What Are the Inspection Techniques to Avoid PCB Component Failures?
By:PCBBUIY 03/27/2025 14:37
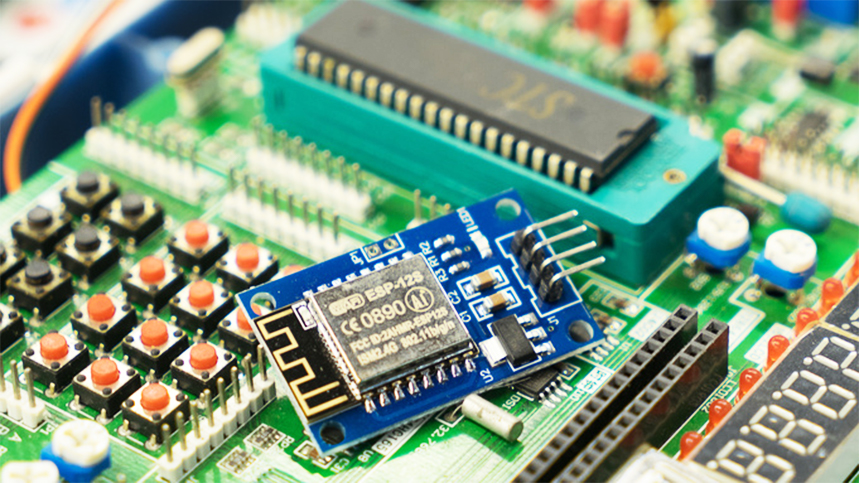
Introduction
Printed Circuit Boards (PCBs) are the backbone of modern electronics, and their reliability is critical in industries ranging from consumer electronics to aerospace. Component failures in PCBs can lead to costly recalls, system malfunctions, and even safety hazards. To mitigate these risks, advanced inspection techniques are employed at various stages of PCB manufacturing and assembly.
This article explores the most effective inspection methods to prevent PCB component failures, including Automated Optical Inspection (AOI), X-ray Inspection (AXI), In-Circuit Testing (ICT), Functional Testing (FCT), and Thermal Imaging**. We will analyze their principles, advantages, limitations, and real-world applications, supported by technical data and comparative tables.
1. Common Causes of PCB Component Failures
Before diving into inspection techniques, it's essential to understand why PCB components fail:
1.1 Manufacturing Defects
Solder Bridges (short circuits)
Cold Solder Joints (poor electrical connection)
Component Misalignment (misplaced or rotated parts)
Missing Components (omitted during assembly)
1.2 Environmental & Operational Stressors
Thermal Cycling (leads to solder fatigue)
Moisture Ingress (causes corrosion)
Electrical Overstress (EOS) (voltage spikes)
Mechanical Stress (vibration, bending)
1.3 Design-Related Issues
Poor Thermal Management (overheating)
Insufficient Trace Width (current overloading)
EMI/RFI Interference (signal degradation)
2. Key PCB Inspection Techniques
2.1 Automated Optical Inspection (AOI)
Principle: Uses high-resolution cameras and machine vision algorithms to detect surface-level defects.
Applications:
- Solder joint inspection
- Component placement verification
- Polarity checks
Advantages:
- Fast (up to 20,000 components/hour)
- Non-contact method
- Detects misalignments, missing parts, and solder defects
Limitations:
- Cannot inspect hidden joints (e.g., BGA, QFN)
- Requires proper lighting and calibration
Table 1: AOI Detection Capabilities
Defect Type |
Detection Accuracy |
Solder Bridges |
99.5% |
Missing Components |
99.8% |
Misaligned Components |
98.7% |
Lifted Leads |
95.2% |
2.2 X-Ray Inspection (AXI)
Principle: Uses X-rays to penetrate PCB layers and inspect hidden solder joints (e.g., BGA, QFN).
Applications:
BGA void detection
Internal trace integrity
Solder joint quality assessment
Advantages:
Detects subsurface defects
Works for high-density PCBs
Measures solder volume and void percentage
Limitations:
Expensive equipment
Slower than AOI (~5,000 components/hour)
Table 2: AXI vs. AOI Comparison
Feature |
AOI |
AXI |
Inspection Depth |
Surface Only |
Subsurface |
BGA Inspection |
No |
Yes |
Speed |
High (20K/hr) |
Medium (5K/hr) |
Cost |
$$ |
$$$$ |
2.3 In-Circuit Testing (ICT)
Principle: Uses a bed-of-nails fixture to test electrical characteristics of components.
Applications:
Open/short circuit detection
Resistance, capacitance, inductance measurements
Fault isolation
Advantages:
High fault coverage (~95-99%)
Tests power and signal integrity
Limitations:
Requires custom fixtures
Not suitable for high-frequency RF testing
2.4 Functional Testing (FCT)
Principle: Validates the PCB under real operating conditions.
Applications:
Power-up testing
Firmware validation
Signal integrity checks
Advantages:
Ensures end-product reliability
Detects system-level failures
Limitations:
Time-consuming
May not pinpoint **individual component faults
2.5 Thermal Imaging (Infrared Inspection)
Principle: Detects heat anomalies to identify overheating components.
Applications:
Thermal runaway detection
Short-circuit localization
Power dissipation analysis
Advantages:
Non-contact, real-time monitoring
Identifies hotspots before failure
Limitations:
Requires thermal calibration
Limited to powered boards
3. Best Practices for PCB Inspection
3.1 Combining Multiple Techniques
AOI + AXI for full defect coverage
ICT + FCT for electrical validation
3.2 Statistical Process Control (SPC)
Track defect rates using Six Sigma methodologies
Implement real-time feedback loops
3.3 AI-Powered Defect Detection
Machine learning algorithms improve defect recognition
Reduces false positives/negatives
4. Case Study: Reducing PCB Failures in Automotive Electronics
Problem: A Tier-1 automotive supplier faced 12% failure rates in ECU PCBs.
Solution:
Implemented AOI + AXI for solder joint inspection
Introduced thermal cycling tests
Results:
Defect rate dropped to 1.5%
-ROI achieved in 6 months
5. Future Trends in PCB Inspection
3D X-ray tomography for multilayer PCBs
AI-driven automated repair systems
In-line robotic inspection
References
1. IPC-A-610. (2020). Acceptability of Electronic Assemblies
2. Koh, S. (2021). Advanced PCB Inspection Techniques. IEEE Transactions on Electronics.
3. Siemens. (2023). Automated X-ray Inspection for High-Density PCBs.
4. Agilent Technologies. (2022). In-Circuit Testing Best Practices.
Industry Category