What Are the Main PCB Thermal Management Techniques?
By:PCBBUY 04/19/2022 09:52
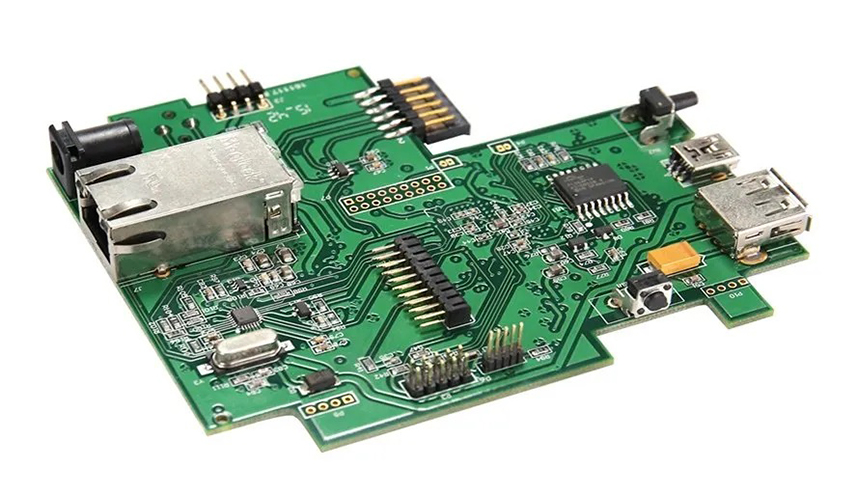
Choosing a substrate with an appropriate thermal conductivity is one of many important aspects of PCB design. Thermal management in PCBs becomes particularly important in smaller boards with active components that switch at high speed. It is also important in boards that will carry high current as resistive losses in a trace will generate heat, which then transfers into the substrate.
If you are looking for the information of PCB thermal management, please check and read the passage for more professional knowledge. Come and check the content below.
Why PCB thermal paste is important for manufacturing?
It is well-known that the removal of excess heat from components or parts that tend to generate high temperatures is critical during electronics operation. Heat sinks that can have thermal conductivities greater than 200W/(m·K), are common for these components, which include CPUs, GPUs, power transistors and other high-performance semiconductor-based devices
During operation, the greatest source of heat on circuits boards is generation by components. And the heat removal techniques implemented are done so during PCB assembly. However, the assembly process itself introduces heat to the board, which also should be a design consideration. There are two heat transfer issues, dissipation and distribution.
To be most effective, thermal paste should fill in all of the gaps between the two surfaces at which it is applied. Additionally, it is desirable that the paste not conduct electricity away from the component. Another important consideration is operational lifetime. For thermal pastes, typical ranges are 3-5 years, which means that for many components it may need to be replaced. All of these factors must be considered if it is determined that thermal paste should be utilized for your design.
What are the guidelines of thermal relief PCB?
Are you going to deal with thermal relief PCB? Then, you must know some relevant guidelines to avoid mistakes.
· You have to use thermal pads while connecting your thru-hole pin to the power place, metal fill, and other bigger metals.
· You must know how much power the pin can conduct. Based on this factor, you can identify the width and number of spokes. You can achieve 40 mils of spokes with 4 spokes. Each of these spokes must have a width of 10 mils.
· SMT components directly soldered to the big metals must have some thermal relief between the metal and solder pad.
· In a few cases, you may not be able to connect all spokes to the thermal relief pad. The congestion of thermal reliefs can result in this problem. Moreover, when the metal has very limited space, and you use thermal reliefs in the split plane, you will encounter this problem. You have to ensure that the chosen software has its own rules to detect minimum connections of thermal reliefs.
· It is essential to know about the terminologies related to components and pads.
· Termination and termination width– Termination refers to a metallization band present at the chip component’s end. The termination’s width is about the dimension across the chosen component.
· Tolerance– It is about how much pad is used under your component.
· Overlap– The component termination covers a pad surface known as overlap. The overlap has a length that includes tolerance.
Why thermal relief PCB is important?
Thermal relief plays a vital role while creating your circuit design. You can use the thermal relief pad anytime when you connect the negative plane to the thru-hole part. You know that the thermal relief pad has a varying number of spokes with different width based on how much power requirements are needed for a pin. A power pin, requiring a 40 mil trace and connecting a plane, must have the pad with four 10 mil spokes.
However, the question is- Do your PCB vias need these thermal relief pads. The major reason for using this pad is to maintain a balance of the heat-sinking activities of pins soldered into planes. As the vias do not get the component pin, it does not need any relief pad with thermal properties. It will establish a link to the plane.
Why to pay attention to thermal relief for a PCB?
Thermal reliefs are the spooked connections from a thru-hole or surface mount pad to an area fill or plane. Their purpose is to provide a robust electrical connection from the pad to the plane while preventing the heat needed for soldering from dissipating into the metal plane. The green color represents a solid plane of copper on a circuit board in the picture below, and you can see four thermal relief connections for each outer pin. In the case of a surface-mount pin that connects to a large metal area, multiple traces may be used from the pad to the copper to accomplish the same results.
The purpose of the thermal relief is to aid in the manufacturability of the circuit board. While a direct flooded connection gives the best electrical performance, it also serves as a heat sink for pins connected to the plane. This sink could effectively pull the heat away from the pin during automated soldering operations and produce poor solder joints in the connection. Simultaneously, the heat sinking attributes of a direct connection would make manual soldering operations difficult for technicians during rework. Additionally, too much metal on one pad versus the other on small two-pin discrete parts can cause a thermal imbalance in the component. This imbalance can result in a manufacturing phenomenon known as “tombstoning.”
Industry Category