Top 7 Important Elements of PCB Impedance Control Requirements
By:PCBBUY 11/23/2021 09:29
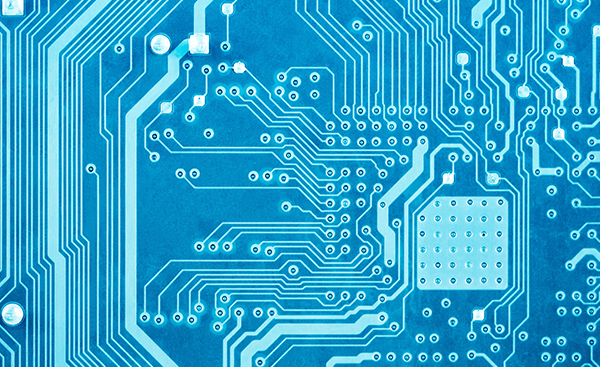
Controlled impedance is a way of predetermining an electric circuit’s resistance to alternating current. That resistance arises as a function of both resistance and reactance within the circuit. Impedance is critical to a circuit’s operations because it affects the schedule on which a circuit completes its functions. It impacts the timing – and integrity – of essential processes. Controlling impedance by altering the physical structure of board components to give the impedance a particular value helps the board act as it was designed to. Controlled impedance is often a design consideration for high-frequency analog circuits or high-speed digital circuits.
In this passage, we will focus on the topic of PCB impedance control requirements. If you are going to learn the details of PCB impedance control, please check and read the content below in this passage.
What is the importance of PCB impedance control?
Typically, you will need controlled impedance for PCBs used in high-speed digital applications, such as RF communication, telecommunications, computing using signal frequencies above 100MHz high-speed signal processing, and high-quality analog video such as DDR, HDMI, Gigabit Ethernet, etc.
At high-frequency, the signal traces on a PCB act like transmission lines, which have impedance at each point on the signal trace trajectory. If this impedance varies from one point to the next one, there will be a signal reflection whose magnitude will depend on the difference between the two impedances. The larger the difference is, the greater the reflection will be. This reflection will travel in the opposite direction of the signal, which means that the reflected signal will superimpose on the primary signal.
As a result, the original signal will be distorted: the signal intended to be sent from the transmitter side would have changed once it gets to the receiver side. The distortion may be so much that the signal may not be able to perform the desired function. Therefore, to have undistorted signal travel, the PCB signal traces must have a uniform controlled impedance to minimize signal distortions caused by reflections. This is the first step to improve the integrity of the signals on the PCB traces. For better understanding, read the effects of high-speed signals in a PCB design.
What are the factors of PCB impedance control requirements?
Many factors influence the stack-up design parameters and choices (such as impedance, physical structure, blind holes, and so on). The impedance of signal lines is affected by the stack-up structure characteristics. Change the stack-up parameters help attain target impedance. It is equally important to examine and balance other aspects in design that impact the stack-up. Consider the following:
· The thicker the dielectric thickness, the higher the impedance
· The smaller the dielectric constant, the greater the impedance
· The thicker the copper weight, the lower the impedance
· The impedance value will be higher if the dielectric constant is less
· A greater inductance indicates a higher impedance
· A higher capacitance indicates a lower impedance
What are the causes of PCB impedance control requirements?
As an example of the problems caused by incomplete information, let’s look in on a front-end pre-production engineer, who is preparing your 6-layer PCB Gerber files for production using CAM software late one Friday afternoon in June. In this example, we will say that the job originated as an online order, which means the engineer is the first person in the fabricator’s organization to review the data files. The drawing notes appear to be reasonably complete – copper weights, mask color, surface finish, etc. are all there. So far, so good, it would seem. But the devil is in the details.
The next note specifies impedance control: single-ended 50 Ohms, and differential 100 Ohms. A glance at the drawing shows that the 6-layer PCB consists of four signal layers, and two planes, arranged as TOP, GND, SIG3, SIG4, PWR, and BOT. The engineer wonders: Is impedance control required for all four signal layers? Or if not, then for which individual layers? And what trace width needs to be controlled?
Remember that the answers to these questions will dictate material selection, CAM data adjustments, artwork scaling, and design of the impedance coupons. Now we see the CAM engineer composing an on-hold notification before going on to the next order in the work queue, instead of tooling your order for manufacturing. Hopefully the PCB designer hasn’t left for a two-week vacation in a place with no cell phone service, or the order may remain on hold for a while. With only slight variations, this scenario is all too common.
What are the considerations of PCB impedance control requirements?
To ensure that the same impedance values are maintained throughout the length of a controlled trace, the following parameters must be considered for routing:
· Trace geometry: The width and thickness (copper weight) of the trace being routed.
· Signal spacing: The spacing between the signal trace and its return path is usually on the adjacent reference plane layer. This will be controlled with the configuration of the board layer stackup.
· Dielectric material: The core and prepreg materials used on either side of the controlled impedance trace layer. Their thickness and dielectric constant will be part of the impedance calculations.
Industry Category