What Are Materials in Multilayer PCB Manufacturing?
By:PCBBUY 12/25/2024 14:49
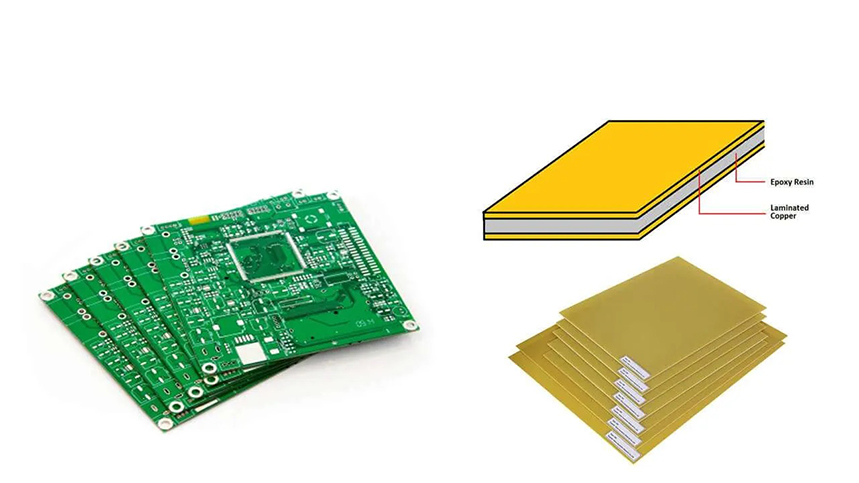
Multilayer Printed Circuit Boards (PCBs) are essential in modern electronic devices, providing the necessary infrastructure for complex circuitry. The materials used in the manufacturing of these multilayer PCBs, particularly thin copper-clad laminates and impregnation materials, play a crucial role in determining the performance, reliability, and durability of the final product. This article delves into the specifics of these materials, including their properties, tolerances, and the factors influencing their performance.
What is Thin Copper-Clad Laminates (TCCL)?
Composition and Structure
Thin copper-clad laminates (TCCL) consist of a dielectric substrate laminated with a thin layer of copper on one or both sides. The substrate is typically made from materials such as FR4 (a woven glass-reinforced epoxy resin), polyimide, or PTFE, chosen for their excellent electrical insulation properties and thermal stability.
Thickness and Tolerances
The thickness of the copper layer in TCCL can vary, commonly ranging from 0.5 oz/ft² (17.5 μm) to 2 oz/ft² (70 μm). The tolerance for copper thickness is critical, as it affects the PCB’s electrical performance and thermal characteristics. Table 1 below shows typical thickness values and tolerances for copper layers in TCCLs.
Copper Weight (oz/ft²) |
Thickness (μm) |
Tolerance (μm) |
0.5 |
17.5 |
±2.5 |
1.0 |
35.0 |
±4.0 |
2.0 |
70.0 |
±8.0 |
The dielectric substrate also has its thickness, which can vary significantly depending on the application. Common thicknesses range from 50 μm to 500 μm, with tolerances typically around ±10%.
Properties and Performance
The performance of TCCLs is influenced by several key properties:
Electrical Conductivity: The copper layer provides excellent electrical conductivity, essential for efficient signal transmission.
Thermal Conductivity: Both the copper and the dielectric substrate need to dissipate heat effectively to prevent overheating.
Mechanical Strength: The laminate must withstand mechanical stresses during manufacturing and operation.
Dimensional Stability: TCCLs must maintain their dimensions under varying thermal and mechanical conditions to ensure reliable performance.
Impregnation Materials in Multilayer PCBs
Role and Types
Impregnation materials, also known as prepregs, are used to bond layers together in multilayer PCBs. These materials are typically composed of woven fiberglass impregnated with a resin, such as epoxy. The prepreg provides mechanical strength and electrical insulation between layers while enabling the lamination process.
Thickness and Tolerances
Prepreg thickness is a critical parameter, as it affects the spacing between conductive layers and, consequently, the electrical properties of the PCB. Common prepreg thicknesses range from 100 μm to 300 μm, with tolerances around ±10%. Table 2 below shows typical thickness values and tolerances for prepregs used in multilayer PCBs.
Prepreg Type |
Thickness (μm) |
Tolerance (μm) |
Standard Epoxy |
100 |
±10 |
High-Tg Epoxy |
150 |
±15 |
Low-Dk Epoxy |
200 |
±20 |
Polyimide |
250 |
±25 |
Properties and Performance
The key properties of impregnation materials include:
Dielectric Constant (Dk): The dielectric constant affects signal propagation speed. Lower Dk values are preferred for high-frequency applications.
Dissipation Factor (Df): This measures the dielectric losses within the material. Lower Df values indicate less energy loss.
Glass Transition Temperature (Tg): Tg represents the temperature at which the material transitions from a rigid to a rubbery state. Higher Tg values indicate better thermal stability.
Thermal Expansion Coefficient (CTE): CTE measures how much the material expands when heated. Lower CTE values are desirable for minimizing thermal stress.
Stability and Reliability
The stability and reliability of TCCLs and impregnation materials are influenced by several factors:
Thermal Stability: Materials must withstand the high temperatures encountered during PCB manufacturing processes, such as soldering. High Tg and low CTE values are essential for maintaining structural integrity.
Moisture Absorption: High moisture absorption can degrade electrical properties and mechanical strength. Therefore, materials with low moisture absorption rates are preferred.
Chemical Resistance: Materials must resist chemicals used in the PCB manufacturing process, such as etchants and cleaners.
Aging and Degradation: Over time, materials may degrade due to thermal cycling, mechanical stress, and environmental factors. Materials with high durability and resistance to aging are critical for ensuring long-term reliability.
Impact of Material Selection on PCB Performance
Electrical Performance
The electrical performance of a multilayer PCB is heavily dependent on the properties of the TCCLs and impregnation materials. Key factors include:
Signal Integrity: Low Dk and Df values help maintain signal integrity, reducing losses and distortion.
Power Handling: High thermal conductivity and thermal stability allow for better heat dissipation, enabling the PCB to handle higher power levels without overheating.
Mechanical Performance
Mechanical performance is crucial for the durability and reliability of the PCB:
Flexural Strength: The PCB must withstand bending and flexing without cracking or delaminating.
Adhesion Strength: Strong adhesion between layers is necessary to prevent delamination under mechanical stress or thermal cycling.
Thermal Management
Effective thermal management is essential to prevent overheating and ensure reliable operation:
Thermal Conductivity: Materials with high thermal conductivity efficiently dissipate heat.
Thermal Expansion: Matching the CTE of different materials minimizes thermal stress and prevents cracking.
The selection of materials in the manufacturing of multilayer PCBs, particularly thin copper-clad laminates and impregnation materials, is critical for achieving the desired performance, reliability, and durability. Understanding the properties, tolerances, and factors influencing these materials allows for better design and manufacturing decisions, ensuring high-quality PCBs that meet the demands of modern electronic applications.
By carefully considering the electrical, mechanical, and thermal properties of these materials, manufacturers can optimize the performance and longevity of their multilayer PCBs, ultimately leading to more reliable and efficient electronic devices.
References
- IPC-4101: Specification for Base Materials for Rigid and Multilayer Printed Boards.
- IPC-6012: Qualification and Performance Specification for Rigid Printed Boards.
- "High-Performance PCB Laminates," by Dr. John Coonrod, Rogers Corporation.
- "Multilayer Printed Circuit Board Handbook," by Dr. J.P. Wilson, McGraw-Hill.
Industry Category