What Are the Essential Factors in PCB Soldering?
By:PCBBUY 09/26/2024 16:30
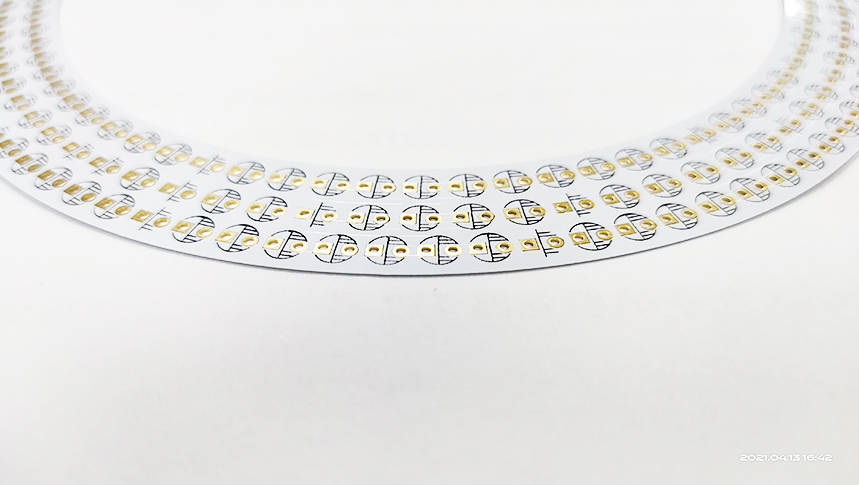
Soldering is a critical process in the assembly of Printed Circuit Boards (PCBs), playing a pivotal role in ensuring the reliability and functionality of electronic devices. This article aims to explore the essential factors in PCB soldering, including the principles of soldering, the types of solder, soldering techniques, and the impact of various parameters on solder joint quality.
1. The Basics of PCB Soldering
1.1 What is Soldering?
Soldering is a process that involves joining two or more electronic components together by melting solder, which typically consists of a mixture of tin and lead or lead-free alloys. The solder cools and solidifies, creating a strong electrical and mechanical bond.
1.2 Types of Solder
Solder can be categorized into two primary types:
Lead-based Solder: Composed primarily of tin (Sn) and lead (Pb), this type of solder has been widely used due to its excellent properties, including lower melting points and good flow characteristics.
Lead-free Solder: With growing environmental concerns, lead-free soldering has become prevalent. Common alloys include:
Tin-Silver-Copper (SAC)
Tin-Copper (SAC)
The following table summarizes the melting points and typical compositions of these solder types:
Solder Type |
Composition |
Melting Point (°C) |
Lead-based Solder |
60% Sn, 40% Pb |
183-190 |
Tin-Silver-Copper |
96.5% Sn, 3% Ag, 0.5% Cu |
217-220 |
Tin-Copper |
99.3% Sn, 0.7% Cu |
227-230 |
2. Principles of Soldering
2.1 Thermal Dynamics
The soldering process involves heat transfer, which can be described by Fourier’s Law of Heat Conduction:
2.2 Chemical Reactions
During soldering, several chemical reactions occur. The primary reaction involves the wetting of the substrate by molten solder. The wetting phenomenon can be described by Young’s equation:
3. Essential Factors in PCB Soldering
3.1 Component Design and Layout
Proper component design and layout on the PCB product affect the soldering process. Key considerations include:
Pad Size and Shape: The pads should be appropriately sized to accommodate solder and provide adequate surface area for bonding.
Clearance: Sufficient space between components allows for solder flow and reduces the risk of solder bridges.
3.2 Soldering Techniques
Different soldering techniques can influence the quality of solder joints. Common methods include:
Wave Soldering: Suitable for large batches, where the PCB is passed over a wave of molten solder.
Reflow Soldering: Used primarily for surface mount technology (SMT), where solder paste is applied to pads, components are placed, and then heated.
3.2.1 Wave Soldering Process
The wave soldering process involves several steps:
1. Preheating: The PCB is preheated to remove moisture and prepare the surface.
2. Solder Wave: The PCB passes over a wave of solder, which fills the pads and connects the components.
3. Cooling: The PCB is cooled, allowing the solder to solidify.
3.3 Temperature Control
Temperature control is vital in soldering. The following factors must be considered:
Soldering Temperature: The temperature must be high enough to melt the solder but low enough to avoid damaging components. Typical soldering temperatures range from 180°C to 250°C.
Duration of Exposure: Extended exposure to high temperatures can lead to component damage or thermal stress.
3.4 Flux Selection
Flux is used to promote wetting and prevent oxidation during the soldering process. There are several types of flux:
Rosin-based Flux: Provides good wetting and is commonly used in electronics.
Water-soluble Flux: Offers excellent cleaning properties but requires careful handling to prevent corrosion.
3.5 Cleaning and Surface Preparation
Proper cleaning and surface preparation are essential for ensuring good solder joint quality. Contaminants like dust, grease, and oxidation can hinder wetting and lead to weak joints.
4. Impact of Solder Joint Quality
4.1 Reliability Testing
The reliability of solder joints can be tested through various methods, including:
Thermal Cycling: Evaluates the performance of solder joints under temperature variations.
Mechanical Shock and Vibration Testing: Assesses the robustness of solder joints under mechanical stress.
4.2 Failure Modes
Common failure modes associated with solder joints include:
Cold Solder Joints: Result from inadequate heating, leading to poor electrical connections.
Solder Bridges: Occur when excess solder connects two pads, creating unintended electrical pathways.
5. Comparative Analysis of Soldering Methods
The following table compares various soldering methods based on efficiency, application, and cost:
Soldering Method |
Efficiency |
Application Type |
Cost |
Wave Soldering |
High |
Through-hole components |
Moderate |
Reflow Soldering |
Very High |
Surface mount technology |
High |
Hand Soldering |
Low |
Prototyping and repair |
Low |
Selective Soldering |
Moderate |
Mixed technology |
Moderate |
Conclusion
Understanding the essential factors in PCB soldering is crucial for ensuring reliable electronic assemblies. Key considerations include the choice of solder, soldering techniques, temperature control, flux selection, and cleaning processes. By paying attention to these factors, manufacturers can improve solder joint quality, enhance product reliability, and ultimately reduce failure rates in electronic devices.
References
1. Friedman, A. (2018). "Soldering Technology: A Comprehensive Overview." Journal of Electronic Materials
2. Hwang, J. (2020). "Advances in Soldering Techniques for Modern Electronics." International Journal of Electronics.
3. Katz, R. (2019). "The Science of Soldering: Principles and Practices." *Journal of Materials Science.
4. Liu, Y., & Zhang, T. (2021). "Reliability of Solder Joints in Electronics." IEEE Transactions on Components, Packaging and Manufacturing Technology.
5. Sullivan, J. (2022). "Flux Selection and Its Impact on Soldering Quality." Soldering & Surface Mount Technology.
Industry Category