What Are PCB Mouse Bite Dimensions and the Functions?
By:PCBBUY 05/11/2022 09:46
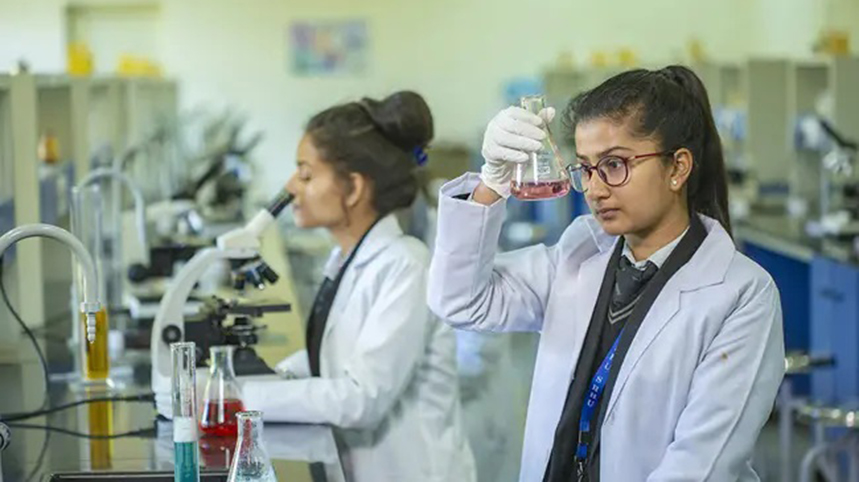
A mouse bite in a circuit board is part of the manufacturing panel used to fabricate and assemble the circuit board. Some people use the term “mouse bite” to describe over-etching in copper, but that isn’t what we are talking about here.
Circuit boards are typically laid out in a manufacturing panel by your PCB contract manufacturer using their Computer-Aided Manufacturing (CAM) systems. The panel gives both the fabricator and the assembler more board material for handling during the manufacturing processes, which is critical for smaller boards. Panels are usually a uniform size, and multiple instances of the PCB design can be laid out within the outline of the panel. Not only does a panel make it easier to manufacture a board, but multiple boards in the panel can be processed for almost the same cost as a single board.
If you are a PCB beginner and you are going to learn the information about PCB mouse bite, please check and read the content below in this passage.
What is the basic definition of PCB mouse bite?
Once the circuit boards have completed their fabrication and assembly processes, they need to be separated from their panels in a process called “depanelization.” Depanelization is accomplished by either cutting the boards out along pre-scored lines known as “V-grooves,” or breaking them out. Boards to be broken out must already be routed around their outlines to separate them from the panel and are only held in place by small tabs of material. These “breakout tabs” are removed, freeing the board from its manufacturing panel.
What are the main factors of PCB mouse bite?
A mouse bite in a circuit board is part of the manufacturing panel used to fabricate and assemble the circuit board. Some people use the term “mouse bite” to describe over-etching in copper, but that isn’t what we are talking about here.
Circuit boards are typically laid out in a manufacturing panel by your PCB contract manufacturer using their Computer-Aided Manufacturing (CAM) systems. The panel gives both the fabricator and the assembler more board material for handling during the manufacturing processes, which is critical for smaller boards. Panels are usually a uniform size, and multiple instances of the PCB design can be laid out within the outline of the panel. Not only does a panel make it easier to manufacture a board, but multiple boards in the panel can be processed for almost the same cost as a single board.
Once the circuit boards have completed their fabrication and assembly processes, they need to be separated from their panels in a process called “depanelization.” Depanelization is accomplished by either cutting the boards out along pre-scored lines known as “V-grooves,” or breaking them out. Boards to be broken out must already be routed around their outlines to separate them from the panel and are only held in place by small tabs of material. These “breakout tabs” are removed, freeing the board from its manufacturing panel.
The tabs have small holes drilled into them that make breaking out the PCBs easier and reduce the boards’ stress. With each tab broken along the line of the holes, the remaining material is left with a “mouse bite” appearance until it is smoothed out. Next, we’ll look at these mouse bite holes in more detail to find out what their recommended sizes and dimensions should be.
Constraints to consider during placement of breakaway Tab PCBs
There are some constraints to consider while performing the breakout tabs’ placement around the outline of the board.
· Don’t make use of many tabs in order to save wear, effort, and time on its router bits.
· Have enough tabs that can support the PCB board fully in its panel throughout the operations of PCB assembly.
· Tabs having a minimum clearance of 0.125 inches should be located to the closest components.
· Don’t place the tabs close to circuitry or sensitive components areas. This could cause the board to experience more breakout stresses.
At times, stress damages coming to the circuitry or components due to the tabs breaking may not be seen till later. It may also cause intermittent issues that won’t be debugged easily. This is why the location of breakout tabs, a distance away from any sensitive area, is very important to the circuit board’s success.
Also, if you don’t use enough tabs, and you don’t place them strategically to support your board during the manufacturing process, your board may end up flexing too much. This will prevent a reliable assembly. Now, this is the point where the experience and knowledge of your PCB manufacturer comes in.
V-Grooves vs Mouse Bites
PCB mouse bites can be used along with routing to reduce wasted material on a PCB panel through better tessellation of shapes for more complex geometry. Conversely, v-grooves are normally added in a linear fashion to a board but are difficult to add to non-rectangular patterns.
In many cases, you may use both along with routing to get the greatest number of boards from a PCB panel to reduce unit costs. Mouse bites can be more economical over v-grooves however v-grooves are used in particular for larger boards that do not require non-rectangular shapes to be routed.
The challenge with PCB mouse bites is that usually unless using bespoke manufacturing tools each hole used will need to be drilled, which can take longer per PCB mouse bite to complete. Routing can help reduce the number of perforations needed and ensure that the majority of the edges are smoother and easier to handle.
When designing a PCB mouse bite, you can either choose to offset the perforation away from the leading edge to create a mounting grip or recess it to reduce snagging on slot mounting PCBs.
The challenge with v-grooves is that they need to be added ideally in straight lines not only due to the tooling used and improved feed rate but also because the geometry needs to be repeated on the other side of the board. V-grooves are normally added at a 30-degree or 45-degree angle normal to the surface of the PCB.
When adding them you will need to ensure the remaining material is approximately half of the board’s thickness.
Industry Category