What Are the 5 Considerations of ICT in PCB Industry?
By:PCBBUY 08/16/2022 16:35
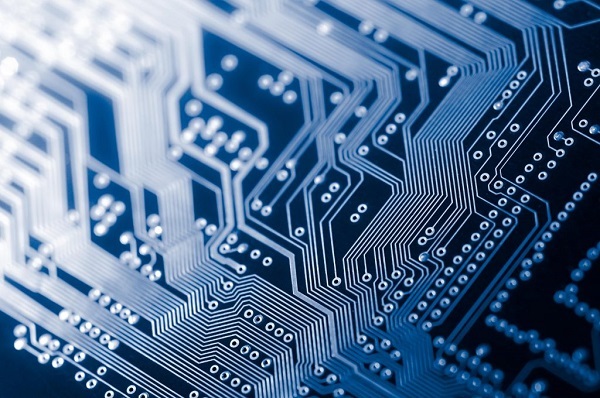
Cost is also inclusive of the maintenance you'll need to make on the PCB once in a while. An instance, even if your products design changes, you may only need a program change. In ICTs, however, you will need a new fixture and components. If you are going to learn more about ICT in PCB manufacturing, please check and read this passage.
What are the advantages of ICT?
ICT has some significant advantages that have been the reason manufacturers opt for it for centuries.
They include:
· In contrast to the AOI and flying probe testers, it can test the ball grid array assemblies (BGAs).
· Straightforward interpretation: the ICT system quickly locates the faultiness and presents it to you in a matter of minutes. You may not need professionally skilled personnel to proceed with the interpretation.
· Fast/ Time-effective: it roughly takes 1 minute in comparison to a flying probe tester that may take about 25 minutes. Being short is in regards to contacting all the board’s test points at once.
· Easy program generation: an ICT tester is effortlessly programmed. In that, you can take files from the PCB outline to make the essential program.
· It can test functionality as well as assembly defects as ICT systems can handle complex testing methods.
· Cost-effective: The high speed helps in quick recovering of the expense of setting up the fixture and program. It is especially true when considering boards that you assemble in large volumes.
· ICT platforms: The testing platform for ICT is available in both Windows and UNIX OS, making it universal.
· The testing can carry out several tests without applying power to the Device Under Test (DUT). It ensures a safe test and protects the board from any damage.
What are the basic concepts of ICT in-circuit test?
In circuit test equipment provides a useful and efficient form of printed circuit board test by measuring each component in turn to check that it is in place and of the correct value. As most faults on a board arise out of the manufacturing process and usually consist of short circuits, open circuits or wrong components, this form of testing catches most of the problems on a board. These can easily be checked using simple measurements or resistance, capacitance, and sometimes inductance between two points on the circuit board.
Even when ICs fail, one of the major reasons is static damage, and this normally manifests itself in the areas of the IC close to the connections to the outside world, and these failures can be detected relatively easily using in-circuit test techniques. Some in-circuit tester are able to test some of the functionality of some integrated circuits, and in this way give a high degree of confidence in the build and probability of operation of the board. Naturally an in-circuit test does not give a test of the functionality of a board, but if it has been designed correctly, and then assembled correctly, it should work.
In-circuit test equipment consists of a number of elements:
In circuit tester: The in circuit test system consists of a matrix of drivers and sensors that are used to set up and perform the measurements. There may be 1000 or more of these driver sensor points. These are normally taken to a large connector conveniently located on the system
Fixture: The in-circuit test system connector interfaces with the second part of the tester - the fixture. In view of the variety of boards this will be designed specifically for a particular board, and acts as an interface between the board and the in circuit tester. It takes the connections for the driver sensor points and routes them directly to the relevant points on the board using a "bed of nails".
Software: Software is written for each board type that can be tested. It instructs the test system what tests to perform, between what points and details of the pass / fail criteria.
These three elements for the major parts of any in-circuit test system. The tester will be used for a variety of boards, while the fixture and software will be board or assembly specific.
In circuit test system are normally relatively expensive items of equipment. They are typically sued on high volume production lines. The fixture and programme generation costs mean that they are not viable for small runs of less than 250 to 1000 items. A cost analysis should be undertaken to ensure that the cost of generating the fixture and programme is viable.
Industry Category