What Are the 3 Tips of PCB Design Guidelines for Power Electronics?
By:PCBBUY 03/10/2022 09:41
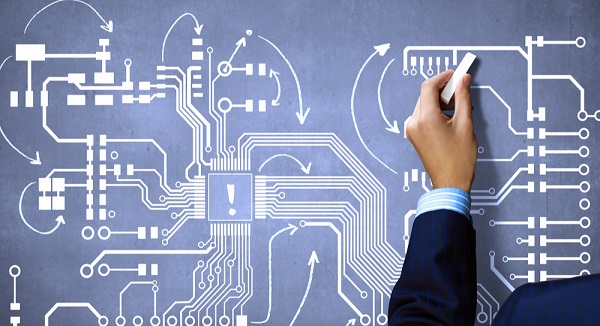
Every circuit board will have some common power integrity problems that need to be identified by examining the PDN. The PDN impedance, S-parameters, Z-parameters, DC current density, and voltages are all important points to examine and calculate as part of power integrity analysis of an electronic system. In some systems, power integrity problems are minor and may not be noticed in measurements.
If you are curious about more information about PCB design guidelines for power electronics, please check and read the content below in this passage for more professional knowledge.
What are the preparations of PCB design guidelines for power electronics?
There are different power electronics that you can design for your circuit board depending on the need. In the case of converting AC power to DC, you will most likely use a regulated power supply that is either a linear or a switch-mode power supply. For applications that consume low power, these supplies can be designed into the PCB as an integrated circuit component (IC) making them ideal for smaller devices that plug straight into a wall socket.
To convert DC to DC power, such as stepping a voltage up or down, there are different power conversion circuits that you can design onto your circuit board. For example, a boost conversion circuit will step up the output voltage while a buck converter will step it down. There are also other variations of DC to DC conversion circuits, such as the buck-boost converter where the voltage can be stepped up or down depending on how it is controlled.
No matter what kind of power supply that you are designing into your schematic, you will be using a mixture of both active and passive components. You will need to use parts that are designed for higher voltages which have dielectric material and coatings that are specified to withstand higher resistance and temperatures. You must also make sure that your design doesn’t exceed the manufacturer’s specified operating values for the parts that you are using to ensure that the part will not fail prematurely. To make sure that the power supply design you create in your schematic will work correctly on the final PCB, you should simulate the design before going to PCB layout.
Thermal Management of Power Electronics
Power supply electronics can run hot depending on the amount of power that they are converting, and that heat must be managed on your circuit board. For those supplies that are very high powered, you may want to look into alternate board materials such as ceramics or some of the PTFE (Polytetrafluoroethylene or “Teflon”) laminates. Be warned though that some of these materials have non-standard fabrication processes that will drive up your manufacturing costs.
Another method of managing the heat in your design is in how the PCB layer stackup is configured with power and ground planes. Although ground planes are important for the management of power integrity, they also help to manage the heat from the surface layers. The heat from component thermal pads and metal conductors will get conducted down through the vias and into the planes where it can dissipate. It is important in your layout to use traces with a higher copper weight to carry high current, which will help with heat dissipation as well.
Choosing the right regulator for PCB power supply
Generally, designers have two options in choosing power supply regulators, linear regulators and switched-mode regulators. The linear regulators provide low noise output but it has higher heat dissipation which requires cooling systems. The switched-mode regulators are highly efficient over a broad current range but the switching noise causes spikes in response.
A linear-mode requires an input voltage higher than the required output voltage because there will be a minimum dropout in voltage. Linear regulators will have considerable power loss and heat dissipation which makes linear regulators less efficient. If you are considering a linear regulator for your PCB design then you must consider a regulator with low voltage dropout and the thermal analysis must be done before going to fabrication. Besides that, linear-mode regulators are simple, cheap, and provide exceptionally noiseless voltage outputs.
The switching regulators convert one voltage to another by temporarily storing energy in inductors and then releasing that energy at a different voltage at different switching times. In such power supplies, fast switching MOSFETs are used. The output from these highly efficient regulators could be adjusted by altering the duty cycle of the Pulse Width Modulation (PWM). The efficiency depends on the heat dissipation of the circuit, which is low in this case.
The PWM switching of switching regulators causes noise or ripple in the output. Switching currents can cause noise crosstalk in other signals. Thus switching power supplies need to be isolated from critical signals.
Switched-mode regulators use MOSFET technology, thus it is obvious that these regulators emit EMI (Electromagnetic Interference) noise. We cannot eliminate EMI from any circuit completely but we can minimize it by EMI reducing measures like filtering, reducing current loops, ground planes, and shielding. Electromagnetic Compatibility (EMC) measures should be considered before incorporating switched-mode regulators in your design.
When it comes to choosing a voltage regulator, linear and switching regulated power supply are the two obvious choices. Linear controlled power supply is cheaper, but inefficient and dissipates more heat. Meanwhile, the switching regulated power supply is more expensive and requires the connection of more passive components bt it doesn’t easily heat up.
Industry Category