What Are the Environmental Factors of Electronic PCB Failures?
By:PCBBUY 11/21/2023 16:02
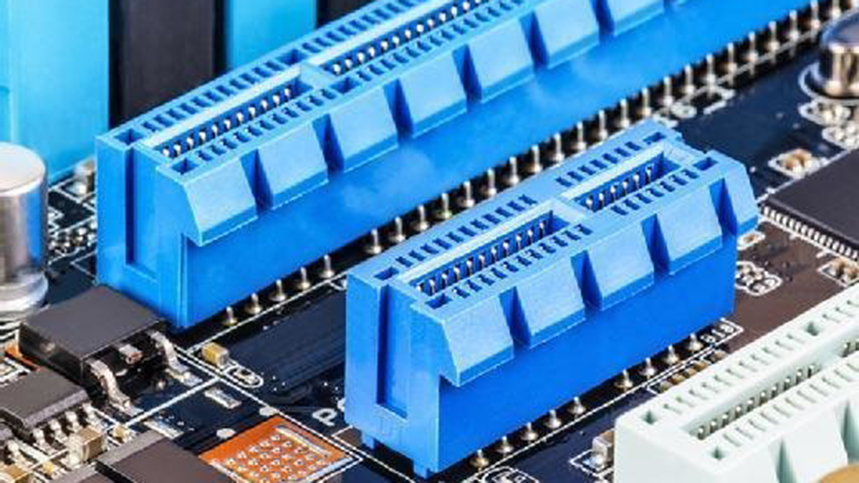
PCBs are prone to a variety of defects that impede proper manufacturing, costing companies money. Defects such as shorts, spurs, mousebites, and pinholes cause issues like current leakage and open circuits, quickly degrading performance or rendering PCBs useless. PCB manufacturers must strive to ship defect-free units to remain competitive and ensure customer satisfaction.
The main objective of Etching process is to remove the exposed unwanted copper other than the required circuit pattern. In order to minimize scrap caused by the wrongly etched PCB panel, inspection has to be done in early stage. If you are looking for more information about PCB fault detection, please check and read the content below.
What Are the Environmental Factors of Electronic PCB Failures?
If you have resided in a warm-weather climate (Florida) for the majority of your life, then you can relate to a new recruit (Me) serving in the Navy in Great Lakes, Illinois experiencing culture shock during his first Chicago, winter. I can attest that temperature is a disruptive environmental factor.
Well, temperature is also a disruptive environmental factor when it pertains to electronic circuits. Temperature changes can indeed cause an electronic circuit to fail and in turn, cause a PCB’s malfunction. As you may know, with temperature changes, you will experience expansion and contraction of the PCB. These expansions and contractions, in turn, brings about the potential risk of a warped board and damage to solder joints.
Another equally devastating environmental factor is moisture. If moisture is introduced to your electronic circuits, it can cause rust, oxidation, and corrosion.
How to build application of PCB fault detection?
With all of the parts, connections, and other critical aspects of a circuit board that must be examined, some complicated PCBs can have up to three or four thousand opportunities for errors. Locating a single problem out of so many possibilities is simply too many for manual inspection methods to reliably find, especially when you consider the volume of boards.
Failure analysts are employed to ensure defects are kept to a minimum. But inspecting and diagnosing defects manually is challenging. There are multiple defects to detect, an extremely low tolerance for errors, and significant expertise required to reliably recognize and handle flawed units. Considering the time to train new analysts, and the cognitive load required to ensure reliability, an automated solution to detecting and classifying defects in PCBs is in demand.
In this article we will build a full PCB Defect Classifier that automates the task of detecting and classifying defects in printed circuit boards. I always encourage AI practitioners to build full products rather than throwing models over the fence to developers and other engineers. Your machine learning must exist in concert with a full application; thus only through its survival inside a holistic product can you be certain you’re building for users, not engineers.
How PCB fault detection using image processing inspects a circuit board?
Depending on what portion of the circuit board is being inspected, different AOI systems are used. Solder paste inspection equipment, for instance, will use laser scanners with micron resolution to determine the amount of solder on a pad.
The automated optical inspection systems used for PCB assembly verification rely on LED illumination and high-resolution cameras to capture circuit board images. Using a known good, or “golden” first article board, the AOI system will capture images of its part markings and solder joints. These images are clear enough to record polarity indicators, color codes, and other markings and compare subsequent circuit boards. Once recorded, the system can detect incorrectly aligned components, open solder joints, and solder bridges on new boards using the standard.
The image recognition can also be de-tuned to reduce false detections or increase its sensitivity for extra critical areas of the board. AOI systems can also be programmed to accept alternate part numbers to keep acceptable replacement parts from being flagged as errors. This ability to fine-tune the AOI system allows operators to configure it to its most optimum level for fault detection. Now let’s take a look at the actual inspection process used during manufacturing.
What are the PCB common faults?
Soldering fault
The bulk of printed circuit board defects can be traced back to a soldering issue. Soldering is a technical skill that becomes even more difficult when dealing with the extremely small components on a printed circuit board. Soldering defects can be minimized both during the design process, and during the soldering process. Some of the most common soldering defects include:
Open joints, sometimes called “dry joints,” occur when the solder doesn’t bond correctly with the point of contact, typically the pad. Open joints do not always cause your circuit to fail, since there may be solder there that makes poor or occasional contact. Open joints are caused by physical movement or bending, incorrect solder temperature, design or manufacturing errors, as well as impact and shifting during use or transport.
Temperature fault
Printed circuit boards are affected by temperature, both in storage, and when they are installed in components. Extreme temperatures or large temperature fluctuations may cause components or joints to break or fail. Many people take the maximum or minimum safe temperature into consideration, without thinking about the fluctuations in temperature that may occur either during operation or in storage. Temperature fluctuations can cause expansion and contraction to take place too quickly, causing premature failure of the printed circuit board.
Plating fault
Holes carry electricity from one side of the board to the other. Plating of the hole wall during manufacture. During this, By establishing the electrical conductivity from the top in the endplate portion depositing copper.
If the copper deposition is incorrect, it will create plating voids, leaving gaps in the wall with no copper coating. It could happen due to air bubbles, contamination in the holes, contaminated materials, and other similar reasons. You can prevent this from happening by following the manufacturer’s direction and cleaning the equipment as instructed.
Industry Category