What Are Causes of PCB Delamination?
By:PCBBUY 03/18/2024 14:27
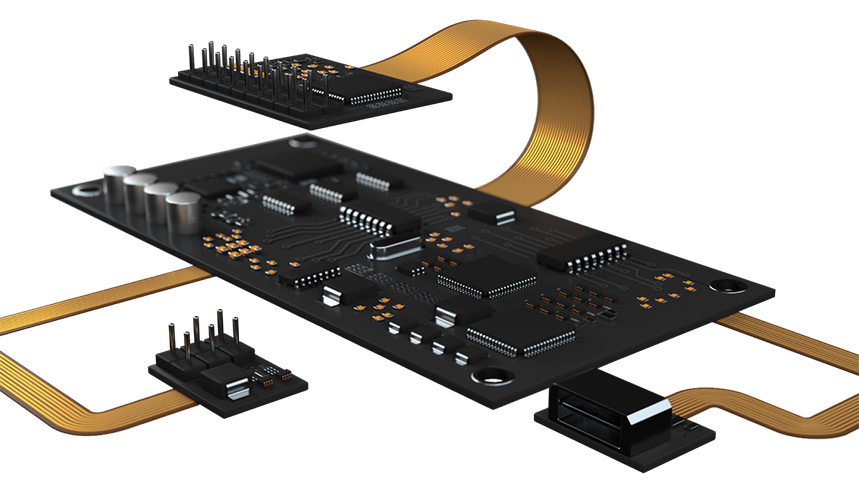
Delamination is when the layers of your PCBbase materials experience a partial separation. This will cause gaps or bubbles that look like blisters. Delamination typically occurs in the production process when unwanted heat or humidity is present.
Measling is the presence of white spots in the PCB weave interior. They signal a destruction of the elements in the board, but some small measling can be within your tolerance as long as they are not very frequent or you don’t have measling that bridges conductors and soldering eyes. Stress and production can produce measling.
In this passage, we are providing all the basic information about PCB delamination. If you are looking for the causes of PCB delamination, please check and read the content below for more knowledge.
What Are Causes of PCB Delamination?
What is delamination’s most likely cause? It can happen due to one factor or a combination of several:
Moisture
Moisture is the most common culprit. Even a small amount trapped within the board can result in damage. High temperatures turn the moisture into steam, and the resulting expansion can cause both internal and external cracking.
It’s essential to understand why moisture can enter a PCB. Typically, it’s the result of poor bonding and a lack of proper adhesive when attaching layers.
Thermal Stress
Additionally, PCB delamination is possible due to thermal stress when production or repair. Thermal stress is any change to the size, fit, or placement of a component, typically a mechanical component, caused by excess heat.
Thermal-stress delamination occurs in a similar way to the damage from moisture. The excess heat creates a gas from inorganic materials, causing layers of the PCB to separate.
Additional Factors
Delamination doesn’t always have a single cause. Instead, a combination of poor manufacturing processes, low-quality materials, and more can all contribute to moisture buildup. Even something as simple as using FR-4 material with the incorrect type of Tg can result in delamination.
How can PCB delamination be avoided?
At ESO, the following processes are implemented in order to prevent PCB delamination: PCB Drying (baking) before assembly of electronic components. Double-layer PCBs are not typically dried unless they have copper planes that do not have a grid pattern. Multi-layer and rigid-flex PCBs are always dried. Rigid-flex PCBs are especially susceptible to delamination because of their hygroscopic glue that is used to connect the rigid and flex parts. The length of time for which PCBs are baked depends on their technical characteristics.
If PCBs will be stored indefinitely, they are properly treated with nitrogen before being sealed in a dry bag. Alternatively, they may be sealed and dated in a dry bag with a silica bag to prevent moisture buildup.
Why to process PCB delamination?
The main reason why FR4 PCB's delaminate during the reflow soldering process is due to moisture being present within the FR4 material that has expanded causing internal layers to separate - see photo above.
It is important to be sure that the correct grade of material is being used with an appropriate specification for the intended assembly process. For example if the assembly is 'Lead-Free' then generally a higher reflow soldering temperature will be needed and therefore a material with a higher Tg (Glass Transition Temperature).
Although the presence of moisture can cause the FR4 layers to separate, quite often the root cause of the problem could be due to a defect during the PCB manufacturing process.
FR4 is a 'Hygroscopic' material and will absorb moisture from the atmosphere and so once the PCB's are fabricated they should be vacuum sealed. If there is concern over the way in which the PCB's have been sealed then the PCB's should be pre-baked prior to assembly to remove moisture following the guidelines detailed in IPC 1601.
Industry Category