What Is BOM Stand for in the PCB Manufacturing Industry?
By:PCBBUY 04/13/2022 10:09
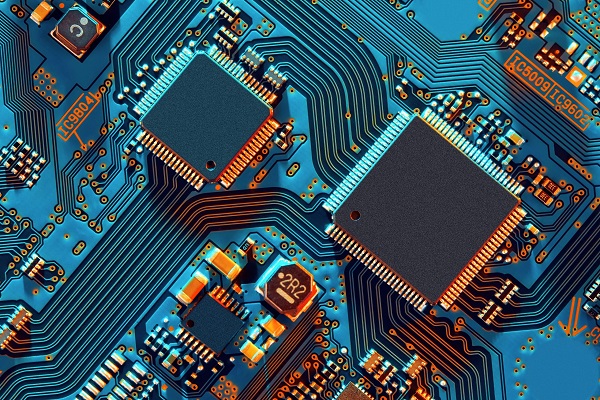
The Bill of Materials (BOM) could be considered the "shopping list" of any given electronic product manufacturer in a complete layperson's terms. It should contain everything necessary to make sure that you get the parts you need for your product. There can be many types of information in a PCB BOM, but the parts must have a core set of elements to start with.
If you are going to learn more about BOM list in the PCB, please check and read the content below in this passage for professional knowledge.
What are the 3 main types of BOM?
It also contains individual information on each of the parts that require complex assembly and, if there is any relation to another component from the list. The MBOM is then shared and applied in the manufacturing approach, where sometimes Enterprise Resource Planning (ERP) is required, or in some cases even a Manufacturing Execution System (MES).
The Engineering Bill of Materials (EBOM) is defining the parts included in the assembly that are designed by the engineering departments. It is showing the perspective of the structure, and often, EBOM is visualized as a technical or mechanical drawing of the end design.
Sales Bill of Materials (SBOM) is where the sales stage takes place. Here the finished product assembly process is defined through the sales lense managed as a sales item instead of an inventory item. The SBOM is structuring the sales stage by listing products by their market order document. It is important to understand that each different bill of materials contains different levels of detail called structure.
For instance, an EBOM lists parts for the assembly of a Rigid circuit board related to a specific end design.
This way, engineers will be able to use the BOM as a guide to manufacturing it without any misconceptions. For instance, a PCB assembly BOM can be generated with specific software instead of editing by hand, which is complicated.
What is a BOM used for?
In SMT manufacturer, the bill of materials is the link for contact and communication with different people and departments. It is used in various departments and systems, and specific data is obtained from BOM. For example:
Design department – The designer of the BOM and is also the user of the BOM. It needs to obtain the information of all parts and the structure information from the BOM.
Process technology department – Generates each component’s manufacturing process and the assembly process according to the BOM. They also process and manufacture tools, jigs, and molds used in the PCB assembly.
SMT department – Mounts the components on PCB according to the BOM. The warehouse distributes the components according to the BOM.
Financial and purchasing department – Determinesthe cost of the final product according to the cost of each self-made or purchased part in the BOM.
The QC department – Ensuresthe correct products are produced based on BOM.
What are the best practices of PCB BOM Inventory management?
The first step in establishing good practices for BOM inventory management in PCB CAD libraries is to develop a well-defined library process:
· Part requests: To build a new CAD part for PCB design should require a formalized request process. This request should be routed through component engineering to verify the application and availability of the requested part and confirm that the part conforms to company standards and policies.
· Manufacturing specifications: The parts’ datasheets should be kept on file within the design department and preferably within a product data management (PDM) system for access throughout design and manufacturing. This data will be used for the construction and the validation of the completed CAD models.
· Verification: The new part needs to be verified that it has been built correctly and satisfies the needs of all the key stakeholders (design, manufacturing, etc.). The verification sign-off should also be kept on file with the part request.
· Database updates: Once completed, the part needs to be installed in the library, and new part notifications published to the design team.
The next step of inventory management for PCB design teams is to establish the processes and procedures mentioned above for part updates and verifications in new designs. CAD library parts need to be confirmed in new designs as being the latest versions and available from the company’s supply chain. There also needs to be procedures in place to run the automated part checks through the CAD system on completed designs before they are sent out for manufacturing.
How to create a BOM?
There are three questions you need to be asking yourself when creating a BOM for your next project: The "when," the "what," and the "how." After discussing these topics with your selected staff and the client who has assigned the project to your organization, you can then proceed with your project.
It would help if you thought of an electrical product project like the head chef of a restaurant feels when preparing their restaurant. There are more similarities between the two than you think.
Most restaurants need to answer these three questions quickly, accurately, and in the right order. If they do not (and most do not), they usually face dire consequences down the road.
It is what happens with smaller-scale restaurants. They approach these questions in an air of panic, not knowing what question to answer first and getting less than complete information on answering these questions. The larger chain restaurants have an established system of answering these questions.
Industry Category