What Are the Common Issues of DFM in PCB?
By:PCBBUY 03/18/2024 14:32
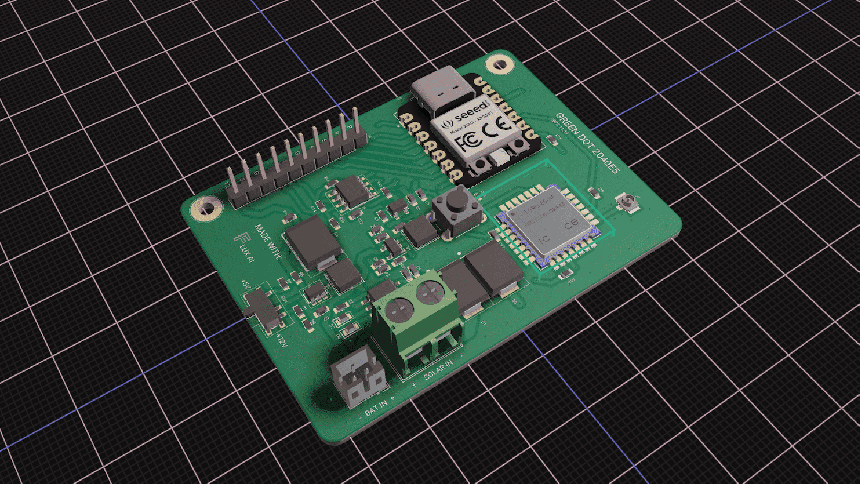
Despite how important PCB DFM guidelines are, there are no generic guidelines that apply to every single type of PCB design. This means that designers must often use their best judgment concerning which guidelines to follow.
Do you the function of DFM in PCB design? If you are searching for more information about DFM in PCB design, please check and read the content below for professional knowledge.
What Are the Common Issues of DFM in PCB?
Avoiding DFM issues is a better approach than letting it ruin your PCB design and then looking for a remedy. DFM needs smart moves from the designer’s side. It is solving problems before they appear. DFM issues can be due to:
Non-functional PCB design
Board functions but not as intended (within the specification). It happens due to component mismatch and timing errors in a PCB.
Random failure that does not reflect any connection with the possible situation
Keeping track of DFM rules and consistent DFM checks can help the designer to avoid the following DFM issues:
DFM issues due to acid traps
To define acid traps, we need to know how traces are laid on the PCB surface. If any copper feature is bending anywhere below 900 (acute angle), it may act as an acid trap during PCB fabrication. It happens before washing when residual acid gets collected in these trap areas and not cleared away. Due to these traps, the desired copper feature starts to erode (over-etching), creating an ‘open’ or lost connection. Avoiding acid traps is very important because today’s PCB traces are very thin, say 4 or 5 mils.
What are the considerations of DFM in PCB?
Ensuring that a circuit board design is manufacturable according to standard DFM rules can save time and money by checking for some of the following design problems:
· The parts ordered for the board are correct and match all of the land patterns.
· Placed components have sufficient space between them for automated and manual assembly.
· The components are also oriented correctly for automated soldering systems.
· Spacing between traces and other metal board objects conforms to the minimum requirements to avoid solder bridging and shorts.
· The board is set up with a test strategy that includes accessible test points for automated testing.
· These are a few of the conditions that a PCB contract manufacturer will be looking for when they conduct a DFM review of a circuit board design before the board enters production. If the board fails any of these areas, the PCB CM will recommend alterations to the layout to ensure the best assembly yields.
To ensure that the board is designed for system assembly, it should be checked for these additional problems:
· Accessibility: The circuit board must be installed, configured, and operated in its designated system.
· Mechanical fit: The board must also fit where it is designed to go. These checks include correctly interfacing to support brackets, braces, connectors, and wire harnesses.
· Adequate clearance: The board must have enough clearance to other parts of the system. Will it interfere with the movement of any other system components, and will it have adequate cooling where it is positioned?
· Electrical connectivity: Even if all of the physical connections are a match, it is still important to verify that the pin-outs of the connectors match electrically. It is not uncommon for board-to-board connectors to be mistakenly pinned out backward.
What is the importance of DFM in PCB?
Most industries use DFMA or Design for Manufacturing and Assembly techniques to mainly minimize product cost through improvements in design and process. Two procedures make up the term—Design for Manufacturing (DFM) and Design for Assembly (DFA)—with many differences and similarities between the two. Rush PCB explains why DFMA techniques are essential in the PCB industry.
DFM & DFA — DIFFERENCES
While DFM strives to optimize the manufacturing process, DFA seeks to optimize a part or system assembly. To put that in simpler terms, DFM is concerned with reducing overall production costs, but DFA is concerned only with reducing the product assembly costs. In other words, while DFM helps to minimize the complexity of manufacturing operations, DFA helps to minimize the number of assembly operations.
DFM & DFA — SIMILARITIES
Both DFM and DFA procedures help in reducing material, labor, and overhead costs. In striving to reduce costs, both technologies tend to utilize standards. Both procedures strive to shorten the time involved in the development cycle of a product.
Industry Category