What Are Effective Tips to Test a PCB Capacitor?
By:PCBBUY 05/26/2025 17:15
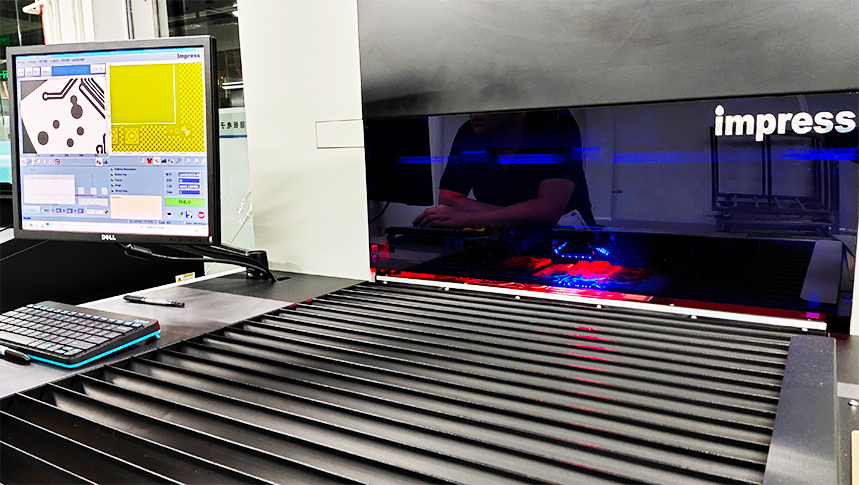
Introduction: The Critical Role of Capacitors in PCBs
Capacitors are ubiquitous passive components in printed circuit boards (PCBs), serving essential functions such as filtering, energy storage, signal coupling, and voltage regulation. Despite their small size, capacitors significantly impact circuit performance, reliability, and longevity. However, deviations in capacitance, equivalent series resistance (ESR), dielectric integrity, or voltage ratings can lead to failures, especially under harsh environmental or operational conditions. Effective testing is paramount to ensure capacitors meet design specifications, comply with industry standards, and avoid costly field failures. This guide explores advanced testing techniques, supported by principles, data, and practical recommendations.
Understanding Capacitor Parameters: Foundations for Testing
Before diving into testing methods, it’s essential to grasp the key parameters that define a capacitor’s behavior:
-
Capacitance (C): Measured in farads (F), it quantifies the ability to store electrical charge. Tolerance (e.g., ±10%, ±5%) determines acceptable deviations.
-
ESR: Represents internal resistance, critical for high-frequency applications and ripple current handling. Typical values range from 0.01 Ω (ceramic capacitors) to 100 Ω (electrolytic capacitors).
-
Equivalent Series Inductance (ESL): Affects performance in switching circuits. Ceramic capacitors have lower ESL (0.1–1 nH) compared to electrolytic types (1–10 nH).
-
Dielectric Absorption (DA): Relates to dielectric material quality, influencing charge retention. High DA can cause voltage droop in analog circuits.
-
Voltage Rating: Maximum safe operating voltage (e.g., 16V, 50V). Testing must verify breakdown voltage (often 150% of rated voltage).
-
Temperature Coefficient: Capacitance variation with temperature, expressed as parts per million (PPM) per °C. Ceramic capacitors (e.g., X7R) exhibit ±15% capacitance change across -55°C to 125°C.
Table 1: Key Parameters for Common PCB Capacitors
Capacitor Type |
Capacitance Range |
ESR (100 kHz) |
ESL |
Voltage Rating |
Temperature Coefficient |
MLCC Ceramic (X7R) |
1 nF – 10 µF |
0.1–100 Ω |
0.1–1 nH |
50V |
±15% (-55°C to 125°C) |
Tantalum (Solid) |
1 µF – 100 µF |
10–100 mΩ |
1–5 nH |
50V |
±1% |
Aluminum Electrolytic |
1 µF – 100 mF |
1–20 Ω |
5–20 nH |
16V–450V |
±20% |
Core Testing Methods: Principles and Applications
1. Capacitance Measurement
Principle: Uses an LCR meter to apply an AC signal and measure reactance.
-
Frequency Selection: Ceramic capacitors test at 1 kHz, electrolytic capacitors at 100 kHz (to account for ESR effects).
-
Fixture Parasitic Compensation: Subtract test fixture capacitance (typically 0.2–0.5 pF) to avoid measurement errors.
-
Tolerance Check: Compare measured capacitance against rated value. For example, a 10 µF capacitor with ±10% tolerance should read between 9 µF and 11 µF.
Data Example: A 10 µF electrolytic capacitor may measure 9.8 µF at 100 kHz due to ESR and ESL influences.
2. ESR and ESL Testing
Principle: ESR dominates at moderate frequencies (100 kHz–1 MHz), while ESL becomes significant at higher frequencies.
-
Equipment: Precision LCR meters (e.g., Keysight E4980A) or specialized ESR meters.
-
Four-Wire Kelvin Connection: Minimizes contact resistance errors, critical for low-ESR capacitors (e.g., tantalum).
-
Frequency Sweep: Analyze impedance curves to separate ESR and ESL contributions.
Table 2: ESR and ESL Comparison Across Capacitor Types
Capacitor Type |
Test Frequency |
ESR (Typical) |
ESL (Typical) |
MLCC Ceramic (X7R) |
1 MHz |
10–50 mΩ |
0.5 nH |
Tantalum (Solid) |
100 kHz |
100 mΩ |
2 nH |
Aluminum Electrolytic |
100 kHz |
2–5 Ω |
10 nH |
3. Dielectric Leakage and Breakdown Voltage
Principle: Applies a controlled overvoltage to test dielectric integrity.
-
Standard Protocol: Gradually ramp voltage to 150% of rated voltage (IEC 62371). For a 50V capacitor, test up to 75V.
-
Leakage Current: Measure under rated voltage. Ceramic capacitors typically exhibit <1 nA leakage, while electrolytic capacitors may reach µA levels.
Failure Mode: Short-circuit or flashover indicates dielectric breakdown.
4. Temperature and Bias Testing
Principle: Evaluates capacitance stability under operational stressors.
-
Bias Tee Setup: Apply rated voltage while measuring capacitance across temperatures (-55°C to 125°C).
-
Thermal Shock: Rapid cycling between extremes to replicate field conditions.
Table 3: Capacitance Variation With Temperature
Capacitor Type |
Capacitance Change (-55°C to 125°C) |
X7R Ceramic |
±15% |
COG Ceramic |
±3% |
Tantalum |
±1% |
Advanced Techniques: Impedance Analysis and Aging Tests
Impedance Spectroscopy
-
Application: Maps impedance vs. frequency to decouple ESR, ESL, and capacitance. Useful for ceramic and film capacitors.
-
Equipment: Precision impedance analyzers (e.g., Solartron 1260A).
-
Data Example: A 1 µF tantalum capacitor may show 100 mΩ ESR and 2 nH ESL at 100 kHz.
Aging Tests
-
Objective: Mimic long-term degradation. Apply rated voltage and temperature for 1,000–10,000 hours (AEC-Q200 standard).
-
Metrics: Capacitance drift, ESR increase, and leakage current rise. Tantalum capacitors often outperform aluminum electrolytic in aging tests.
Case Study: Field Failure Analysis
Scenario: An automotive PCB experienced intermittent startup issues. Testing revealed:
-
Visual Inspection: Swollen aluminum electrolytic capacitors (Fig. 1A).
-
ESR Testing: ESR increased from 2 Ω (new) to 8 Ω (aged).
-
Breakdown Voltage: Failed at 65V (rated 50V), indicating dielectric degradation.
-
Root Cause: Thermal cycling caused electrolyte drying, reducing capacitance and increasing ESR.
Industry Standards and Compliance
-
IEC 62371: Dielectric testing protocols.
-
AEC-Q200: Automotive-grade stress tests (temperature cycling, load life).
-
MIL-STD-810: Military standards for shock/vibration resilience.
-
EN 60364: Safety requirements for consumer electronics.
Best Practices for Capacitor Testing
-
Select Appropriate Tools: Use LCR meters for routine tests, impedance analyzers for ESL/DA.
-
Control Environmental Conditions: Maintain 23°C ± 5°C and <60% RH during tests.
-
Document Aging Trends: Track capacitance/ESR drift over time using automated testers.
-
Prioritize Standards Compliance: Align testing with AEC-Q200, IEC, or MIL-STD protocols.
Reference
-
Keysight Technologies, Precision LCR Measurement Handbook, 2023.
-
IEC 62371, Test Methods for Electrical Contenders, Edition 3.0.
-
Murata Manufacturing, Capacitor Reliability Whitepaper, 2022.
-
NASA TMC-LP-003, Space-Grade Capacitor Testing Procedures, 2021.
-
AEC-Q200 Rev. D, Stress Test Specifications, Automotive Electronics Council.
Industry Category