What Are the Considerations of PCB Selective Soldering Process?
By:PCBBUY 03/04/2024 16:24
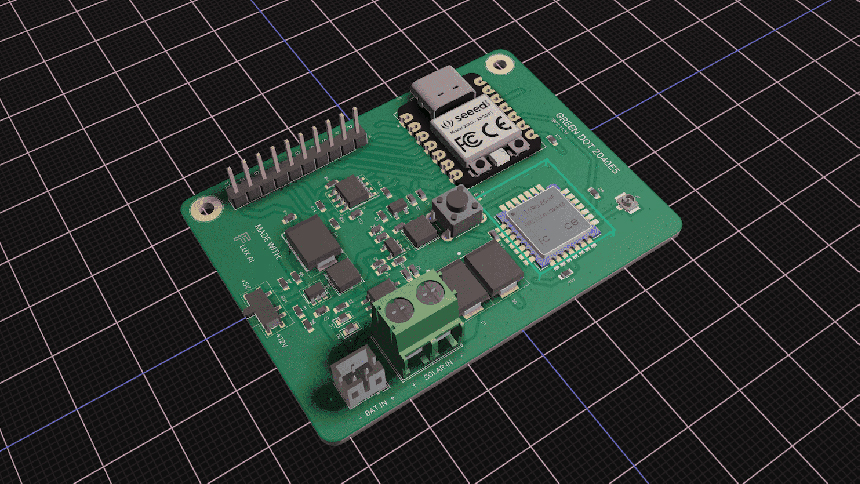
High reliability assembled PCB prototypes as well as novel surface mounted devices (SMD) and mixed systems must be assessed according to well defined qualification test plans. Such high reliability verification programmes are not limited to just evaluate the robustness, reliability and performance of the product but they also address the verification of tools, fabrication procedures and involved materials, as well as the confirmation of product integrity.
In this passage, we are going to tell you everything about PCB selective soldering. If you are going to search for more information about PCB selective soldering, please check and read the content below for professional knowledge.
What Are the Considerations of PCB Selective Soldering Process?
PCB Size
The maximum size PCB that needs to be processed will have a bearing on the machine selection. If the PCB’s to be processed are not too big then many machines can be configured to have two conveyors to process twice the number of assemblies. Another option based on PCB size is to have a second solder pot to speed up the soldering process which quite often is the bottle neck.
Floor Space
The amount of floor space available will need to be considered – Selective soldering machines vary in size from compact machines that process one assembly at a time to much larger in-line machines that also need board handling for processing larger volumes.
Maintenance
Depending on how much the selective soldering machine is planned to be used the amount of maintenance can vary mainly depending on the technology within the solder pot. Many manufacturers use an impeller to drive the solder which can generate a fair amount of dross which if not regularly removed will cause undesirable results. The more expensive machines use electromagnets to drive the solder which as well as being lower maintenance, achieve a much steadier wave for higher accuracy soldering.
Solder Type
There are a number of different solder alloys that can be used within a selective soldering machine. Some companies are using leaded solder but most will be using a lead-free alloy which generally operates at a pot temperature of between 270 deg c and 300 deg c. There are some newer lead-free alloys on the market which need less temperature and operate at a pot temperature of around 250 deg c.
Solder Pots
Within the selective soldering process of flux, preheat & solder, the soldering process tends to take the longest time and so to balance the process manufacturers sometimes offer the option to add solder modules to the overall system.
Some selective soldering machines use more than one solder pot per module and can be configured differently depending on how the machine is intended to be used. Possible configurations are:-
· Different solder alloys in each pot
· Variable Z axis on both pots allowing different size nozzles to be fitted
· Variable Y axis between pots allowing two PCB’s on one panel to be soldered at the same time on single conveyor system or two separate PCB’s on dual conveyor system.
When Selective Soldering Is the Most Effective
There are some conditions in which wave solder cannot be used, and hand soldering is not effective. In these cases, the only choice left is using the selective solder system. Some of these conditions include:
· Tall component height: The height of the solder wave has limitations, and some components are tall enough that they will block the wave from soldering the board.
· Tight component spacing: When thru-hole components are placed too close to SMT components, there might not be enough room to fit a protective fixture around the SMT parts that will allow effective wave soldering.
· Uneven heating: Thick boards, or boards with thick copper layers for power and ground planes, can cause a problem for hand soldering. It is difficult to get a single soldering iron to heat all of the thermally connected metal in the board sufficiently enough for the solder to flow through the holes to form a good solder joint.
· Dense concentration of thru-hole pins: When large connectors are being used with hundreds of pins, it can be difficult for a soldering iron to get into each pin to solder them all effectively.
In all of these situations, selective soldering can provide the solution. In addition to its ability to be programmed to handle unique pin configurations, selective solder also has other benefits as well. The selective solder system will utilize a far-side infrared preheater to balance uneven heating of thick copper boards. It can also use a wider nozzle that can solder two or three rows of connector pins in a single pass, considerably cutting the amount of time needed for soldering. This ability to quickly solder hard-to-reach areas that were traditionally only able to be hand-soldered is where selective solder really shines.
Another benefit that a contract manufacturer that offers selective soldering is in its consistency. Hand soldering can understandably produce variations in its results, but the selective soldering system will repeatedly give you the same consistent solder joint each and every time.
Industry Category