37
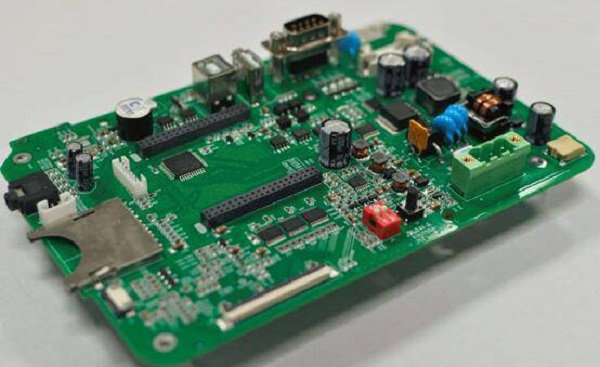
For a specific circuit, the impedance is not constant, but changes with frequency. In a series circuit of resistance, inductance and capacitance, the impedance of the circuit is generally larger than the resistance. That is, the impedance is reduced to the minimum. In the parallel circuit of inductance and capacitance, the impedance increases to the maximum value at resonance, which is the opposite of the series circuit?
In this passage, we are going to provide all the det5ials about PCB impedance. If you are interested in PCB impedance knowledge, you can check and read the content below for more information.
If you want to order PCB product, please check and custom your order online.
1. How to determine PCB impedance?
Usually, trace impedance is between 25 and 125 Ohms and depends on the following factors:
· Copper trace width and thickness
· Passage of the signal through vias
· Core thickness or prepreg material thickness on each side of the trace
· Core and prepreg material dielectric constant
· Distance from the reference copper plane
· Presence or not of solder resist
2. Why to process PCB impedance?
Typically, you will need controlled impedance for PCBs used in high-speed digital applications, such as RF communication, telecommunications, computing using signal frequencies above 100MHz high-speed signal processing, and high-quality analog video such as DDR, HDMI, Gigabit Ethernet, etc.
At high-frequency, the signal traces on a PCB act like transmission lines, which have impedance at each point on the signal trace trajectory. If this impedance varies from one point to the next one, there will be a signal reflection whose magnitude will depend on the difference between the two impedances. The larger the difference is, the greater the reflection will be. This reflection will travel in the opposite direction of the signal, which means that the reflected signal will superimpose on the primary signal.
3. What are the applications of PCB impedance control?
Controlled Impedance should be considered for PCBs used in fast digital applications such as:
· Telecommunications
· Computing 100MHz and above
· High Quality Analog Video
· Signal Processing
· RF Communication
4. What are the factors for PCB impedance control?
Some of the variables on which the impedance of a trace is dependent on are more or less fixed by the PCB manufacturer and some of them are defined by the PCB designer. Power is transmitted uniformly across the length of the trace across the PCB when there is uniform impedance. Therefore, a trace that has a very uniform cross-sectional geometry needs to be constructed.
In other words, the shape and size should be as uniform as possible running across a consistent dielectric constant of the material that it’s running along the length for a given routing layer. And, the more uniform the trace the more consistent the dielectric constant and we will achieve more consistent impedance and less power degradation.
5. How does PCB impedance control work?
· No impedance control: This is a situation where you do not need any extra design elements to ensure correct impedance because you have very loose impedance tolerance. Naturally, this will result in a faster-completed, less expensive board because the manufacturer does not have to include any special measures.
· Impedance watching: What is impedance watching? This is a situation where the designer will outline the impedance control trace, and the PCB provider adjusts the trace width and dielectric height accordingly. Once the manufacturer approves these specifications, they can begin to manufacture the board. You can request a time-domain reflectometry (TDR) test to confirm the impedance for a fee.
· Impedance control: Actual impedance control is something you will typically only request when your design has tight impedance tolerances that could be tough to hit the first time around. When the capability limits of the manufacturer get close to the dimension requirements, it can be tough to ensure target impedance on the initial attempt.
6. How to control dielectric of PCB impedance?
The typical design considerations involved in the determination of the requirement for controlling the impedance are the strength of the signals involved, the susceptibility of the circuit to noise and signal distortion, the criticality of signal timing and the speed at which the signal’s source is attempting to force a change in voltage and/or current.
7. What is power delivery network of PCB impedance?
Your power delivery network will exhibit capacitive impedance at lower frequencies and reduces to the resistance of your power bus in series with your load components and ground return path at DC. This impedance is dominated by the physical separation between your power rails, traces, and internal planes in your board. As the driving frequency increases, mutual inductance between circuits in your board will cause the impedance of your power delivery network to increase. Eventually, the impedance of your power delivery network will exhibit many peaks at high frequencies.
Ideally, the impedance of your power delivery network should be flat within the band you want to work in. For digital signals, the relevant bandwidth is all frequencies between the clock rate and the knee frequency (0.35 divided by the signal rise time). If all harmonics that comprise a digital signal see the same frequency, then the transfer function for a return signal in a ground plane will be flat. The same ideas apply to analog signals travelling throughout your board and ground planes.
Industry Category