What Are the 5 Effective Tips of Automotive PCB Assembly Services?
By:PCBBUY 03/31/2022 10:27
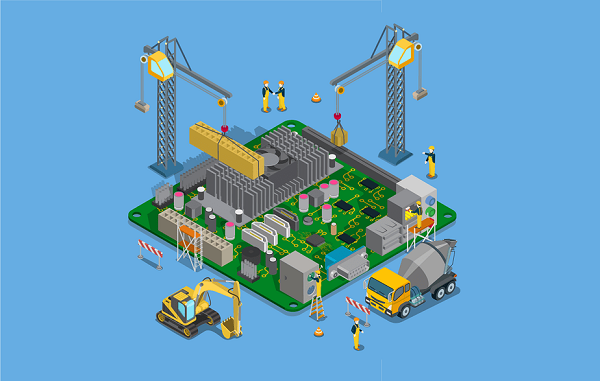
The popularity of printed circuit boards for vehicles can be attributed not only to its functionality, but also because of its many other benefits. This is a welcomed innovation in vehicle manufacturing as it has extensive applications. Other alternatives will not be able to take over its functions, or will at least not suffice in terms of their quality.
It’s important that your PCB manufacturer is capable of producing very small circuit boards as most vehicle types that use printed circuit boards only allow a limited amount of space for electronic control devices. Please check and read the content below for more information of automotive PCB manufacturing.
What are the characteristics during automotive PCB design?
High-frequency substrate board
Automotive collision-resistance/predictive braking safety system plays a role as a military radar device. Since automotive PCBs are responsible for transmitting microwave high-frequency signals, substrate with low dielectric loss needs to be applied with the ordinary substrate material to be PTFE. Different from FR4 material, PTFE or similar high-frequency substrate materials require special drilling speed and feeding speed during drilling.
Thick copper PCB
Automotive electronics brings more heat energy owing to high density and power and hybrid power and electromotives tend to require more advancing electric power transmission system and more electronic functions, which leads to more requirements on heat dissipation and large current.
It's relatively easy to fabricate thick copper double-layer PCBs while it's much more difficult to fabricate thick copper multi-layer PCBs. The key point lies in thick copper image etching and thickness vacant filling.
Component embedment
Component embedded PCBs were massively applied in mobile phones in order to increase assembly density and decrease component size, which is acquired by other electronic equipment as well. Therefore, component embedded PCBs are also applied in automotive electronic equipment.
According to different component embedment methods, there are numerous manufacturing methods for component embedded PCBs. Component embedded PCBs for automotive electronics have mainly 4 manufacturing methods
Types of automotive PCBs
In order to meet the stringent requirements of space, weight and cost, automotive industry uses different types of PCBs that differ from each other both in the structure and in the type of material or substrate used. The main types of PCBs for automotive applications are as follows:
Rigid PCBs: these are the traditional PCBs, not flexible and normally manufactured using FR4. Applications includes display monitors and reverse cam screens;
Flex PCBs: these printed circuit boards are built with flexible plastic substrates and use of materials such as polyamide, polyetheretherketone (peek) or transparent polyester films. The advantage of these boards is that they can be twisted and bent. Applications are numerous, especially where space is limited or irregular in shape, and include the connection of displays, control panels and light switches;
Rigid-flex PCBs: they are a combination of the two types of PCBs mentioned above and therefore offer the advantages of both. Rigid-flex PCBs are used, for instance, in lighting systems;
LED PCBs: the increasingly massive use of high power and high brightness LEDs requires PCBs with excellent heat dissipation, typically made with a metal substrate such as aluminum. PCBs of this type are used in car indicators, headlights, and brake lights;
HDI PCBs: HDI, acronym for High Density Interconnect, indicates printed circuit boards with high density of electrical connections per unit of area. These PCBs have finer spaces and lines, minor vias and capture pads and higher connection pad density. Widely used in infotainment systems, HDI PCBs help improve the quality of wiring, reducing the weight and size of the solution.
What are the applications of PCB for automotive industry?
Because there are so many different types of electronic systems in today's cars, the types of PCBs needed for automotive electronics vary greatly. The same car may require flex PCBs, rigid PCBs and rigid-flex PCBs for different technologies. As people demand more accessories and features for their cars that are powered by electronic components, the need for automotive PCBs of varying types is only growing.
Car PCB manufacturers need to provide a wide variety of PCB options. The kinds of systems and operations that now use printed circuit boards for enhanced efficiency and safety include rear LED lights and running lights, transmission controls and comfort control units. You can also find car PCBs managing engines, entertainment systems, digital displays, radar, GPS, power relays timing systems, mirror controls and a lot more.
Industry Category