What Are Methods to Control ESD during Manufacturing?
By:PCBBUY 03/13/2024 15:27
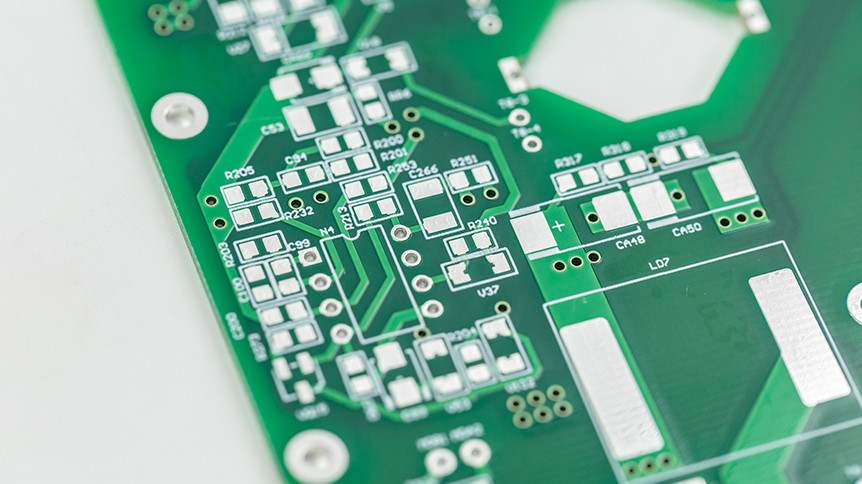
When a PCB assembly comes close to any object that has a charge, there is a possibility of an ESD. This depends on the electromotive force between the two and the distance separating them, with the greatest chance of an ESD taking place when the two touch.
In this passage, please check and read the content below to learn more about ESD PCB design. If you are searching for professional knowledge about ESD PCB design, please check this article for more.
What are the Main features of ESD?
Do you know the most dangerous feature of static electricity during SMT assembly, and what can lead to the biggest damage? It is that humans might not recognize ESD at all. The electrostatic discharge needs to be of a certain volume for humans to identify it. Unfortunately, even levels lower than the ones we can notice can endanger an electronic device's components.
ESD of low power is more than enough to cause huge damage to the product you are assembling. That low power cannot harm people, and it is so low that they don’t even notice the damage to the components. As for other features, it is vital to note that the ESD starts and ends quickly. It doesn’t take more than a millisecond for the electrostatic discharge to damage the components.
It is also important to note that humidity may contribute to ESD, which is why you should consider putting it under control.
How does ESD damage occur?
ESD can occur in a variety of forms. One of the most common is through human contact with sensitive devices. Human touch is only sensitive on ESD levels that exceed 4,000V.
A recent investigation found the human body and its clothing capable of storing between 500V and 2,500V electrostatic during the normal workday. This is far above the level that damages circuits yet below the human perception threshold. Other sources of ESD damage to equipment include:
· Troubleshooting electronic equipment or handling of printed circuit boards without using an electrostatic wrist strap;
· Placement of synthetic materials (i.e. plastic, Styrofoam, etc.) on or near electronic equipment; and
· Rapid movement of air near electronic equipment (including using compressed air to blow dirt off printed circuit boards, circulating fans blowing on electronic equipment, or using an electronic device close to an air handling system).
· In all of these scenarios, the accumulation of static charges may occur, but you may never know. Furthermore, a charged object does not necessarily have to contact the item for an ESD event to occur.
How to generate ESD damage?
Take a look at three ways that can generate ESD:
Friction – it is the contact that happens between two objects or surfaces. After you create contact and separate them again, you might notice electrostatic appearing. The simplest example of this is your clothes. You’ve surely felt static electricity when you touched your clothes at least once in your life. The problem with electrostatic in SMT assembly is that it can compromise the device's performance and its components.
Conduction – if the parts of your device have pins and lead made of metal, they have the potential to conduct ESD. That means if they find themselves between a component and an object (body, surface). It will transfer electrostatic.
Induction – some surfaces and objects have huge energy that might touch the electronic parts of your device. That will cause your parts to produce electrostatic themselves.
We presented three ways, but it all comes down to movement being what leads to static electricity and the potential damage.
What Are Methods to Control ESD during Manufacturing?
Semi Conductor: To protect the sensitive components from ESD contamination during manufacturing, there are four areas that PCB contract manufacturers will concentrate on:
Component identification: Although sensitive devices are pre-packaged from the manufacturer in static controlled containers, it is still important for the PCB CM to identify which components are more sensitive than others, and handle them appropriately. Not only is this important for ESD, but for moisture-sensitive parts as well.
Component handling: Once the components are in-house, the PCB CM needs to follow documented procedures for handling them. This includes their use within designated ESD protected areas of the manufacturing floor and ensuring that assembly technicians are trained and prepared for working with these parts.
Establish ESD protected areas: Areas for working with ESD sensitive parts need to be set up with the correct tools and equipment to minimize the generation of static electricity. These areas need to be controlled to ensure that only workers trained in ESD control methods and are prepared with the proper equipment have access.
Industry Category