What Are the Common Defects of PCB Soldering?
By:PCBBUY 11/24/2023 14:56
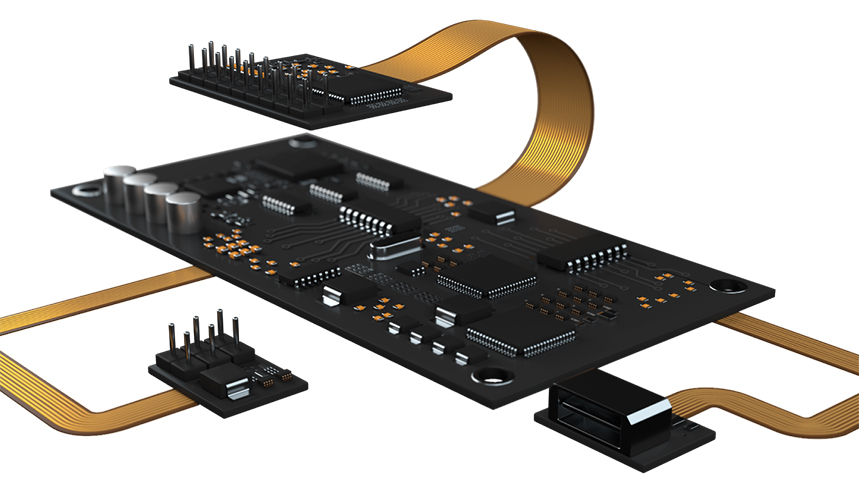
As smartphones, tablets, and wearable devices have become smaller, thinner, and more functional, PCBs and components continue to be even smaller, denser, and more layered. In the automotive industry, research and development of technologies such as automatic brakes and autonomous driving has promoted computerized control of important components. Such control then expects PCBs and electronic components to have high durability and reliability so as to withstand long-term stress caused by driving, accelerating, and stopping.
If you are searching for more information about PCB defect detection, you can check and read the content below in this passage for professional knowledge.
What Are the Common Defects of PCB Soldering?
Soldering defects can arise for a variety of reasons, ranging from operator error to pollutants. The most well-known -- and well-hated -- of these defects are:
· Opens
· Excessive solder
· Component shifting
· Cold joints
· Solder bridges
· Webbing and splashes
· Lifted pads
As frustrating as these defects can be, it’s a valuable lesson to experience them at least once. And, to pass the solderability test standard, knowledge of soldering defects is critical.
Pin and Connector Checks
One of the important components of PCB is the pin and connector, which help relay signals in operations. Incorrect placement of the pin can result in damage to the connector. To prevent this defect, you can use a pattern-matching tool to check the connector’s correct placement.
Thus, you can use this pattern-matching tool, usually in a vision tool kit, to locate and group patterns. Hence, it provides a score that indicates how much the patterns match the intended pattern or location.
However, to ensure the alignment of pins, you can use a telecentric lens. The magnification of a telecentric lens does not change, which prevents parallax error, which a conventional lens can cause. However, a thorough check of pins and connectors will go a long way in preventing this defect in cheap correct PCB service provider. Thankfully, there are various PCB manufacturing companies.
Heat Dissipation Analysis
Most electronic components tend to get unusually hot whenever they are working at their full capacity. Hence, this can lead to overheating if they are not properly checked. Also, a hot PCB heat sink can be a shock to unsuspecting technicians. Likewise, PCB’s extreme temperatures can lead to a reduced lifespan of products hence.
What is the importance of PCB failure analysis?
As smart phones, tablets, and wearable devices have become smaller, thinner, and more functional, PCBs and components continue to be even smaller, denser, and more layered. In the automotive industry, research and development of technologies such as automatic brakes and autonomous driving has promoted computerized control of important components. Such control then expects PCBs and electronic components to have high durability and reliability so as to withstand long-term stress caused by driving, accelerating, and stopping.
Terminals and devices now have an important role in various daily situations, and cars require a high degree of safety. Any failures and defects of important components that are computerized in such products can lead to serious trouble or accidents.
To evaluate the durability and reliability of PCBs and electronic components, reliability evaluation tests, including acceleration tests, have become increasingly important. In addition to such tests, using microscopes to identify defects and failure causes is more important than ever.
What are the common defects during PCB manufacturing?
The complexity of the PCB design and manufacturing processes means there are numerous opportunities for PCB failure issues to arise. Some of these failures are a result of design oversights, such as insufficient clearances or incorrect measurements, which can negatively affect the functionality of the finished product. Others may result from problems in the manufacturing process, such as drilling errors or over-etching, which can be equally catastrophic.
Fortunately, most of these errors can be avoided with knowledge and consideration for the manufacturing process, as well as awareness of the more common PCB manufacturing issues. To help you and your company better understand and avoid the potential errors in your printed circuit board designs, we’ve compiled a list of the most common issues experienced in PCB manufacturing, why they occur and how they can be prevented below:
Plating voids
Plated through-holes are copper-coated holes in a printed circuit board. These holes allow electricity to be carried from one side of the circuit board to the other. To create these holes, the PCB board fabricator drills holes through the circuit board, puncturing the material all the way through. A layer of copper is then added to the surface of the material and along the walls of these holes through an electroplating process.
Defects as a result of contamination, air bubbles or insufficient cleaning can be avoided by cleaning the material properly after drilling. Additionally, defects from faulty drilling can be avoided by closely following the manufacturer’s directions during use, such as the recommended number of drill hits, drill in-feeds and drill speeds. Both problems can be avoided by hiring a well-qualified and experienced PCB manufacturing company.
Insufficient copper-to-edge clearance
Copper is an incredibly conductive metal, which is used as an active component of PCBs. However, copper is also relatively soft and vulnerable to corrosion. To prevent corrosion and protect the copper from interacting with its environment, this copper is covered with other materials. However, when a PCB is trimmed, if the copper is too close to the edge, part of this coating can be trimmed as well, exposing the copper layer underneath. This can cause numerous problems in the functionality of the board.
Bad soldering
Improper soldering during PCB assembly can lead to major issues. One of the most common kinds of poor soldering occurs when a technician doesn’t heat the solder enough, leading to cold soldering, which can cause PCB failure. Additionally, moisture during the soldering process can contaminate the PCB pad and other components. This contamination can cause PCB components to burn and create connection problems. Companies often use visual or X-ray inspections to detect bad soldering.
Slivers
Slivers are narrow wedges of copper or solder mask produced during the PCB manufacturing process and can cause serious problems during the fabrication of circuit boards. These slivers are often produced during the etching process and can occur in one of two ways.
First, slivers can be produced when an extremely long, thin feature of the copper or solder mask is etched away. In some cases, this sliver detaches before it fully dissolves. These detached slivers can float around in the chemical bath, and can potentially land on another board, adding an unintended connection.
Industry Category