Types of vias in PCB design
By:PCBBUY 08/17/2021 17:14
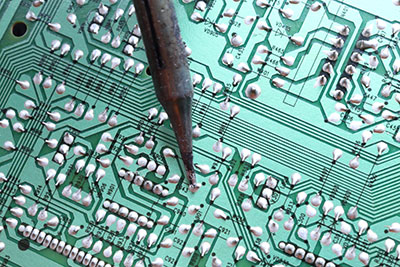
For most of the PCB lovers, you may know the definition of vias. In short, vias are holes that pass through the layers of the board for electric conduction of PCB. The functions of each hole as a conductive path through which electrical signals are passed between the layers. However, for designers, how to choose the vias for the boards? There are various options when it comes to vias on a PCB.
If you are curious about the vias during the PCB design process, please check this article and read the content we provide. You could learn more professional knowledge about PCB vias in design. Let’s check it!
If you want to order PCB product, please check and custom your order online.
What are the main types of vias in PCB design?
There are several types of vias of PCB. Among them, there are 2 main types: the blind hole and the buried hole.
In blind vias, the hole penetrates the top or bottom layer of the board but stops before any of the inter layers. Blind vias are named as such because you cannot see through them when you hold a board up to the light. As for buried via, might appear through one or more internal layers. For a multi-layer board to have a blind layer, the hole plating on the inter layer must be completed early on during PCB assembly process, before the top and bottom layers are applied to the board.
And here are the introductions of different types of vias:
What is through hole?
Among all the vias in PCB design, the most obvious type of via is the plating through-hole, which penetrates all the layers in a multi-layer board. Usually, Through-holes are typically larger than blind holes and buried holes and are also a lot easier to identify with the naked eye. The light will pierce right through a plating through-hole when hold a board up before the light. Besides, Through-holes are also easier to make because you can simply drill right through all the layers.
With the growing popularity of small, compact, mobile computing devices and electronic gadgets, PCBs are being designed with few, if any, through-hole components. As such, there are few remaining reasons for PCB designers to continue using boards that contain large through-holes, as these consume lots of space on a board that could be put to more efficient use with microvias. In fact, for designers to keep their boards small, microvias and surface mounts should be used as much as possible. As the trend continues, through-holes will likely be phased out entirely in the years ahead.
What is Microvia?
Usually, vias that are under 150 microns are known as Microvia. In the PCB design, the designers prefer Microvia because of the small size of the hole, which consumes far less space on the board than the holes that require more drilling. The layers are connected to one another with copper plating in Microvia. In some cases, a microvia will penetrate two whole layers. The blind vias that fit this description are known as skip vias. However, skip vias are not recommended by manufacturers because the nature of the hole can result in complications with plating.
In the PCB manufacturing process, microvia are drilled by lasers and have a smaller diameter compared to the standard through-hole vias. And we divide microvia into 2 types - stacked vias and staggered vias according to the location in the PCB layers.
Microvias reduce the layer count in printed circuit board designs and enable higher routing density. Microvias improve the electrical characteristics and also allow miniaturization for higher functionality in less space. It makes room for large pin-count chips that can be found in smart phones and other mobile devices. Besides, there is another type of microvias called skipvias. Skipvias skip one layer, meaning, they pass through a layer making no electrical contact with that specific layer. The skipped layer will not form an electric connection with that via. Stacked vias are piled on top of one another in different layers and staggered vias are scattered in the different layers. And they are more expensive.
What is VIA-in-Pad?
Recently, one of the popular via process of PCB design involves the application of vias on BGA pads, also known as via-in-pad. The design has become popular because it makes it possible for manufacturers to minimize the amount of space required for vias. As a result, via-in-pad allows manufacturers to make smaller printed circuit boards that require less space to route signals. Via-in-pad is an optimal technology for today’s compact electronic and computing devices.
There are some disadvantages, it will also popular in the PCB design with the advantages. Costs aside, you can make smaller boards with via-in-pad and ultimately make smaller devices. For certain modern gadgets and mobile devices, the via-in-pad design might be your only option. The via-in-pad design is especially convenient for routing because the holes connect straight to the layer that underlies the component, making it possible to route signals without the risk of going outside the perimeter of the device’s footprint.
How to select the vias during PCB design?
For designers, the best way is to choose the vias according the size and application. Typical mechanical drills don’t go much lower than 12 mil in diameter, so the manufacturer will increase the cost to account for broken drills. For some of these older devices, your only option would likely be a larger mutilayer PCB with through-hole components. If you are designing a PCB for a smaller device, there is really no reason to use through-hole components since you will need to maximize the small amount of space on the tiny board that would fit the device.
The vias ensure a secure solder joint for the thermal pad and prevent solder from floating the package during assembly, which could hamper forming good solder joints at the QFN contacts.
An assembly shop can compensate for a lack of through vias in a thermal pad by adding windowpane-shaped opening in the solder paste stencil above the pad, to relieve solder pooling and outgassing during assembly, but the fix is less effective than if vias were present.
The pad matrix on which a BGA will be installed may include through vias and blind vias, but all of them must be filled and planarized, otherwise solder joints will be compromised.
Incorporate vias in the thermal pads under QFNs to help solder flow through to conductive planes.
Use maximum micro via structures in your design. Keep the aspect ratio minimum. This provides better electrical performance and signal integrity. Lower noise and crosstalk, and lower EMI/RFI.
Via-in-pads must be filled, unless they reside in thermal pads. Implement smaller vias. This can help you build an efficient HDI PCB since the stray capacitance and inductance gets reduced.
Industry Category