What Are the Advantages of PCB Conformal Coating?
By:PCBBUY 02/27/2024 16:11
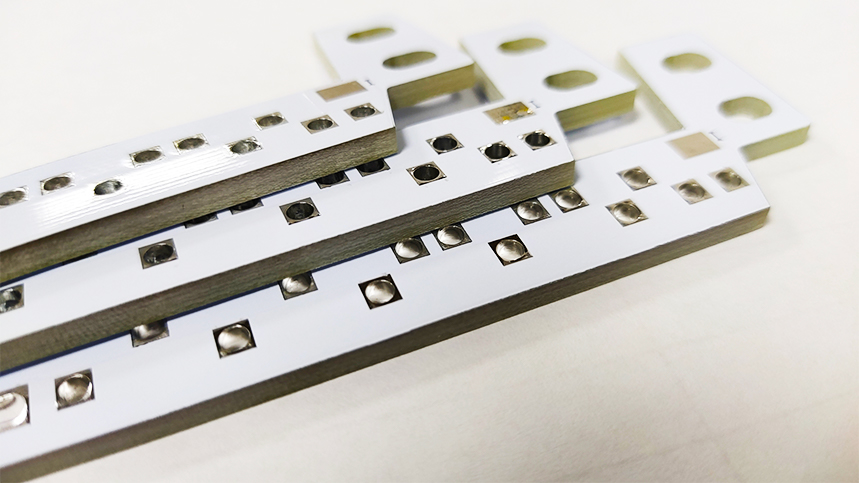
What is conformal coating and what is it used for? In short, conformal coating is a thin, transparent film that can be applied to the surface of a circuit board. This film contours to the PCB’s shape, protecting components from environmental conditions without impacting functionality.
Conformal coatings will even increase the dielectric strength of a board allowing for reduced spacing between circuits in more compact and dense PCB layouts. In this passage, we are going to provide you everything about PCB conformal coating, please check and read the content below for more information.
What are the types of conformal coating?
Many types of PCB conformal coating materials exist, including a range of specialty varieties. The most common of these conformal coatings are described below, along with their most prevalent applications:
Urethane resin: Urethane resins (UR) or polyurethane resins are known for their excellent resistance to moisture, abrasion and chemical attacks. The downside of this material is that it is resistant to solvents, meaning it is difficult to remove and rework. Urethane resins are most commonly used in aerospace applications where components may be exposed to corrosive fuel vapors.
Acrylic resin: Acrylic resins (AR) are acrylic polymers dissolved in a solvent. These substances require a simple drying process and are easy to rework. When complete, this type of coating provides good general protection against humidity and other environmental factors but poor protection from solvents and chemical vapors, making it most suitable for basic-level protection. The major upside of this material is the ease with which it can be removed and reworked, making it practical for repair operations.
Epoxy resin: Epoxy resin (ER) coatings are compounds that create a hard layer with good humidity, abrasion and chemical resistance, with minimal permeability. Less flexible than other types of coatings, epoxy resins are difficult to remove and rework. Epoxy is the most common choice for PCBs that need to be coated completely and is often chosen for applications with low mechanical stress.
Silicone resin: Silicone resin (SR) coatings provide excellent thermal, chemical, moisture and corrosion resistance while maintaining good flexibility. This type of coating is difficult to remove and offers poor abrasion resistance due to the surface’s rubbery texture. However, it makes up for this in offering good resilience against vibrational stress. Silicone resin conformal coatings are often chosen for electronics in outdoor environments that are exposed to broad temperature and moisture conditions.
Parylene: Parylene (XY) coatings are applied through chemical vapor deposition. In this process, the parylene is heated to become a gas and put into a vacuum chamber to polymerize and turn into a thin film, which is placed over electronics. This film offers excellent dielectric strength and resistance to extreme temperatures, moisture and corrosive elements. However, it is also difficult to remove and rework, requiring abrasion techniques to remove. The specialized production process also makes replacing parylene coating more difficult than other methods. It’s often used in specialty applications.
What Are the Advantages of PCB Conformal Coating?
· Insulating properties allow a reduction in PCB conductor spacing of over 80%
· Can help eliminate the need for complex, sophisticated enclosures
· Light weight
· Completely protect the assembly against chemical and corrosive attack
· Eliminate potential performance degradation due to environmental hazards
· Minimize environmental stress on a PCB assembly
Printed Circuit Board (PCB) rework may be necessary for high-value boards. Conformal coatings should be removable with minimal to moderate effort and easily repairable off-line. Ease of rework and removal are directly linked to the resilience of a coating to specific factors in the operating environment. In general, solvent-based, non-cross-linked coatings will be relatively easy to remove with solvents. UV light-curable and cross-linked materials, with their enhanced environmental and chemical resistance, will be more challenging to remove.
It’s important to consider the effect of the rework/removal method on solder masks, components, and assembly materials prior to choosing the appropriate method. The three most common techniques for removal are chemical, thermal, and mechanical.
Chemical Removal
Removing cured conformal coatings by chemical treatment requires immersion of the coated board or treating localized areas with the chemical stripping solution. Several companies manufacture materials that dissolve/ attack conformal coatings
Thermal Heat Removal
Two techniques are possible to remove a cured conformal coating depending upon the temperature sensitivity of the components located on the printed circuit board.
1) Heat the entire board to 150°C [300°F] and strip the coating once it softens (while still hot).
2) Use a hot-air de-soldering tool or a solder gun to remove spot areas of the coating. Apply the heat source to the treated area and remove the coating as it softens. Exercise care not to damage heat-sensitive components or traces. These methods are useful when the surrounding area does contain heat-sensitive components since it directs the hot air to one spot. When heat sensitivity is not a factor, a heat gun capable of 200-230°C [400-450°F] may be used to heat the area.
Mechanical Removal
Scraping or cutting the conformal coating may be an option for some applications and is easier with thicker, more flexible coatings. Pressurized abrasive systems - like micro-abrasive blasting - are often used to safely remove cured coatings. The abrasive is easily separated from the surfaces without danger to the components or reworking process. This technique is fast, cost-effective, and environmentally clean. It also enables you to selectively remove the coating from a specific targeted area, while causing no damage to the surrounding components.
Industry Category