What Are the Equipment Used in PCB Manufacturing?
By:PCBBUY 10/31/2024 17:10
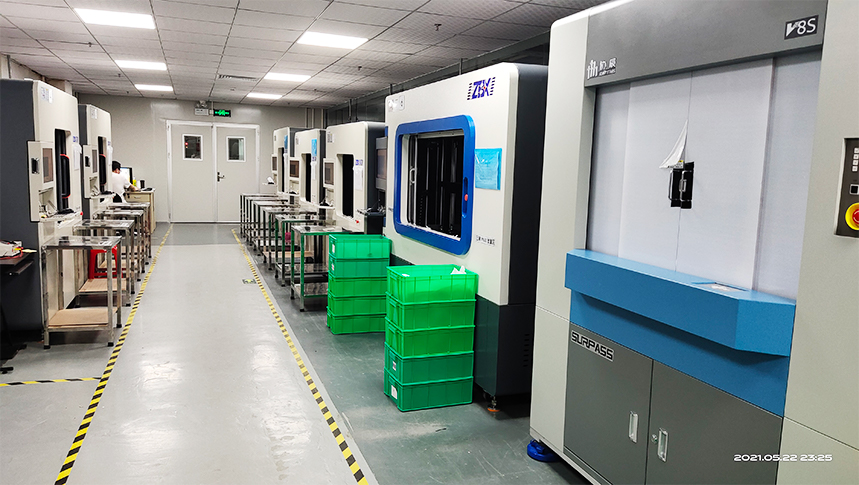
Printed Circuit Boards (PCBs) are fundamental components in electronic devices, providing the necessary connections for electrical signals. The manufacturing of PCBs involves a complex process that utilizes various specialized equipment. This article explores the equipment used in PCB manufacturing, detailing their functions, principles, and the overall impact on production efficiency and quality.
Overview of PCB Manufacturing Process
PCB manufacturing encompasses several key stages: design, material preparation, etching, drilling, plating, solder mask application, surface finish, and final inspection. Each stage requires specific equipment that plays a crucial role in ensuring quality and efficiency.
1. Design and Layout Software
Before any physical manufacturing begins, the PCB design process is crucial. Designers use specialized software to create layouts that define the circuit pathways and component placements.
Key Features of PCB Design Software:
Schematic Capture: Allows designers to create circuit schematics, facilitating the visualization of electrical connections.
Layout Design: Converts schematics into physical layouts, defining the traces, pads, and vias needed on the PCB.
DRC (Design Rule Check): Ensures that the layout meets manufacturing specifications to avoid issues during fabrication.
2. Material Preparation Equipment
Once the design is finalized, the next step is preparing the substrate materials used for the PCB. Common materials include FR-4 (a glass-reinforced epoxy laminate) and polyimide.
Equipment for Material Preparation:
Laminators: Used to bond multiple layers of material together, essential for multilayer PCBs. The process involves heat and pressure to ensure proper adhesion.
CNC Routers: These machines cut the PCB substrates to the desired dimensions, ensuring uniformity across all boards.
3. Imaging Equipment
Imaging is a critical step that transfers the PCB design onto the substrate. This involves applying a photoresist layer and exposing it to light.
Types of Imaging Equipment:
Film Plotters: Produce high-resolution film negatives of the PCB design, which are used for exposure.
Direct Imaging Systems (DI): These systems use laser technology to directly image the photoresist on the substrate, eliminating the need for film.
4. Etching Equipment
Etching removes unwanted copper from the PCB to create the desired circuit patterns. This process is typically done using chemical etchants.
Types of Etching Equipment:
Wet Etching Systems: Use liquid chemicals to dissolve excess copper. Common etchants include ferric chloride or ammonium persulfate.
Dry Etching Systems (Plasma Etching): Utilize gases to etch the copper layer. This method allows for greater precision and is often used for fine features.
5. Drilling Machines
Drilling is necessary for creating vias and holes for component leads. Precision is critical to ensure that holes are correctly aligned and sized.
Types of Drilling Machines:
Automated Drill Machines: These machines can drill multiple boards simultaneously, improving efficiency. They use high-speed spindles to create precise holes.
Laser Drilling Systems: For ultra-fine vias, laser drilling offers the precision needed for high-density interconnect (HDI) boards.
6. Plating Equipment
Plating is essential for creating conductive pathways between layers and reinforcing vias. This process typically involves electroplating.
Types of Plating Equipment:
Electroplating Tanks: These tanks allow for the deposition of a thin layer of metal (usually copper) onto the PCB surface. The process is driven by an electrical current that facilitates metal deposition.
Immersion Gold Plating Systems: Used for creating a corrosion-resistant surface finish on pads and vias, immersion plating provides excellent solderability.
7. Solder Mask Application Equipment
Solder masks protect areas of the PCB from solder during assembly. Applying a solder mask is crucial for preventing solder bridging and ensuring reliable connections.
Types of Solder Mask Application Equipment:
Solder Mask Printers: Use a screen printing process to apply solder mask material to the PCB.
Liquid Photoimageable (LPI) Solder Mask Systems: These systems allow for a finer application of solder mask using photoresist technology.
8. Surface Finish Equipment
Surface finish treatments are applied to protect exposed metal and enhance solderability.
Common Surface Finishing Techniques:
HASL (Hot Air Solder Leveling): This process involves coating the PCB with solder, followed by hot air to remove excess. This is a traditional method but can be less favorable due to environmental concerns.
ENIG (Electroless Nickel Immersion Gold): ENIG provides excellent corrosion resistance and is widely used for high-reliability applications.
9. Inspection and Testing Equipment
Quality control is vital in PCB manufacturing to ensure that boards meet specifications and function as intended.
Types of Inspection Equipment:
Automated Optical Inspection (AOI): Uses cameras to inspect the PCB for defects in soldering and component placement.
X-Ray Inspection Systems: Essential for inspecting hidden solder joints, such as BGAs and CSPs.
Testing Equipment:
Functional Testers: Validate that the PCB operates as designed by applying electrical signals and measuring responses.
In-Circuit Testers (ICT): Check for electrical connectivity and proper functionality of individual components on the PCB.
10. Cleaning Equipment
After the assembly process, cleaning is essential to remove flux residues and contaminants.
Types of Cleaning Equipment:
Ultrasonic Cleaners: Utilize high-frequency sound waves in a solvent solution to clean delicate PCBs without damaging components.
Aqueous Cleaning Systems: These environmentally friendly systems use water-based solvents to remove contaminants.
Conclusion
The equipment used in PCB manufacturing is vital for ensuring high-quality, reliable electronic devices. From design to final inspection, each piece of equipment contributes to the overall efficiency and effectiveness of the manufacturing process. Understanding these tools is crucial for professionals in the industry, as it aids in optimizing production methods and maintaining quality standards.
References
1. Smith, J. (2020). *PCB Design and Fabrication*. Electronics Publishing.
2. Johnson, L. (2019). *Advanced PCB Manufacturing Techniques*. Circuit Press.
3. Zhang, T. (2021). "Trends in PCB Manufacturing Technology," *Journal of Electronics Manufacturing*, vol. 45, no. 3, pp. 123-134.
4. "Automated Optical Inspection in PCB Manufacturing," (2022). PCB World. [Online]. Available: www.pcbworld.com/inspection.
5. "The Importance of Surface Finishing in PCB Assembly," (2021). Electronics Weekly. [Online]. Available: www.electronicsweekly.com/surface-finishing.
Industry Category