What Are Manufacturing and Performance Requirements of Flexible PCBs?
By:PCBBUY 12/25/2024 16:11
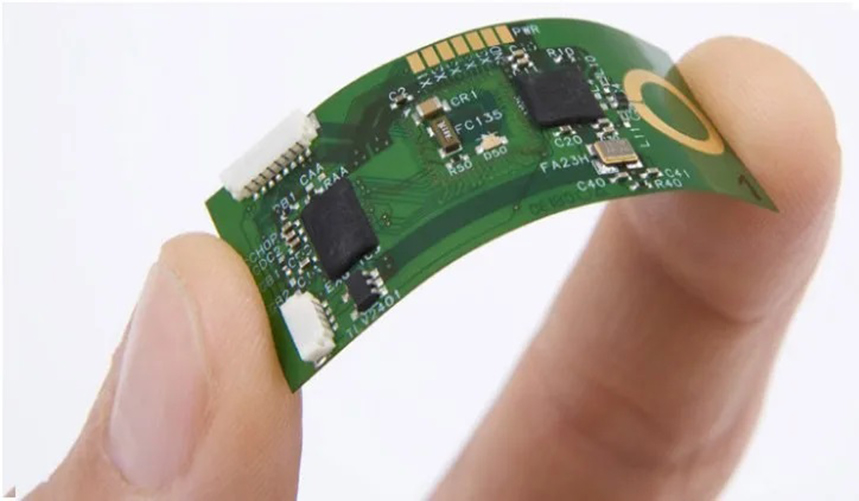
Flexible printed circuit boards (FPCBs) are pivotal in modern electronics, offering unmatched flexibility and durability. This comprehensive guide delves into the various aspects of FPCBs, including their definition, performance, applications, classification, structure, and current technological status. Additionally, it covers the materials and design standards of FPCBs, focusing on flexible dielectric films, copper foils, cover layers, reinforcement plates, and the coefficient of thermal expansion. Finally, it outlines the manufacturing processes and performance requirements of FPCBs.
What Is Overview of Flexible PCBs?
Performance
FPCBs are renowned for their flexibility, lightweight nature, and space-saving capabilities. They can withstand mechanical stress and dynamic flexing, making them ideal for applications requiring frequent movement.
Applications
FPCBs are widely used in various industries, including:
Consumer Electronics: Smartphones, tablets, and wearable devices.
Automotive: Dashboard displays, sensors, and lighting systems.
Medical Devices: Portable diagnostic tools and implantable devices.
Aerospace and Defense: Avionics systems and communication equipment.
Classification
FPCBs can be classified based on their structure and application:
Single-sided FPCBs: One conductive layer.
Double-sided FPCBs: Two conductive layers with vias connecting them.
Multilayer FPCBs: Multiple conductive layers separated by insulating layers.
Rigid-Flex PCBs: Combination of flexible and rigid sections.
Structure
The basic structure of an FPCB includes:
Flexible Substrate: Usually made of polyimide or polyester.
Conductive Layers: Typically copper foils.
Adhesive Layers: Bind the conductive layers to the substrate.
Cover Layers: Protective layers on top of the conductive pattern.
Technological Status
FPCB technology continues to advance, with ongoing research focused on improving material properties, manufacturing processes, and reliability. Innovations include the development of new flexible materials, enhanced adhesive systems, and more precise manufacturing techniques.
What Are the Materials and Design Standards for Flexible PCBs?
Flexible Dielectric Films
Flexible dielectric films are crucial for FPCBs, providing electrical insulation and mechanical support. The most common materials are:
Polyimide: High thermal stability, excellent mechanical properties.
Polyester: Cost-effective, good mechanical properties but lower thermal stability.
Copper Foil
Copper foils serve as the conductive material in FPCBs. Key properties include:
Thickness: Typically ranges from 12 µm to 70 µm.
Adhesion Strength: Critical for maintaining the integrity of the circuit.
Surface Finish: Affects solderability and corrosion resistance.
Cover Layers
Cover layers protect the conductive pattern from environmental damage and mechanical wear. Materials used include:
Polyimide Films: Offer excellent thermal and mechanical properties.
Liquid Photoimageable (LPI) Solder Masks: Provide high-resolution patterning and protection.
Reinforcement Boards
Reinforcement boards enhance the mechanical stability of FPCBs in specific areas, usually where components are mounted or where connectors are located. Common materials include:
FR-4: A composite material of woven fiberglass cloth with an epoxy resin binder.
Stainless Steel: Provides additional rigidity and strength.
Coefficient of Thermal Expansion (CTE)
The CTE of FPCB materials affects their performance under temperature variations. Matching the CTE of different materials is crucial to prevent mechanical stress and delamination. Typical values include:
Polyimide: ~20 ppm/°C.
Copper: ~17 ppm/°C.
What Are Manufacturing and Performance Requirements of Flexible PCBs?
Manufacturing Process
The manufacturing of FPCBs involves several key steps:
1. Substrate Preparation: Cleaning and treating the flexible substrate.
2. Copper Cladding: Laminating copper foil onto the substrate.
3. Patterning: Creating the circuit pattern using photolithography or etching.
4. Drilling: Creating vias and holes for interlayer connections.
5. Plating: Electroplating the vias and surface pads.
6. Cover Layer Application: Applying cover layers to protect the circuit.
7. Testing: Conducting electrical and mechanical tests to ensure quality.
Performance Requirements
FPCBs must meet stringent performance requirements to ensure reliability in their applications. Key parameters include:
Parameter |
Requirement |
Thermal Stability |
Withstand temperatures up to 250°C |
Flexibility |
Endure bending radius as low as 1 mm |
Adhesion Strength |
>1 N/mm² |
Electrical Conductivity |
Low resistance, high conductivity |
Mechanical Strength |
High tensile strength, >150 MPa |
Chemical Resistance |
Resist solvents, acids, and alkalis |
Data Table Example
Material |
Thermal Stability (°C) |
Flexibility (Bend Radius) |
Tensile Strength (MPa) |
Adhesion Strength (N/mm²) |
CTE (ppm/°C) |
Polyimide |
250 |
1 mm |
200 |
1.5 |
20 |
Polyester |
150 |
2 mm |
150 |
1.0 |
60 |
Copper |
1085 |
- |
210 |
- |
17 |
Technological Advances and Challenges
Material Innovations: Development of new polymers with enhanced properties.
Manufacturing Precision: Improvements in photolithography and etching techniques.
Reliability Testing: Advanced testing methods to simulate real-world conditions.
Flexible PCBs have come a long way since their inception, evolving into a critical component of modern electronics. Their unique properties, such as flexibility, lightweight nature, and durability, make them indispensable in a wide range of applications. With ongoing advancements in materials, manufacturing processes, and integration with emerging technologies, the future of FPCBs looks promising. As the demand for smaller, more powerful, and versatile electronic devices continues to grow, FPCBs will play a pivotal role in shaping the next generation of technology.
The Evolution and Current State of Flexible PCB Technology
Flexible printed circuit boards (FPCBs) have revolutionized the electronics industry by offering unparalleled flexibility, durability, and adaptability. This article delves into the development process of FPCBs, tracing their historical advancements, and examines the current technological state of these essential components. By exploring the innovations and challenges in FPCB technology, we can appreciate their significance in modern electronics.
Evolution of Flexible PCB Technology
Early Developments
The concept of flexible circuits dates back to the early 20th century, with initial experiments involving printed wiring on flexible substrates. However, it wasn't until the 1950s and 1960s that significant progress was made. The invention of polyimide films, such as DuPont's Kapton, provided a flexible and heat-resistant substrate that could support intricate circuitry.
1970s to 1990s: Growth and Standardization
During the 1970s and 1980s, FPCBs gained popularity in various industries, including aerospace, automotive, and consumer electronics. The development of advanced manufacturing techniques, such as photolithography and etching, allowed for higher precision and reliability in flexible circuits. The establishment of industry standards, such as IPC-6013, ensured consistent quality and performance.
2000s to Present: Technological Advancements
The 21st century has seen rapid advancements in FPCB technology, driven by the increasing demand for smaller, lighter, and more powerful electronic devices. Innovations in materials, manufacturing processes, and design methodologies have significantly enhanced the capabilities of FPCBs.
Current Technological State of Flexible PCBs
Materials and Substrates
Polyimide Films
Polyimide films remain the most widely used substrate for FPCBs due to their excellent thermal stability, mechanical properties, and electrical insulation. These films can withstand temperatures up to 250°C and have a low coefficient of thermal expansion (CTE), typically around 20 ppm/°C.
Advanced Polymers
In addition to polyimide, advanced polymers such as liquid crystal polymers (LCPs) and polyethylene naphthalate (PEN) are gaining traction. These materials offer improved performance characteristics, such as lower moisture absorption and better dimensional stability.
Conductive Materials
Copper Foils
Copper foils are the primary conductive material used in FPCBs. The thickness of copper foils typically ranges from 12 µm to 70 µm, with thinner foils being used for high-density interconnects. The adhesion strength of copper foils to the substrate is critical, with values exceeding 1 N/mm² being common.
Silver Inks and Conductive Polymers
For specific applications, such as flexible displays and wearable electronics, silver inks and conductive polymers are used. These materials offer flexibility and can be printed using additive manufacturing techniques.
Manufacturing Processes
Photolithography and Etching
Photolithography and etching remain the cornerstone of FPCB manufacturing. These processes allow for precise patterning of circuits on flexible substrates. Advanced techniques, such as laser direct imaging (LDI), have further improved the resolution and accuracy of these patterns.
Roll-to-Roll Processing
Roll-to-roll processing is a high-throughput manufacturing method that involves continuously feeding a flexible substrate through various stages of fabrication. This process is particularly suited for large-scale production of FPCBs and offers cost advantages over traditional panel-based methods.
Additive Manufacturing
Additive manufacturing, including inkjet printing and screen printing, is emerging as a viable alternative for producing flexible circuits. These techniques enable the deposition of conductive and insulating materials directly onto flexible substrates, reducing waste and enabling rapid prototyping.
Performance and Reliability
Flexibility and Bend Radius
The flexibility of FPCBs is a key performance metric. Modern FPCBs can achieve bend radii as low as 1 mm without degrading their electrical or mechanical properties. This capability is crucial for applications in foldable devices and dynamic environments.
Thermal Management
Effective thermal management is essential for ensuring the reliability of FPCBs. Advanced materials with high thermal conductivity, such as metal-backed substrates, are used to dissipate heat efficiently. Thermal vias and heatsinks are also incorporated into FPCB designs to manage heat.
Environmental Resistance
FPCBs are designed to withstand harsh environmental conditions, including exposure to chemicals, moisture, and UV radiation. Protective coatings, such as conformal coatings and encapsulants, are applied to enhance their durability and reliability.
Data and Statistics
Market Growth
The global market for flexible PCBs has been growing steadily, driven by the demand for miniaturized and lightweight electronic devices. According to market research, the FPCB market was valued at approximately USD 15 billion in 2020 and is projected to reach USD 27 billion by 2025, with a compound annual growth rate (CAGR) of 12.6%.
Year |
Market Value (USD Billion) |
CAGR (%) |
2020 |
15 |
12.6 |
2021 |
16.8 |
12.6 |
2022 |
18.9 |
12.6 |
2023 |
21.2 |
12.6 |
2024 |
23.9 |
12.6 |
2025 |
27 |
12.6 |
Performance Metrics
Data from industry standards and research indicate the following typical performance metrics for FPCBs:
Parameter |
Typical Value |
Bend Radius |
1 mm |
Thermal Stability |
Up to 250°C |
Tensile Strength |
>150 MPa |
Adhesion Strength |
>1 N/mm² |
Electrical Conductivity |
Low resistance, high conductivity |
Challenges and Future Directions
Material Innovations
Continued innovation in materials science is crucial for the future of FPCBs. Developing new substrates with improved thermal and mechanical properties, as well as conductive materials with higher performance, will enable more advanced applications.
Manufacturing Techniques
Advances in manufacturing techniques, such as roll-to-roll processing and additive manufacturing, will enhance the efficiency and scalability of FPCB production. These methods will also enable the fabrication of more complex and intricate circuit designs.
Integration with Emerging Technologies
The integration of FPCBs with emerging technologies, such as flexible displays, wearable electronics, and the Internet of Things (IoT), presents significant opportunities. FPCBs' ability to conform to non-traditional shapes and withstand dynamic environments makes them ideal for these applications.
Environmental Sustainability
As the electronics industry moves towards more sustainable practices, the development of eco-friendly materials and manufacturing processes for FPCBs is becoming increasingly important. Research into biodegradable substrates and low-impact fabrication methods is ongoing.
References
1. [IPC-6013C: Qualification and Performance Specification for Flexible Printed Boards](https://www.ipc.org)
2. [Polyimide Materials for Flexible PCBs](https://www.dupont.com)
3. [Flexible Circuit Technology by Joe Fjelstad](https://www.flexiblecircuittechnology.com)
Industry Category