What Are the Main working logistics of HASL in PCB Industry?
By:PCBBUY 09/20/2023 09:23
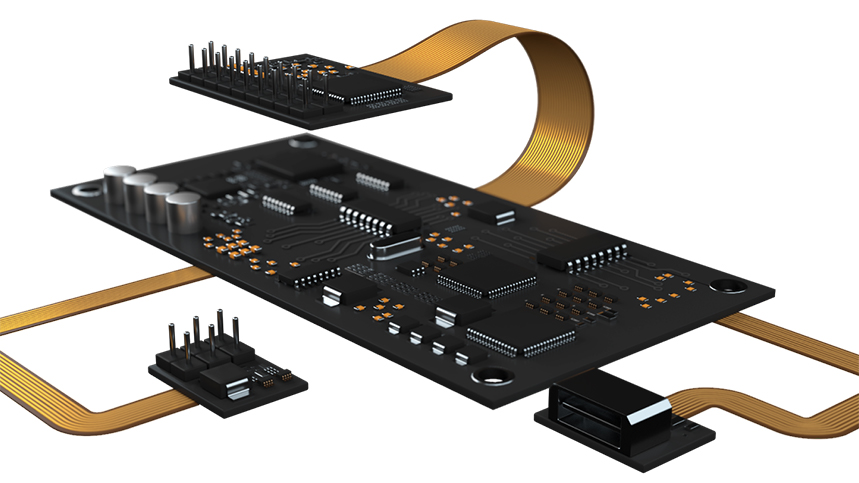
PCB manufacturing is divisible into two primary stages: fabrication and assembly. The surface finish process inextricably links them together, ensuring sufficient bonding between the bare board and the components for continuous performance and extended reliability. PCB surface finishes come in many flavors, but HASL is the most prominent for non-consumer devices: as an extension of the solder material (and thus, the solder processes), it is readily integrable for all board materials that are already using the same solder material to bond components to the bare board. This advantage holds for both leaded and non-leaded solders making HASL a highly applicable solder finish that is indispensable for PCB production.
The Logistics of HASL in Manufacturing
The HASL process is relatively straightforward: after the necessary contact time with the molten solder, the panel passes through planar-aligned air knives, which blow away excess solder with air jets at temperatures above the solder’s melting point. After solidification, the panel undergoes a wash to remove leftover flux, followed by a bake to dry. The HASL process is performable with a vertical or horizontal system, depending on the method of solder deposition: a molten solder bath for the vertical alignment or a nozzle/roller configuration that dispenses solder to the top and bottom of the board simultaneously. The horizontal process has a few advantages:
· As an in-line process, it can easily integrate with existing equipment like pre-etch, washing, and drying. Integrating multiple processes within a single in-line system allows for simultaneous pre-heating of the solder, which reduces processing time and provides a corresponding increase in production throughput.
· There is greater uniformity in the solder finish, as the effects of gravity are constant for each side of the board.
· In general, an in-line system reduces the amount of human contact with panels, reducing defects related to mishandling while increasing throughput.
Inspection and Troubleshooting of Common HASL Errors
The foremost advantage of HASL to manufacturers is that solder processes are already so well-characterized and integrated into PCB production that there is little difficulty translating this to a surface finish. There is no need for X-ray fluorescence or destructive cross-section analysis, as a simple visual inspection will suffice. A HASL finish should appear silver and lustrous – just like a solder joint – with no visible evidence of partial or incomplete solder wetting. The presence of an uneven HASL finish typically indicates a few potential process faults:
· Thinned coating – During application, there was insufficient solder to provide complete coverage of the pad surface.
· Incorrect process parameters – Some combination of the solder flux, the solder temperature, or the time the panel underwent the HASL process resulted in a poor finish outcome.
· Excessive solder removal – After the air knives remove the bulk of solder, the residual solder remaining cannot provide complete coverage of the pads after accounting for surface tension.
Process Control for HASL Surface Finishes
A deficient HASL finish exposes the intermetallic to the atmosphere when it usually sits between the solder and copper pad layers. Although the presence of the intermetallic indicates the wettability of the process, atmospheric exposure gravely impacts the solderability of the finish and should be considered grounds for rework. For this reason, HASL process control must ensure both an even coating and a minimum growth of the intermetallic layer to maximize the distance between the surface solder layer. Since there is a tendency for the exposed copper to dissolve into the molten solder, process engineers and technicians will want to monitor the bath for the intermetallic that precipitates out of the solution and falls to the bottom of the pot due to its density. It’s possible to alleviate this condition by dredging the precipitate or slightly increasing the temperature and copper content of the solder bath to prevent panel copper dissolution and intermetallic precipitation, according to Le Chatelier’s principle.
Industry Category