What Are the Challenges and Principles of ENIG in PCB Industry?
By:PCBBUY 09/27/2023 10:08
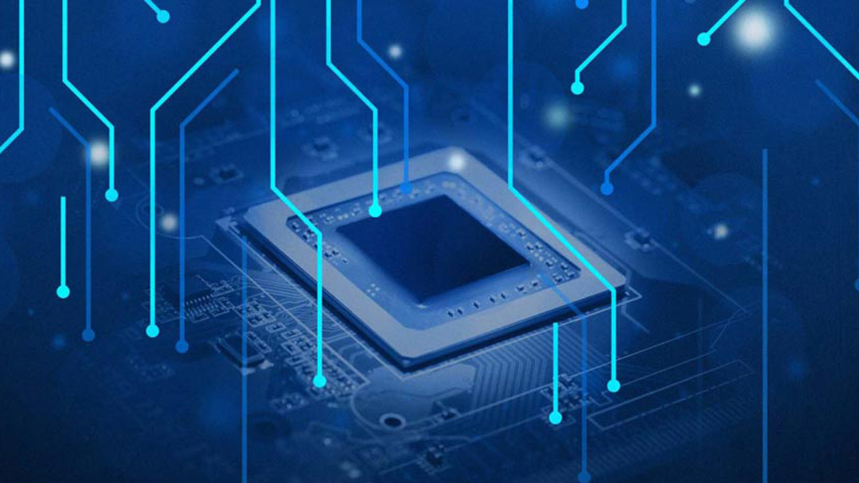
Many people look at gold purely for its monetary value, but engineers see things differently: gold is exceptional due to its remarkable corrosion resistance. This property is a lifeline for PCBAs with high-reliability requirements and those operating in demanding environments. In a perfect world, function and performance would trump expense, but the reality is that the benefits of gold plating come at a cost beyond the sticker price. Electroless nickel immersion gold, or ENIG, is a surface finish that melds the individual, separate characteristics of nickel and gold to produce a superior finish well positioned to meet many of the most difficult aspects of modern HDI design.
A Dive into ENIG’s Chemistry
ENIG melds autocatalytic and immersion processes under a single surface finish umbrella. As described by its name, ENIG contains an interstitial layer of electroless nickel deposited over copper capped with a layer of immersion gold. ENIG contributes more than soldering functionality; it applies to aluminum wire bonding and press-fit connections. Recent developments have propelled ENIG to become the premier surface finish option: the RoHS directive had manufacturers focus on a fully developed lead-free process and the increasing popularity of flex and rigid-flex printed circuits. However, the chemistry involved in ENIG makes it one of the more complicated, lengthy, and expensive surface finish choices.
ENIG’s core is the twin autocatalytic nickel and immersion gold processes. Autocatalytic processes continuously deposit metal with a reducing agent in the plating solution, creating a nickel-alloy co-deposition depending on the chemical composition of the reducing agent. A precious metal catalyzes the copper surface and prepares it for the electroless nickel step by lowering the activation energy requirement. This autocatalytic reaction is additive and unrestrained, requiring some control mechanism for cessation after the desired amount of nickel deposits over copper.
In comparison, the immersion gold step involves the gold atoms displacing accessible nickel atoms in the metallic substrate until no occupiable positions remain and the plating is complete. This restriction makes the gold plating process self-limiting, a valuable aspect for manufacturers when dealing with an expensive solution. Each metal contributes a crucial surface finish functionality, with the nickel layer a capable boundary to copper diffusion (making ENIG suitable for multiple reflow passes); the thin gold surface layer provides planarity and excellent protection against corrosion. This corrosion buffer is so robust that any attempts to strip plating (i.e., for board rework) are nearly guaranteed to damage the bare PCB board, resulting in scrap. While this tarnish resistance is undoubtedly an advantage of a successful ENIG surface finish, the lack of reworkability further underlines the process’s cost and relative complexity.
The Challenges and Rewards of the ENIG Process
ENIG is susceptible to a defect mode known as a black pad (the name derives from the appearance of the corroded nickel) that hinders solderability and produces poor solder joint integrity. Ideally, the gold displacement of nickel occurs uniformly on flat surfaces such that there is no deeper penetration into the nickel structure. In practice, additional corrosion occurs in the nickel substrate along grain boundaries or imperfections present from deposition. Reduced ductility and a buildup of internal stress in the nickel substrate can often arise due to the composition of the solution and its metal turnover (MTO) status. Each MTO – the number of replacements of the original amount of metal in the solution – indicates solution aging and a corresponding reduction in efficacy.
One method unmentioned for preventing black pad defects is an increase in the thickness of the nickel substrate. Intuitively, this makes sense, as there is no limit to the nickel plating process, and providing additional material should impede the depth of corrosion while limiting total damage to the nickel layer. Yet increasing the thickness of the nickel layer inhibits the ductility, a key performance metric for flex and rigid-flex printed circuits. Fortunately, there is a solution that balances the mechanical and chemical requirements of the ENIG process: the addition of a reducing agent to the nickel layer (typically 10~13% phosphorous by weight, more rarely boron) prevents corrosion during the immersion gold step while preserving the necessary minimum ductility.
While this may sound like a lot of labor, material, and cost–why not use a single-step solder process, one might ask–the benefits of a successful ENIG surface finish are well worth the trouble. Consider all the ways ENIG dovetails with the demands of today’s HDI designs:
Copper barrier – As circuits and devices continue to miniaturize, copper migration has a more pronounced effect on signal integrity through the attenuation of the signa
Industry Category