What Are Front-end Simulation and Evaluation in PCB Industry?
By:PCBBUY 10/24/2023 16:51
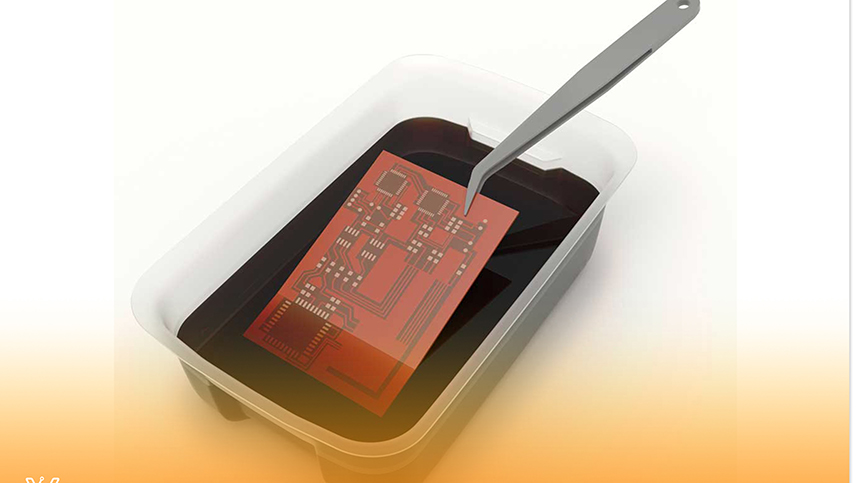
PCB simulations begin in the schematic capture phase of a design project, where SPICE simulations are used as part of circuit design. SPICE simulations are important for evaluating system-level electrical behavior, but they are also useful for circuit optimization as part of the design process. Schematic capture software with a built-in SPICE simulation package can help you stay productive while you work through some of the basic simulations needed to evaluate electrical behavior.
SPICE packages that are used for front-end engineering and simulations are designed to perform a specific set of analyses:
· DC sweeps, where input DC voltage is swept through a series of values and the voltage and current at other nodes are monitored
· Transient analysis, or time domain mixed-signal simulations; this is the fundamental time-domain simulation
· AC sweeps, or frequency sweeps, where the frequency of an AC signal is varied in time
· Parameter sweep, where a specific set of component parameters is swept across a range of values
· Pole-zero analysis, where stability conditions and transient oscillation frequencies can be visualized in a single graph
Some schematic capture programs with integrated SPICE engines can be used with more advanced simulations, such as noise analysis and thermal analysis.
What are the common problems of circuit simulation in PCB manufacturing?
While SPICE circuit simulators can tell you whether or not the circuit concept will work, the actual physical layout of the circuit still needs to be refined for the circuit board’s maximum performance. The circuit analysis for these refinements also used to require time-consuming and expensive testing of prototype circuit boards. However, design engineers can analyze from within the design tools while the board is still being laid out.
Impedance
Impedance analysis must be done before layout to determine the trace widths for the layer stackup of a circuit board. To control the impedance of high-speed transmission lines, it is essential to carefully calculate the board dielectric materials and width and the width and spacing of the traces. Some CAD tools also offer impedance checking during layout to confirm that the transmission line traces being routed are maintaining their target impedance values. Impedance analysis is important for combatting reflection and other signal integrity problems.
High-speed timing
DDR (Double-Data Rate) and other high-speed routing topologies depend on accurate trace lengths to support the timing requirements of their circuits for the best performance of the board. Many of these trace lengths also need to be matched to prevent one line from being faster than another, and the CAD tools will analyze the routing and report any problems.
Crosstalk
When a strong signal overpowers a weaker signal due to its proximity, it can result in the weaker signal mimicking its behavior instead of accomplishing its task. This condition is known as crosstalk, and it can create signal integrity problems that will degrade the board’s performance. Crosstalk analysis is an essential layout tool that designers should be acquainted with and regularly use.
Return paths
The clear return path of high-speed signals on the reference plane is another essential signal integrity check to minimize the amount of electromagnetic interference (EMI) the board is generating. Return path analysis tools can tell layout designers immediately if their boards will potentially generate too much noise.
Power integrity
When laying out a circuit board, it can be very easy to miss small details in the design, such as a power pin not having enough metal for a robust connection. Although there may be enough metal to pass the design rule check, in reality, there isn’t enough to support the amount of voltage that the pin will conduct. Power integrity analysis tools can give the designer immediate feedback during layout and determine which pins need a stronger connection to satisfy the power requirements.
Design rule checks
Although not considered an “analysis” tool, a designer should always check the layout’s basic design rules and constraints before sending it out for manufacturing. Circuit board fabricators and assemblers often find simple errors that should have been caught in design but weren’t because the rules were either not set up correctly or not used at all. Thankfully the design rules in today’s CAD systems are very comprehensive and often include a 3D display and checking for a complete object clearance verification.
Industry Category