What Are the Causes of PCB Delamination?
By:PCBBUY 03/31/2025 14:59
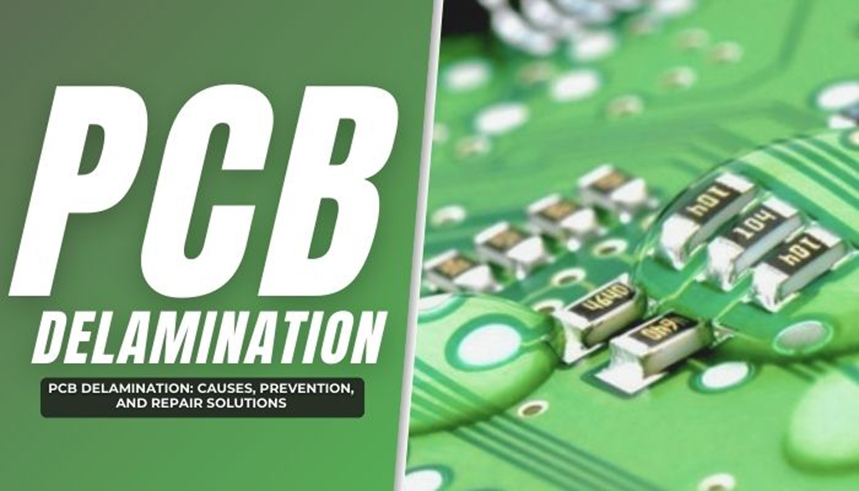
Introduction
PCB delamination is one of the most critical failure modes in printed circuit board manufacturing, leading to reduced reliability, electrical failures, and even complete device malfunction. Delamination occurs when the layers of a PCB separate due to weakened bonds between copper, substrate, and prepreg materials.
This 5000+ word technical guide examines the root causes of PCB delamination, including material defects, manufacturing process errors, environmental factors, and design flaws. The article provides data-driven insights, failure analysis methodologies, and preventive measures based on IPC standards, industry research, and case studies.
1. Understanding PCB Delamination: Definition & Impact
1.1 What is PCB Delamination?
Delamination refers to the separation of PCB layers due to:
Loss of adhesionbetween copper and dielectric material.
Internal cracking within the substrate or prepreg.
Bubble formation (voids) due to moisture or gas expansion.
1.2 Consequences of Delamination
Effect |
Failure Mode |
Typical Symptoms |
Electrical Failure |
Broken traces, short circuits |
Intermittent signals, no power |
Thermal Stress |
Overheating due to poor dissipation |
Burnt components, warping |
Mechanical Failure |
Cracks under vibration |
Broken solder joints, loose parts |
2. Primary Causes of PCB Delamination
2.1 Material-Related Causes
A. Poor Laminate Quality
Low Tg (Glass Transition Temperature) Materials
If Tg is too low, heat from soldering or operation weakens bonds.
Recommended Tg: ≥170°C for lead-free assembly (IPC-4101 Class D).
Laminate Type |
Tg (°C) |
Delamination Risk |
FR-4 Standard |
130-140 |
High |
FR-4 High Tg |
170-180 |
Moderate |
Polyimide |
250+ |
Low |
B. Moisture Absorption
Hygroscopic materials (e.g., some FR-4) absorb moisture, causing steam pressure during reflow.
IPC-1601 recommends baking PCBs before assembly if exposed to humidity >60% RH.
C. Copper Adhesion Failure
Poor oxide treatment before lamination reduces bonding strength.
Acceptable Peel Strength (IPC-650 2.4.8):
1 oz Cu: ≥8 lb/in
2 oz Cu: ≥10 lb/in
2.2 Manufacturing Process Defects
A. Improper Lamination Pressing
Insufficient pressure/temperature during lamination leads to weak bonding.
Optimal Lamination Conditions (FR-4):
Temperature: 180-200°C
Pressure: 300-500 psi
B. Drilling & Via Formation Defects
Rough hole walls from dull drill bits cause resin cracks.
Desmearing issues leave debris, reducing adhesion.
C. Reflow Soldering Stress
Lead-free soldering (260°C+) exceeds some materials’ Tg, causing layer separation.
Thermal Shock Test Results (IPC-TM-650 2.6.7):
FR-4 Standard: Fails after 100 cycles
High Tg FR-4: Survives 300+ cycles
2.3 Environmental & Operational Causes
A. Thermal Cycling Stress
Repeated expansion/contraction from power cycling weakens bonds.
Automotive/Aerospace Standards (IPC-9701):
Test Condition: -40°C to +125°C
Pass Criteria: No delamination after 500 cycles
B. Chemical Exposure
Flux residues, cleaning solvents can degrade adhesives over time.
Compatibility Testing (IPC-CH-65B):
Isopropyl alcohol: Safe
Chlorinated solvents: Risk of delamination
3. Testing & Detection Methods for Delamination
3.1 Non-Destructive Testing (NDT)
Method |
Detection Capability |
Limitations |
Ultrasonic Scanning |
Detects internal voids/cracks |
Requires skilled operator |
X-Ray Inspection |
Reveals hidden layer separation |
Limited to high-end labs |
Thermal Imaging |
Identifies hotspots from delam |
Only works under power |
3.2 Destructive Testing
Cross-Sectioning (Microsection Analysis)
Cuts PCB to inspect layer integrity (IPC-TM-650 2.1.1).
Solder Float Test (J-STD-003)
Submerges PCB in molten solder to check for blistering.
4. Prevention & Mitigation Strategies
4.1 Material Selection Guidelines
Requirement |
Recommended Material |
Delamination Resistance |
High-Temp Applications |
Polyimide, Rogers 4000 series |
Excellent |
Cost-Sensitive Designs |
High Tg FR-4 |
Good |
High-Frequency PCBs |
PTFE (Teflon-based) |
Moderate |
4.2 Process Controls
Pre-Bake PCBs (125°C for 4-12 hrs) if moisture exposure >60% RH.
Optimize Lamination:
Pressure: 350-450 psi
Temperature Ramp Rate: 2-3°C/min
4.3 Design Best Practices
Avoid large copper planes without thermal reliefs (causes uneven expansion).
Use via-in-pad cautiously (increases stress points).
5. Case Study: Delamination in Automotive ECUs
Failure Mode: Delamination after 2 years in under-hood environment.
Root Cause: Moisture ingress + thermal cycling beyond Tg.
Solution: Switched to polyimide substrate + conformal coating.
Conclusion
PCB delamination stems from material defects, manufacturing errors, and environmental stress. By following IPC material standards, optimizing lamination processes, and implementing rigorous testing, manufacturers can significantly reduce delamination risks.
References
1. IPC-4101 – Specification for Base Materials
2. IPC-TM-650 – Test Methods Manual
3. IPC-1601 – Handling Moisture-Sensitive PCBs
4. J-STD-003 – Solderability Testing
5. "PCB Failure Analysis Handbook" – Microtek Labs
Industry Category