What Are 5 Factors Did the Technician Considered in Etching the PCB?
By:PCBBUY 08/16/2022 16:32
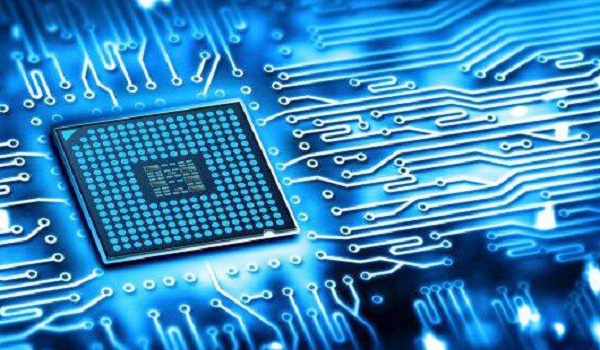
The etching process is one of the major steps in the final processing of printed circuit boards (PCBs). This process removes excess copper so as to reveal the desired circuit patterns. In the PCB etching process, all copper is removed except the circuitry that is protected by the tin plating that was applied during the previous treatment in PCB manufacturing. The tin is then stripped and the copper is cleaned and the newly prepared circuit is ready to move on to the next step in manufacturing.
Are you curious about etching the PCB? If you are curious about more information about etching the PCB, please check and read the content below for more professional knowledge.
What are the main types of etching the PCB?
PCB etching is the process of removing copper from a circuit board layer that is not protected by the hardened photoresist by immersing it in a chemical solution. The etching used by industrial circuit board fabricators is broken into two different processes: acidic etching and alkaline.
Acidic etching
Acidic etching is used for removing copper from internal layers in standard rigid FR-4 circuit boards due to its precision and less aggressive action. The acidic process won’t react with the photoresist and will produce less of an undercut in the metal it etches. The trade-off, however, is that acidic etching will take longer than other methods.
Alkaline etching
Alkaline etching is used for the outer layers of the circuit board, where a quicker process is more to maintain the uniformity of the remaining copper. Alkaline is more active than acidic and requires careful monitoring to ensure its accuracy.
The acidic and alkaline etching processes are ideal because they have a high etching rate at a relatively low operational cost and effectively etch many different metal materials. PCB fabricators must precisely maintain their etching processes to guard against exposure to hazardous liquids and fumes and prevent any chance of water contamination. Now, let’s see how this etching is used in the fabrication of printed circuit boards.
What are the advantages and disadvantages of etching the PCB?
Advantages of wet PCB etching
· The most important advantage of wet PCB etching is that it can be conducted in a normal atmospheric environment.
· High etching rate
· Low operational cost
· High selectivity: wet etching can be used to etch off a wide range of materials.
· Ease of equipment maintenance
Disadvantages of wet PCB etching
· Inadequate power to etch traces <1μm.
· High use of chemicals
· Creating a significant amount of hazardous chemical waste
· The risk of wafer contamination
· Chemical hazards
· Direct exposure to liquids
· Direct and indirect exposure to fumes
What are the types of chemical solution used in PCB etching?
The etch rate is stable. It is particularly suitable for producing the correct topography and cleanliness for hot air levelling. It is non foaming and sprayable.
150 MG copper etchant
It is a proven etchant, specially designed for etching copper in the manufacturing of printed circuit boards during mass production. MG Etchant chemicals are based on ammoniac compounds in highly selected proportions. It can be used in spray or immersion application.
1932 Nickel cleaner
It is an aquoues solution of acidic chemical components used to restore the solderability of nickel plated and nickel alloy surfaces. Tarnish can be removed by immersing the part for 15-20 seconds at room temperature. Immersion time can be reduced if the solution is warmed up to 74°C . After treatment the part should be thoroughly cleaned through hot water spray, followed by cold or hot water immersion.
6401 Solder stripper
It is an acid based stripper designed to be used for stripping tin, tin / lead and lead from PCBs. It is extremely economical and will hold in excess of 15 oz. per gal. without replenishment. It contains a unique stabilizer, copper inhibitor system which reduces base metal etching during stripping.
6810 Resist stripper
It is a concentrated alkaline solution formulated specially to remove alkaline soluble dry films and silk screen printing inks from printed circuits boards. It contains no organic solvents and can be used in dip tanks and spray equipment.
8200 De-foamer
It is an alkaline, non-silicon de-foamer (foam suppressant) used in conjunction with all alkaline resist stripper and developer solutions. It is recommended for use in conveyorised spray machines. It operates over a wide temperature range, which allows it to be used where necessary to control excessive foaming
Industry Category