What Are the 5 Types of Common PCB Component Failure?
By:PCBBUY 01/29/2023 14:55
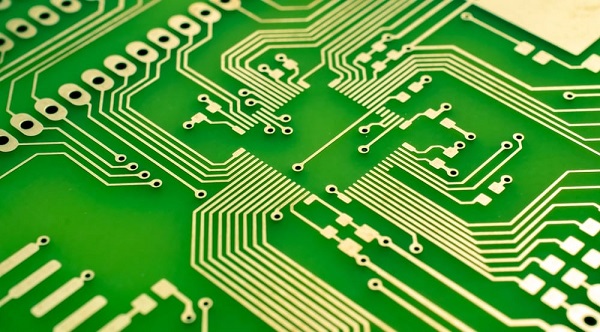
Electronic component failure is when a component is not functioning or performing as expected. It eventually damages the product. These defects may result in a complete breakdown or degradation in the performance of the device.
It is crucial to perform root-cause analysis to find out the failure modes of components. This research requires some information that includes:
· Circuit board design data including dimensions, stresses, loads, etc.
· Parts, material, and process specifications.
· Manufacturing process reports involving chemical analyses, mechanical properties, inspections, and performance testing.
· Information related to working environments.
· Maintenance record comprising vibration analysis and previous failures.
In this passage, we are going to tell you about PCB Component Failure, please check and read the content below of PCB Component Failure.
How to Prepare factors for the PCB component placement?
The primary objective of PCB development is to design a PCB that functions and performs as intended. However, it is equally, if not more, important for a design to be manufacturable. Of course, various determining factors may affect PCB manufacturability, including:
Components: If a component is distinctive or challenging to acquire, it will increase the cost of manufacturing. Moreover, if the lead times on some components incur delays in production, it will increase costs.
Placement: Component placement affects how you manufacture a PCB and whether you can even manufacture a PCB. Improper component placement can dramatically increase board costs. In fact, design decisions as simple as the orientation of a component can affect its solderability.
Layout: The schematic layout places component placement and other considerations at the center of your design process. However, failure to account for possible connections or interfaces with other PCBs will increase overall system manufacturing costs.
What are the common PCB Component Failures?
Electronic component failure is when a component is not functioning or performing as expected. It eventually damages the product. These defects may result in a complete breakdown or degradation in the performance of the device.
Unprotected Components
Circuit boards are subjected to various conditions before being installed for operation. These include board fabrication, PCB assembly, shipping and storage. During all of these phases, the possibility of contamination exists. For the manufacturing of critical boards—such as those used in some medical device applications—ionic contamination can be a major problem. During shipping and storage, unprotected boards are subject to oxidation and other contamination that may eventually lead to a premature board and/or component failure.
Moisture Sensitive Components
One of the major sources of contamination that threaten electronic components on circuit boards is moisture. Moisture can be acquired during component and/or board manufacturing. Additionally, condensation can occur on the board and within component packages. This is most common when boards are stored in packaging where internal temperatures are colder than the external environment. Certain components are more susceptible to moisture than others and this should be a consideration when making your selections.
Temperature Sensitive Components
PCBAs are installed everywhere these days. This includes extreme environments where temperature, pressure and corrosion can affect the operation, damaging boards and components. For example, components used for aerospace electronics must be able to withstand temperatures that range from very cold (as low as minus 184° F in the thermosphere) to severely hot (approximately 5,792° F during a rocket launch). When selecting these components, especially when a COTS solution is implemented, thermal sensitivity must be a major concern.
Components Vulnerable to Power Surges
Excessive heat on circuit boards can cause several failure mode issues. These include structural fatigue and spikes in the current flow. The latter can also be due to power supply surges or, in the case of high voltage PCBAs used in industrial applications, arcing. Irrespective of the source, large currents can wreak havoc on boards and destroy vulnerable unprotected components.
What are the inspection techniques to avoid PCB Component Failures?
A contract manufacturer will be dealing with parts that have either been ordered out of a catalog of parts, or a part that has been specifically built by a manufacturer for customers that request them. For any of these new parts, there should be a full, first-article inspection process in place that will do the following:
· Take sample measurements of the part.
· Have the part reviewed and approved by a quality engineer to match up with the posted specifications.
· Maintain a file for this and all other first-article parts for future reference.
· In some rare cases for specialty parts, conduct an electrical test of the part with the help of the CM’s test department for a test fixture and procedure.
· The more unique the part is—and for those that are custom-ordered for a specificapplication—the more thorough the inspection process should be. The inspection results should also be fed back to the manufacturer for their records.
Once a relationship has been built with a supplier of standard components, the parts may no longer need to be subjected to the same level of inspection. This should follow a documented criteria for inspection that will specify what needs to happen before a component and its supplier becomes a trusted part and vendor.
For instance, if a standard catalog part is received five times from the same originator or supplier and there isn’t a rejection, the moisture barrier packaging may no longer need to be opened for incoming inspections. This trusted relationship is vital with incoming components so that the components can stay in their protected packaging until they are needed for a PCBA build.
Industry Category