What Are the Applications of Automotive PCB in Manufacturing?
By:PCBBUY 05/25/2023 16:14
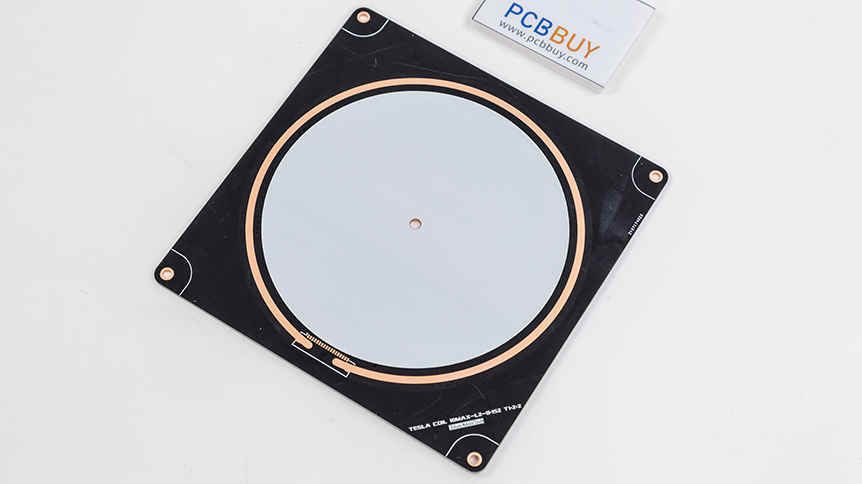
Automotive printed circuit boards from MCL are designed specifically to support each individual application and work in the real-world environments they will experience, whether they’re in the dashboard, under the hood or in areas of significant motion.
Do you know the basic information of automotive PCB? Do you know the applications of automotive PCB? In this passage, we are providing all the details about automotive PCB, if you are searching for more knowledge about it, please check and read the content below.
Why we use automotive PC B?
The popularity of printed circuit boards for vehicles can be attributed not only to its functionality, but also because of its many other benefits. This is a welcomed innovation in vehicle manufacturing as it has extensive applications. Other alternatives will not be able to take over its functions, or will at least not suffice in terms of their quality.
It’s important that your PCB manufacturer is capable of producing very small circuit boards as most vehicle types that use printed circuit boards only allow a limited amount of space for electronic control devices. Don’t let the small size full you. Circuit boards can be programmed to perform system essential commands no matter how big, or small, they are. Almost everything you see in your vehicle that is digitally displayed is most likely controlled by a circuit board. Another reason the automobile industry has adopted the use of PCBs in vehicles is because they are very easy to repair. Once a PCB has been created, it’s easy to reproduce for a quick repair.
What are the applications of automotive PCB?
Because there are so many different types of electronic systems in today's cars, the types of PCBs needed for automotive electronics vary greatly. The same car may require flex PCBs, rigid PCBs and rigid-flex PCBs for different technologies. As people demand more accessories and features for their cars that are powered by electronic components, the need for automotive PCBs of varying types is only growing.
Car PCB manufacturers need to provide a wide variety of PCB options. The kinds of systems and operations that now use printed circuit boards for enhanced efficiency and safety include rear LED lights and running lights, transmission controls and comfort control units. You can also find car PCBs managing engines, entertainment systems, digital displays, radar, GPS, power relays timing systems, mirror controls and a lot more.
Not only do automotive circuit board manufacturers need to offer a variety of types of PCBs, but those who manufacture, assemble and ship printed circuit boards for the car industry must also be able to supply boards with the types of materials that can stand tough use and support long life cycles. This means high-temperature PCBs that allow the PCB to dissipate heat quickly, are crucial.
The demands for safety, convenience, and connectivity require circuit board design to keep pace – if not stay a step ahead. Advancements in the automotive industry meant PCB applications had to accommodate these complex systems.
All new cars require computers to operate. PCBs are at the heart of these system designs and can range in type – including single-sided, double-sided, multilayer, rigid, flexible, and so on. They cover a broad range of applications that are spread throughout a vehicle’s operating systems.
How to choose the proper material for automotive PCB?
· Ceramic Substrate board – The ceramic substrate is made from high temperature co-fired alumina and aluminum nitride. These boards are implemented in the engine compartment since they can withstand high-temperature variations.
· PTFE PCBs – Polytetrafluoroethylene (PTFE) PCBs tolerate high-frequencies and find their purpose in safety systems and Radar technology.
· Metal Core PCBs – The Metal Core PCBs consist of aluminum base layer. The base layer is an aluminum alloy sheet on top of which the entire board is built up. The base layer act as a heatsink and thus are suitable for heat transfer applications. The metal core boards provide improved electrical insulation and thermal conductivity. These boards are employed in the Antilock Braking Systems (ABS).
· Heavy copper PCBs – The Automotive printed circuit boards employ thicker copper (Cu) in the outer and inner layers of the boards. These heavy copper boards are preferred over the regular ones since they can withstand high temperature, high frequency, and high current variations. The regular boards display a copper thickness of around 25µm to 50µm. Whereas, the heavy copper PCBs will be 150µm to 200µm thick. These boards are implemented in safety and signaling systems.
With more and more chips being integrated, the material that holds them together will play a prominent role.
The automotive PCBs must qualify the stringent thermal cycling test, thermal shock test, and temperature humidity test before they are taken into consideration. The boards must restrain from Conductive Anodic Filament (CAF) defects in the dielectric. The CAF can lead to short between the Copper Clad Laminate (CCL) and the conductive traces.
Industry Category