What Are the Key Principles of Choosing the Right PCB Contract Manufacturer?
By:PCBBUY 08/22/2024 16:54
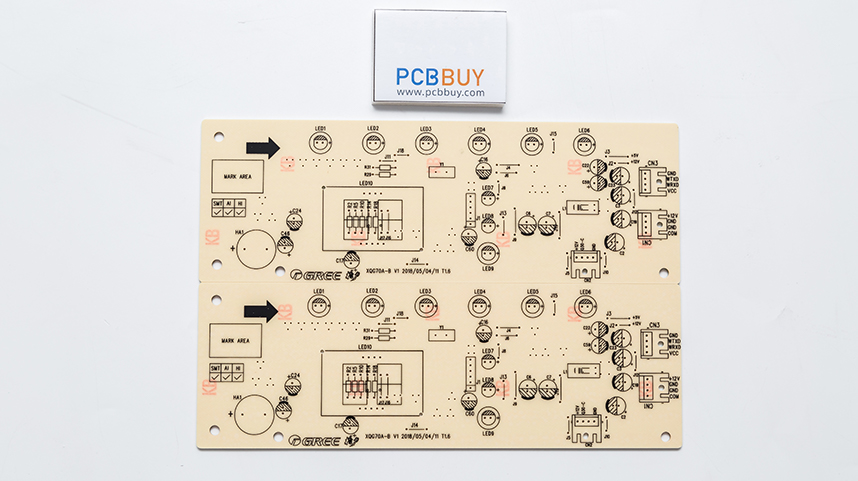
Printed Circuit Boards (PCBs) are fundamental to virtually all electronic devices, serving as the backbone that connects electronic components. As electronic devices become increasingly complex and miniaturized, the demand for high-quality, reliable PCBs has never been higher. Selecting the right Contract Manufacturer (CM) for PCB production is therefore critical. This decision can significantly impact the quality, cost, and delivery time of the final product. In this article, we will delve into the key principles that should guide the selection of a PCB Contract Manufacturer, considering technical capabilities, industry standards, cost factors, and more.
1. Understanding PCB Complexity and Requirements
Before diving into the selection of a PCB CM, it’s essential to understand the specific requirements of your PCB design. This includes factors like:
Number of Layers: Simple designs may require just one or two layers, while complex designs might require multi-layered PCBs, sometimes going up to 16 or more layers.
Material Requirements: The material of the PCB is critical. FR4 is standard, but high-frequency applications might require materials like Rogers or Teflon.
Trace Width and Spacing: These affect the electrical performance of the PCB.
Via Types: For complex designs, microvias, blind, and buried vias may be necessary.
Importance of Material Selection
Material selection directly impacts the electrical properties, mechanical strength, and thermal performance of the PCB. Table 1 summarizes the key materials used in PCB fabrication:
Material |
Dielectric Constant (εr) |
Loss Tangent (tan δ) |
Thermal Conductivity (W/mK) |
Applications |
FR4 |
4.5 |
0.02 |
0.29 |
General-purpose PCBs |
Rogers 4350B |
3.66 |
0.0037 |
0.69 |
High-frequency RF applications |
Polyimide |
3.4 |
0.004 |
0.12 |
Flexible PCBs, high-temp environments |
Understanding these parameters helps in selecting a CM that can work with the specific materials your design requires.
2. Assessing CM Capabilities
A PCB CM’s capabilities are the most critical factor in ensuring that your design is manufactured to specification. This includes technical capabilities, the equipment they use, and their ability to meet quality standards.
Technical Capabilities
When assessing a CM’s technical capabilities, consider:
Layer Count Capability: Can they fabricate PCBs with the number of layers your design requires?
Minimum Trace Width and Spacing: What are their limits on trace width and spacing, and does it align with your design needs?
Via Technology: Can they handle microvias, blind vias, and buried vias?
HDI and Flexible PCBs: Do they have experience in High-Density Interconnect (HDI) and flexible PCB technologies?
Equipment and Technology
The equipment used by the CM is indicative of the quality and precision of the final product. Here’s a list of critical equipment and technologies a modern PCB CM should have:
Laser Direct Imaging (LDI): For precise patterning and fine features.
Automatic Optical Inspection (AOI): For detecting defects in traces, pads, and solder joints.
X-Ray Inspection Systems: Essential for inspecting multilayer PCBs and BGA assemblies.
Advanced Plating Lines: For uniform copper deposition.
A CM with advanced technology ensures that your PCBs are manufactured to the highest standards, with tight tolerances and minimal defects.
3. Quality Assurance and Certifications
Quality assurance is crucial in PCB manufacturing. A reputable CM will have stringent quality control processes and industry-recognized certifications that guarantee the reliability and performance of their PCBs.
Quality Control Processes
Quality control should be integrated at every stage of the PCB manufacturing process. Key quality control processes include:
First Article Inspection (FAI): This involves producing a small batch of PCBs and inspecting them against all design specifications. FAI helps identify any issues early in the production process.
In-Process Inspection: Continuous monitoring during production to catch defects as they occur, minimizing waste and rework.
Final Inspection: Comprehensive testing of finished PCBs, including electrical testing, visual inspection, and functional testing.
Industry Certifications
Certifications are a hallmark of a CM’s commitment to quality. Essential certifications include:
ISO 9001: A standard for quality management systems.
IATF 16949: A quality management standard specifically for the automotive industry.
UL Certification: Ensures that the PCBs meet safety standards for electrical and fire hazards.
RoHS Compliance: Ensures that the PCBs are free of hazardous substances like lead, mercury, and cadmium.
These certifications not only ensure the quality of the PCBs but also demonstrate that the CM adheres to global standards.
4. Supply Chain Management
Efficient supply chain management is essential for ensuring timely delivery and controlling costs. A CM’s ability to manage its supply chain effectively can significantly impact the overall success of your project.
Material Sourcing
The CM should have established relationships with reliable suppliers for all the materials used in PCB fabrication. This ensures that the materials are of consistent quality and available when needed. Consider the following factors:
Supplier Reliability: Are the suppliers reliable in terms of delivery time and material quality?
Material Quality: Does the CM have a process for verifying the quality of incoming materials?
Inventory Management: How does the CM manage its inventory? Do they have a Just-In-Time (JIT) system to reduce costs and minimize waste?
Logistics and Delivery
The CM should have robust logistics and delivery systems to ensure that your PCBs are delivered on time and in perfect condition. This includes:
Lead Time Management: Can the CM deliver within the required timeframe?
Shipping and Handling: Are the PCBs properly packaged to prevent damage during transit?
Customs and Export Compliance: If dealing with an international CM, do they manage customs and export compliance efficiently?
5. Cost Considerations
Cost is a significant factor in the selection of a PCB CM, but it should not be the sole determinant. A focus on cost at the expense of quality or reliability can lead to greater expenses down the line.
Understanding Quotation Structures
When evaluating quotations from different CMs, it’s important to understand the structure of the costs. This includes:
Breakdown of Costs: Look for a detailed breakdown of material costs, labor, overhead, and margins.
Tooling and NRE Costs: Non-Recurring Engineering (NRE) costs are often a one-time expense for setting up the manufacturing process. These should be clearly identified.
Volume Discounts: Consider whether the CM offers discounts for higher volumes and how these affect the overall cost.
Total Cost of Ownership (TCO)
Total Cost of Ownership includes not just the initial cost of manufacturing but also the costs associated with quality control, potential defects, and supply chain management. A cheaper CM may have hidden costs, such as higher rates of defects, longer lead times, or less responsive customer service, which can increase the overall cost.
6. Lead Time and Flexibility
Lead time is a critical factor in PCB manufacturing, particularly in industries with fast-paced product development cycles. The CM’s ability to meet tight deadlines without compromising quality is crucial.
Production Lead Time
The production lead time is the time it takes from placing an order to receiving the finished PCBs. Factors that influence lead time include:
Complexity of the PCB: More complex PCBs take longer to produce.
Material Availability: Delays in sourcing materials can extend lead times.
Manufacturing Capacity: The CM’s ability to scale production to meet demand.
Flexibility and Responsiveness
A good CM should be flexible enough to handle changes in order quantities, design modifications, or urgent production needs. This flexibility can be critical in responding to market demands or addressing unexpected issues during the development process.
7. Communication and Support
Effective communication is key to a successful partnership with a PCB CM. The CM should offer clear, prompt, and open lines of communication, ensuring that you are kept informed at every stage of the manufacturing process.
Project Management
A dedicated project manager or point of contact can greatly enhance communication and ensure that your project receives the attention it needs. A good project manager will:
Provide Regular Updates: Keep you informed of the progress of your order.
Address Issues Promptly: Quickly address any issues that arise during production.
Coordinate Between Teams: Act as a liaison between your team and the various departments within the CM.
Technical Support
Access to knowledgeable technical support is essential, particularly during the design and prototyping phases. The CM should be able to provide:
DFM (Design for Manufacturability) Feedback: Guidance on optimizing your design for manufacturing, potentially reducing costs and lead times.
Material and Process Recommendations: Advice on material selection and manufacturing processes based on their experience with similar projects.
Rapid Prototyping Support: Assistance in quickly turning around prototypes for testing and validation.
8. Case Study: Selecting the Right CM for High-Volume Automotive PCBs
Illustrate the principles discussed, let’s consider a case study where a company needs to select a CM for the production of high-volume automotive PCBs.
Requirements
High Reliability: Automotive PCBs must meet stringent reliability standards due to the harsh operating environments.
Compliance with Automotive Standards: The PCBs must comply with standards such as IATF 16949 and AEC-Q100.
Cost Efficiency: The project requires cost-effective production due to the high volume.
CM Selection Criteria
Technical Capabilities: The selected CM should have experience in producing automotive-grade PCBs, with the ability to meet the required reliability and quality standards.
Certifications: The CM must be certified to IATF 16949 and have a proven track record in the automotive industry.
Supply Chain Management: The CM should have strong relationships with suppliers of automotive-grade materials and a robust logistics system to ensure timely delivery.
Cost Considerations: The CM should offer competitive pricing, with clear cost structures and the potential for volume discounts.
Outcome
By selecting a CM with the right technical expertise, certifications, and supply chain capabilities, the company successfully launched its automotive product, meeting all quality and reliability requirements while staying within budget.
9. Advanced Testing and Validation
For applications requiring high reliability, such as aerospace or medical devices, advanced testing and validation of the PCB are essential. The CM should offer a range of testing options to ensure the performance and durability of the PCBs.
Thermal Cycling and Environmental Testing
Thermal cycling tests involve subjecting the PCB to repeated cycles of high and low temperatures to simulate the stresses it will experience in the field. Environmental testing might also include humidity, vibration, and shock tests.
Testing for thermal expansion is critical in ensuring that the PCB materials will not delaminate or crack under extreme temperature variations.
Signal Integrity and Impedance Testing
For high-speed or RF PCBs, maintaining signal integrity is paramount. Impedance control is critical in these designs, and the CM should be equipped to test and validate the impedance of traces and vias.
Ensuring that the CM can accurately control and test impedance is crucial for applications where signal integrity is a priority.
10. Future Trends in PCB Manufacturing
As technology advances, PCB manufacturing is evolving rapidly. When selecting a CM, it’s important to consider whether they are keeping pace with industry trends and emerging technologies.
Adoption of Advanced Materials
Materials such as ceramics, flexible substrates, and organic laminates are becoming more common in PCB manufacturing. A forward-thinking CM should be exploring and adopting these materials to offer more options for advanced designs.
Integration of IoT and Smart Manufacturing
The Internet of Things (IoT) and smart manufacturing technologies are revolutionizing PCB production. CMs that integrate these technologies can offer better traceability, quality control, and efficiency.
Example: A CM using IoT-enabled machines can provide real-time data on production status, allowing for quicker identification and resolution of issues.
Environmental and Sustainability Considerations
Sustainability is becoming increasingly important in PCB manufacturing. CMs that focus on reducing waste, recycling materials, and using environmentally friendly processes are more likely to meet future regulatory requirements and customer preferences.
Conclusion
Selecting the right PCB Contract Manufacturer is a complex but critical decision that can have a significant impact on the success of your product. By considering factors such as technical capabilities, quality assurance, cost, lead time, communication, and future trends, you can make an informed choice that aligns with your project’s needs. As the PCB industry continues to evolve, staying abreast of new technologies and practices will be essential in maintaining a competitive edge.
References
1. IPC-2221: Generic Standard on Printed Board Design.
2. ISO 9001: Quality Management Systems – Requirements.
3. IATF 16949: Automotive Quality Management System Standard.
4. "High-Frequency PCB Design Guidelines," by John Doe, IEEE Transactions on Advanced Packaging, 2022.
5. "Material Selection for RF PCBs," by Jane Smith, Journal of Electronics Manufacturing, 2023.
6. "Trends in Advanced PCB Materials," by Robert Green, Electronics Weekly, 2024.
Industry Category