What Are the 5 Essential Aspects of PCB Panelization Guidelines?
By:PCBBUY 03/15/2022 10:02
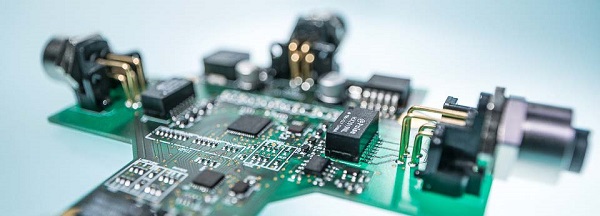
It is also essential to choose the size of the panel, whether small or large, that best fits your printed circuit board's needs and the various manufacturing and assembly processes. The more boards you can fit into a PCB panel, the more efficient the manufacturing process will become. It will also reduce the number of panel space that will go to waste.
If you are curious about more information of PCB panelization, we recommend you to check and read the content below for more information about PCB panelization.
What are the tips of PCB Panelization?
Here are some guidelines for determining how Bay Area Circuits panelizes parts:
· Multilayer (3 or more layers) PCBs are only printed on 12”x 18” panels or larger.
· To be conservative, plan for a border (or spacing) of 1 inch around the border of the panel. However, depending on the design the spacing or panel margin for 2 layer boards can be as little as 0.50 inches and 0.75 inches for multilayer boards. The spacing between boards should be 0.1 inches or 0.2 inches for round boards.
· It is highly recommended that the total yield is greater than your desired quantity. This is to account for any possible board failures that may occur during manufacturing.
PCB panelization improves work efficiency
As a way of improving the productivity of the PCB manufacturing process, it is common practice to mount several copies of smaller printed circuit boards in a manufacturing panel. It is an effective method of fabricating and assembling the boards instead of building them one by one. The panel must contain the same materials and layer stack-up configuration as the printed board.
It is also essential to choose the size of the panel, whether small or large, that best fits your printed circuit board's needs and the various manufacturing and assembly processes. The more boards you can fit into a PCB panel, the more efficient the manufacturing process will become. It will also reduce the number of panel space that will go to waste.
During panelization, PCB panel designers must use all the arrangement options when placing the PCB designs to optimize the panel space and improve manufacturing efficiency.
How to process PCB Panelization?
The most critical area of panel requirements for PCB layout is to observe the clearances. Sensitive areas of circuitry and components need to be held back from the board edge to protect them during depanelization. Additionally, breakout tabs and V-grooves both have unique clearances that have to be held. As a reminder, these are just PCB panelization guidelines; you should confirm actual clearances with your PCB CM, as they tend to vary between manufacturers.
Breakout Tabs:
· To prevent any possibility of damage from splinters when the boards are broken out, components should be kept back a minimum of 0.125 inches from a tab. Taller components, like electrolytic capacitors, should be kept back 0.250 inches from a tab.
· While copper traces and planes can be very close to the edge of a board (0.005 inches), they should be kept back 0.125 inches from where a tab will be located.
· Make sure that there is enough room for the number of tabs necessary to support the board during its manufacturing operations.
· Pay attention to sensitive areas of circuitry on the board that could be more susceptible to the stress put on the board with a breakout tab.
V-Grooves:
· Keep components back 0.050 from the edge of the board if it is to be cut with a V-groove.
· Taller components should be kept back 0.125 inches from the board edge to avoid interference from the cutting tools.
· Components with large solder pads should also be given more clearance to avoid any chance of their solder joints experiencing stress fractures during depanelization.
· Copper traces and planes should be kept back 0.020 inches from the board edge.
· Each manufacturer will probably have panel requirements that differ slightly from each other, and these clearance values should be checked with your own PCB CM. Here are some other panel details to consider during PCB layout:
· Make sure to understand what depanelization method (breakout tabs or V-grooves) will be used before you set up your board edge clearances.
· Find out which way wave soldered boards will be arranged in the panel to place SMT discretes accordingly for the wave.
· Make sure to specify overhanging component outlines in your drawings so that the manufacturer will create the panel accordingly.
Industry Category