What Are the Causes of Solder Bridge in PCB?
By:PCBBUY 11/20/2023 14:08
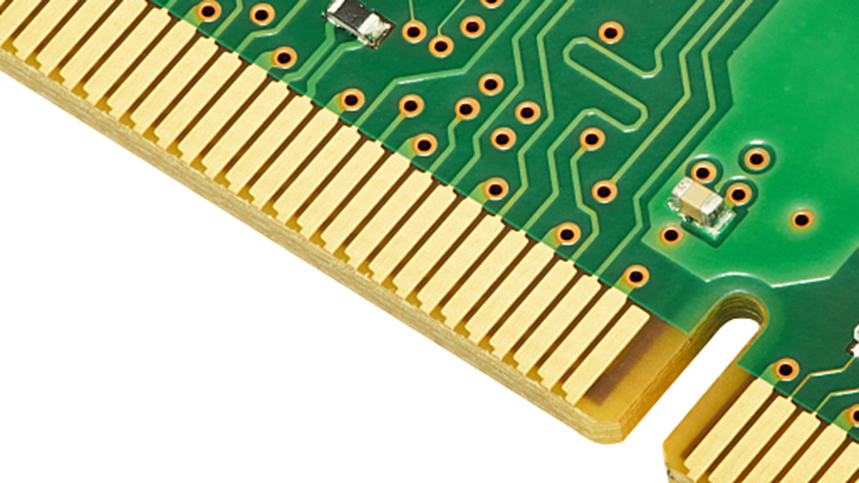
To have a perfect understanding of what bridge soldering is, you have to know what soldering is. Soldering is a way of bringing small pieces together on the surface of a circuit board. It connects electrical components on a PCB. Soldering is an important aspect of PCB manufacturing.
During soldering, materials such as soldering iron, soldering paste, and solder flux are used. The soldering process is simple and straightforward. However, mistakes occur. Therefore, bridge soldering is one of these mistakes.
In this passage, if you are searching for the definition of solder bridge and the methods to prevent it, please check and read the content below for more information.
What Are the Causes of Solder Bridge in PCB?
While there is no way to guarantee you never see solder bridges on your circuit boards, there are a few key things you can do in your design and preparation to greatly reduce your solder bridging risk.
Use the correct lead lengths for through-hole parts
Through-hole components with leads that are too long can cause solder bridges. The correct lead lengths for your application will depend on the size and thickness of your PCB, the size and mass of the component, and the type of soldering you plan to employ (wave, selective, etc).
Use the correct hole size and pad diameter for through-hole parts
Many solder bridges are the result of holes and/or surface pads that are too large. An annular ring pad that is too large decreases the distance between the solderable surfaces of two adjacent pins. This decreased distance, especially in a wave solder operation, greatly increases the risk of a solder bridge. So follow datasheets to correctly size both the plated through hole and the pad.
Design to the highest producibility level possible
Designing for producibility applies to both surface-mount and through-hole components and relates to the ease of producibility given the dimensions and spacings of your land patterns for your parts.
The IPC (Association Connecting Electronics Industries) publishes industry standards for PCB design and assembly, and they have defined Level A as the preferred level for general producibility. In some designs very small spacings are unavoidable, but in many designs, they are very avoidable. The best practice here is to avoid using unnecessarily small parts or tight spacing.
How to fix Solder Bridge of PCB?
There are several reasons why solder bridging occurs. This includes incorrect use of solder masks, excessive solder, incorrect soldering technique. This defect can be avoided at times. However, there are times it happens. It is, therefore, important to learn how to fix this problem. To fix a solder bridge, you need a solder flask, solder wick, and temperature adjustable soldering iron. Follow these steps to fix a solder bridge.
Monitor the temperature
Usually, you want a large tip to transfer sufficient heat into the solder wick. You need to monitor the temperature. Ensure the temperature is higher than the soldering temperature. This will compensate for the solder wick absorbing some heat from the joint.
For instance, if you solder at 270°C, you would have to increase the temperature to 300°C when utilizing the solder wick.
Surface tension
Surface tension refers to the possibility of fluid surfaces to shrink into the smallest area possible. The type of skills you have got and how effective your flux is might help you to wick the bridge away without needing a solder wick. You can utilize surface tension.
Surface tension helps to remove the solder from the bridge. You can fix a solder bridge without utilizing a solder wick. You just need to clean the top of the soldering iron before you try again. However, you need to be careful, heating the pin or pad severely with this approach can damage the integrated circuit or PCB pad.
What are the applications of solder paste in PCB?
Electronic components were first hand soldered onto circuit boards until the wave soldering process was perfected for the mass production of PCBs. Next came the development of surface mount parts which were smaller than their thru-hole counterparts due to their lack of long leads, and eventually they became the dominant component package type used on circuit boards. The lack of thru-hole pins in surface mount parts, however, forced the development of a new method of soldering in order to hold them in place on the board until the soldering was complete. This new process is known as solder reflow, and it doesn’t use the standard pool of molten solder that the wave process uses. Instead, a sticky solder paste is used to hold the parts in place and solder them as well.
Solder paste is a combination of a powder made up of metal solder particles and sticky flux that has the consistency of putty. The flux not only does its usual job of cleaning the soldering surfaces of impurities and oxidation, but it also provides a temporary adhesive that holds the surface mount components in place. The solder powder used in the paste can vary in its chemical composition with different material types and percentages used depending on the needs of the board being soldered. For instance, solder paste is available in both lead and lead-free versions to satisfy the restriction of hazardous substances (RoHS) directive. Solder paste is also classified by the size of the metal particles that make up the solder powder. These particles must be spherical in shape and can vary in size according to the type standards specified in IPC J-STD 005.
Industry Category