What Are the 5 Main Factors of Aerospace PCB Design Standards?
By:PCBBUY 02/19/2022 09:50
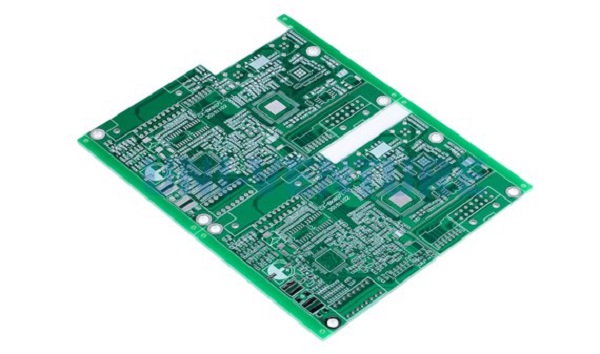
It’s no surprise that aerospace manufacturing and design must meet stringent standards. Electronics in aerospace often face harsh environments, and it may be impossible to repair them while they’re in use -- they’re thousands or millions of feet in the air, after all which means your aerospace PCB assembly better work as you intended.
Do you know the details about aerospace PCB design? If you are searching for professional knowledge about aerospace PCB, please check and read the content below for more information.
What are the rules of aerospace PCB design?
Printed circuit boards designed for aerospace and military applications shall have a high degree of reliability and robustness, without offering any margin for error. Challenging applications, such as space missions, require an accurate understanding of how printed circuits must be designed and created to ensure a very long period of operation, in often very extreme operating conditions. Unlike most traditional PCBs, printed circuit boards used in aerospace applications are subjected to extreme environmental conditions, radiation, chemicals, contaminants, and more.
It follows that these circuits must meet very strict standards, such as the IPC-A-610E Class 3, which refers to high-performance electronic devices whose operation must be guaranteed continuously, without any interruption, even in the most difficult and critical operating conditions. Some of the main applications falling within the scope of the IPC-A-610E Class 3 standard are the following:
· Systems for satellite communication
· Navigation systems, control systems and on-board avionic instrumentation
· Applications for on-ground processing of data recorded during flights or missions (ground stations)
· Passive detection systems
· UAVs (Unmanned Aerial Vehicles)
Circuits for aerospace applications are exposed to extreme temperatures and must be able to withstand and absorb shocks and vibrations of considerable intensity. In addition, they have many features in common with PCBs for RF high frequency applications, bearing in mind that radio communication in the HF (or higher) band is a fundamental requirement for these systems. Operating at high altitudes, the risk associated with radiation also increases and, as a result, PCBs (as well as the electronic components used) must be designed to withstand high levels of radiation for a long time without being damaged.
What are the basic considerations of aerospace PCB design?
With any military or aerospace electronics project, there are special boxes your design has to check off:
· Can it last long before requiring maintenance?
· Have you followed material specs down to the letter?
· Can it hold up in a harsh environment?
· What testing and inspection will be necessary?
· Is it 100% compliant with AS9100 design standards?
Have you fully assessed risk?
Aerospace PCB design standards soar far above what you’d see in, say, a toddler’s LeapFrog tablet.
Aerospace electronic components can be critical or noncritical. For example, there are PCB (printed circuit boards) in the autopilot system on an airplane -- obviously important to keeping people alive. If they fail, you have a big problem, Houston.
In contrast, there are also circuit boards in the seat adjustment controls of a commercial airline. These are not considered critical; if they fail, lives aren’t at risk. Still, you’ve got to design electronics in a way that they can “fail safely” and not be a fire risk.
When considering how you are going to design military & aerospace electronics, plan ahead to follow the appropriate protocols. The components and materials you use should reflect the requirements you must meet for your product’s final use. If your product is mission-critical, expect longer lead times. The approval process is going to be much longer.
Industry Category