What Are the 3 Main Materials of Flexible PCB?
By:PCBBUY 10/31/2023 16:30
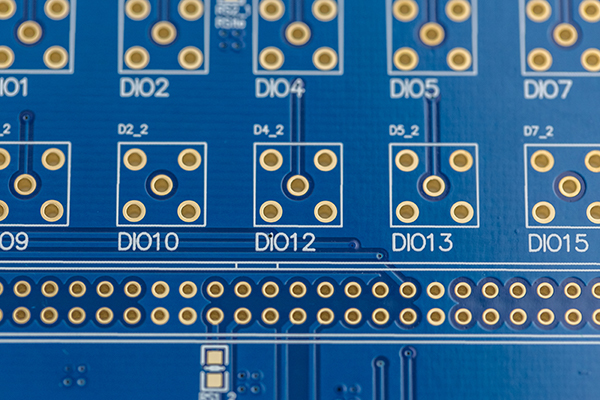
Flexible circuit is a technology developed by the United States for the development of space rocket technology in the 1970s. It is made of polyester film or polyimide as a substrate with high reliability and excellent flexibility. By embedding the circuit design on the thin and flexible plastic sheet, a large number of precision components are stacked in a narrow and limited space to form a flexible circuit.
In this passage, we are providing all the details of flexible PCB. If you are going to learn more about flexible PCB and the usage of it, please check and read the content below for more information.
If you want to order PCB product, please check and custom your order online.
What Are the 3 Main Materials of Flexible PCB?
1. Insulating film
The insulating film forms the basic layer of the circuit, and the adhesive bonds the copper foil to the insulating layer. In a multi-layer design, it is bonded to the inner layer.
They are also used as protective coverings to isolate the circuit from dust and moisture, and to reduce stress during flexure. The copper foil forms a conductive layer.
In some flexible circuits, rigid members formed of aluminum or stainless steel are used, which can provide dimensional stability, provide physical support for the placement of components and wires, and relieve stress. The adhesive bonds the rigid member and the flexible circuit together. Another material is sometimes used in flexible circuits. It is an adhesive layer, which is formed by coating adhesive on both sides of an insulating film.
There are many types of insulating film materials, but the most commonly used are polyimide and polyester materials. Nearly 80% of all flexible circuit manufacturers in the United States use polyimide film materials, and about 20% use polyester film materials. Polyimide material is non-flammable, has stable geometric dimensions, has high tear strength, and has the ability to withstand welding temperatures.
Polyesters have a melting point of 250°C and a glass transition temperature (Tg) of 80°C, which limits their use in applications that require a large amount of end welding. In low temperature applications, they exhibit rigidity. Nevertheless, they are suitable for use in products such as telephones and other products that do not require exposure to harsh environments.
2. Conductor
Copper foil is suitable for use in flexible circuits. It can be electrodeposited ( for short: ED) or plated. Electrodeposited copper foil has a shiny surface on one side and a dull matte surface on the other side. It is a flexible material that can be made into many thicknesses and widths. The matte side of ED copper foil is often treated with special treatment to improve its bonding ability. In addition to its flexibility, wrought copper foil also has the characteristics of hard smoothness. It is suitable for applications where dynamic deflection is required.
3. Adhesive
In addition to the adhesive used to bond the insulating film to the conductive material, it can also be used as a cover layer, as a protective coating, and cover coating. The main difference between the two is the application method they used. The cover layer is adhered to cover the insulating film to form a circuit with a laminated structure. Screen printing technology used for adhesive coating. Not all laminate structures contain adhesives, and laminates without adhesives form thinner circuits and greater flexibility. Compared with the laminated structure based on adhesive, it has better thermal conductivity. Due to the thin structure of the adhesive-free flexible circuit and the elimination of the thermal resistance of the adhesive, which improves the thermal conductivity, it can be used in working environments where flexible circuits based on the adhesive laminate structure cannot be used.
What are the advantages of flexible PCB?
The advantages of multi-layer circuit boards: high assembly density, small size, light weight, because high-density assembly, reduced wiring between components (including parts), thereby increasing reliability; can increase the wiring layer, and then increase design flexibility; It can also form the impedance of the circuit, can form a certain high-speed transmission circuit, can set the circuit, the electromagnetic shielding layer, and can also install the metal core layer to meet the functions and needs of special thermal insulation; easy installation and high reliability.
Disadvantages of multi-layer PCB board (unqualified): high cost and long cycle; high reliability inspection method is required. Multilayer printed circuit is the product of electronic technology, multi-function, high speed, small volume and large capacity. With the development of electronic technology, especially the wide application of large-scale and ultra-large-scale integrated circuits, fine lines appear in the direction of high-density, high-precision and high-number change of multilayer printed circuits.
What are the applications of flexible PCB?
The PCB industries and applications in which flex PCBs can be used are diverse. Hence, we are focusing on a few major industries and applications.
Electronics:
Laptops
Cameras
Calculators
Printer Heads
Flip Cell Phones
Computer Keyboards
Manufacturing:
Robotic Arms
Sensoric Equipment
Processing Machines
Bar Code Equipment
Human Machine Interface (HMI) equipment
Automotive:
Air Bag Systems
Antilock Brakes
GPS Systems
Engine Controls
Medical:
Pacemakers
Hearing Aids
Heart Monitors
Exercise Monitors
Others:
Resistors
Satellites
Capacitors
Tower Lights
LCD Fabrication
Light and Motion systems
Wanna know PCB knowledge? Check and read for more.
Industry Category