What Are the 5 Main Solutions of Intelligent PCB?
By:PCBBUY 10/25/2023 15:58
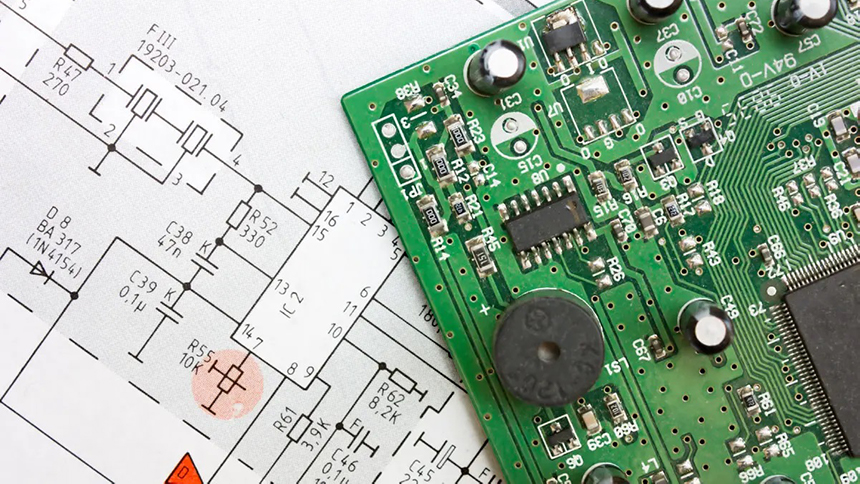
1. Digital models should be established in smart factories in terms of general design, procedure and layout and simulation should be carried out. Besides, digital management should be implemented during the whole procedure from planning, manufacturing to operation.
2. Digital 3D design and technology should be applied to carry out product/technology design and simulation. Verification and optimization should be done through physical detection and test. Product Data Management (PDM) should be set up so that product design and technological data will be integrated.
3. Numerical control rate of manufacturing equipment should exceed 70% and information mutual communication and integration should be achieved between key technologies and equipment including top-grade numerically-controlled machine tools and industrial robots, intelligent sensors and control equipment, intelligent detection and assembly equipment, intelligent logistics and storage equipment.
4. Production process data collection and analysis system should be founded to make production process data automatically uploaded including production schedule, field operation, quality detection, equipment status and material transfer with visual management achieved.
5. Manufacturing Execution System (MES) should be established in the factory in order to reach all management functions including planning, dispatch, quality, equipment, manufacturing and energy efficiency. Enterprise Resource Planning (ERP) system should be also established so that enterprise management functions can be achieved including supply chain, logistics and cost.
What are the options of Intelligent PCB design?
The first step in power supply is to choose the type of power supply you wish to use for your device. Unregulated power supplies are a down-and-dirty option for converting AC power from a wall outlet to a DC voltage. The output from these supplies will contain a ripple waveform as the output is not smoothed with a regulator. Modern applications use a regulated power supply, where this ripple is minimized.
There are two principal options for regulating DC output from power supplies: using a linear regulator or a switching regulator, which is sometimes called a switch-mode power supply. These types of power supplies pass the DC output from a full wave rectifier to a regulation circuit, which smooths the ripple waveform that is superimposed on the desired DC output. These regulators can also be used to directly regulate a DC power source like a battery. Linear regulators have very low noise, but they tend to be bulky due to the use of heatsinks or other active cooling measures required for thermal management. The significant heat dissipation in these power supplies is responsible for their low efficiency.
In contrast, a switched mode power supply provides much higher efficiency over a broad current range, allowing these power supplies to take on smaller form factor. However, these power supplies use a PWM circuit to smooth and regulate the output voltage, which requires the use of an active switching component (normally a MOSFET). This means that the system radiates strong EMI, and the output will contain spikes due to switching noise. This switching noise can appear as a ringing signal on the output (i.e., conducted EMI), and this noise needs to be filtered from the output.
How to process the Intelligent PCB design?
This section describes the design of the IAPIS and the system architecture is shown in Figure 2. In the proposed system, there are three modules to achieve the objectives of identifying the key factors in PCBA and optimizing the machines’ parameter settings. The three modules are: (i) a data collection module (DCM); (ii) a failure analysis module (FAM); and (iii) a machine setting optimization module (MSOM). In the proposed system, DCM functions to collect the essential data from the PCBA process and expert perception to facilitate the data analytics process.
In order to improve the PCBA process performance, FAM plays a role to determine the critical process parameters through the investigation of the NG types, while MSOM is developed to optimize the process parameters obtained in the FAM. By setting the optimized process parameters, the process performance in term of yield loss can be enhanced, resulting in better quality of the PCBA process.
Considering the above studies, the rapid development of approaches to improve the productivity and process performance has continued in recent years. In the era of smart manufacturing, the above concerns can be effectively addressed by means of emerging technologies and techniques. The selection of k-means clustering to investigate the critical parameters in the PCBA process is appropriate and the selected parameters can be used to formulate effective experimental studies. Consequently, the structured system architecture can be established, as described in the next sections.
Industry Category