What Are the Factors to Design for PCB Manufacturability?
By:PCBBUY 01/31/2024 14:51
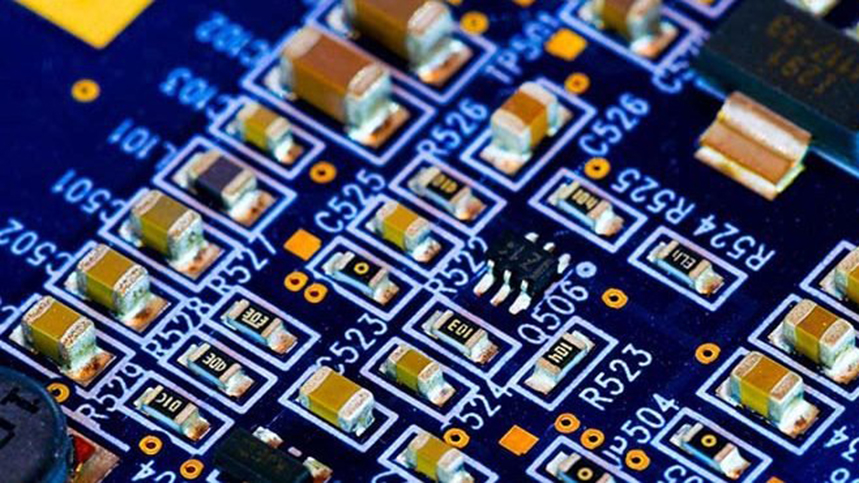
When a prototype circuit board is first being developed, the focus is usually on the functionality rather than the buildability of the board. As such the component placement on the board may not be optimized for assembly, which may result in higher assembly costs. Even during limited production runs for prototyping, a lot of manufacturing costs can be saved by designing the board for automated manufacturing.
These problems are magnified however when the board is ready to be moved into its production phase. Components that are not optimized for manufacturing will have to be re-positioned to avoid the necessity of manual assembly. As you can guess, having to solder even one component manually on a run of a thousand boards can quickly escalate manufacturing costs and delays. Another problem is with components that weren’t selected for long-term production. If their price is too high or their availability is limited, the board will encounter additional manufacturing problems.
In this passage, we are going to learn more about PCB DFM. If you are interested in the PCB DFM, please check and read the content below for more information.
What Do PCB DFM Guidelines Cover?
PCB DFM guidelines identify a variety of potential problems, including the following:
Physical problems, such as component crowding, are comparatively simple to find and correct, but other problems can be more insidious.
Electrical problems can occur even when following DFM guidelines. Layouts that have correct current flow may be difficult to solder evenly, which could in turn lead to uneven heating when current flows through the design.
Design document problems can come from discrepancies within a bill of materials (BOM) or within schematics, leading to uncertainty over which components to use during manufacturing.
Manufacturing difficulties can come from layouts that are difficult to create without causing damage to components, such as overlapping mounting holes that could jam and break drill bits.
There are many problems that robust PCB DFM guidelines can catch, and many of them aren’t found in design software. One of these problems is the acid trap, which happens when acid used for etching a PCB collects in undesirable areas of a board through surface tension. These areas can be tiny and easy to miss with the naked eye, but they can cause electrical problems or weaken the structure of the board.
What Are the Factors to Design for PCB Manufacturability?
If a PCB is performing appropriately and the design engineer is also satisfied with it, then why DFM checks? There are various reasons: cost of final PCB, design layout, and chances of future design failure.
· Theoretically, in cost terms, PCB designs submitted without DFM checks are less expensive than the designs with DFM checks. But it is better to pay a little extra so that the manufacturer could ensure whether the design is manufacturable or not.
· To sustain a PCB layout with DFM issues, CAM engineers edit the data to meet the design requirements. This is one primary reason that introduces signal integrity issues and EMI/EMC issues.
· PCBs assembled and tested efficiently, still fail. The main reason is that the design data still contained the DFM errors that were resolved in the prototype but were not implemented during the production.
How to choose material for PCB DFM?
Below are the parameters that should be considered while choosing materials that meet the design criteria:
· Moisture absorption
· Fire retarding
· Electrical properties
· Mechanical properties
· Thermal properties
See our post, how to choose PCB materials and laminates for fabrication to gain a better understanding of material characteristics and selection attributes.
Why DFM is important to PCB design?
Often design teams look at DFM as a “manufacturing problem” and something handled by their contract manufacturers or downstream partners. In fact, many manufacturers will perform DFM analysis prior to production to identify and fix issues. Where this process tends to fall apart is manufacturers often do not share any changes they made back to the design team and changes made are done without a full understanding of the design and its performance / electrical requirements.
The results can be devastating when a design team then sends what they think is the spec for the previously manufactured board off for a new rev, a new production line, or second source partner and soon realizes the PCB fails in some, most, or all of the finished devices. Performing your own analysis prior to the prototype could have detected those same issues and altered them in engineering, allowing you to incorporate the changes into the PCB design where they belong. Doing so would have lowered the cost, maintained design intent, and ensured follow-on builds also work correctly.
Industry Category