What Is Component Alignment in PCB Assembly?
By:PCBBUY 04/18/2022 10:11
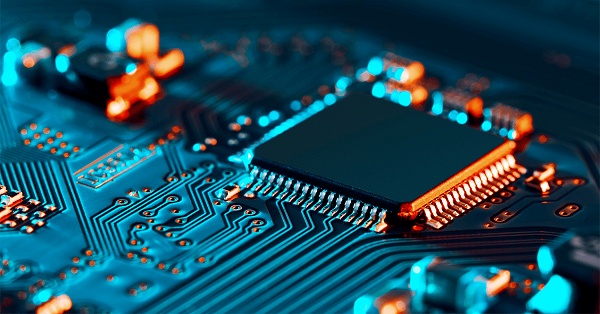
Precision holes in the bare board will be used to align the layers during the initial lamination and any subsequent lamination cycles. After the press, the board will be placed in another jig for application of soldermask and silkscreen. Yet another fixture will use them for electrical probing to find opens and shorts. Good panels will then be put on a robotic assembly line and then on to a soldering machine using the same holes.
Do you know the methods to choose proper alignment in PCB assembly process? In this passage, we are going to tell you all the details and information about alignment in PCB assembly, if you are curious about it please check and read the content below.
Why alignments affect PCB design?
The entire EAGLE community has been shouting from the rooftops to give you alignment tools, and we’ve been listening. After all, there’s nothing enjoyable about squinting to count grid points while you line up that row of SMD resistors or vias. The new alignment tools in Autodesk EAGLE includes everything you might expect:
· Align a set of objects by their top, bottom, left, right, or center origins.
· Evenly space grouped objects based on horizontal or vertical distributions.
· Align new design blocks or library parts to your grid settings with grid alignment.
Now, while all of these alignment tools will surely make your life easier at design time, they even have an impact down the road during manufacturing. It’s more than just making your board beautiful; alignment tools can help with。
How to determine the right alignment for PCB?
Technology marches on and the end result is a decreased margin for error. Even the language has to adapt as mils give way to microns because one thousandth of an inch is too coarse of a measure for modern PCB geometry. As the traces and spaces shrink to accommodate the latest chips, the onus is on the fabricators and assemblers to achieve greater precision in all aspects of manufacturing.
Where does it end? Could Intel's new two-nanometer fab be the last stop? It seems so but I would not bet on it. Somewhere, somebody is working on Angstrom class devices. Why not? Well, a single atom of copper comes in around 0.23 nano-meters so Intel is depositing about eight or nine atoms of copper across the width of a connection. To quote Carl Sagan, “Billions and billions…” but we’re scaling down rather than up.
Back in the good old days, there was one size for tooling holes, 125 mils with a plus/minus tolerance of one mil. Now, there is an 89 mil hole too because everything in this game shrinks over time. Unilateral tolerances are often applied where the pin will be the nominal value with a plus tolerance but no negative tolerance. The hole then gets zero oversize and a small negative tolerance. The actual numbers come down to what the fab shop can do on a best-effort basis. It’s almost an interference fit but not quite.
The smaller boards that you’d find in a smartwatch or similar device do not have room for tooling holes on the board so the holes become a standard part of the assembly sub-panel. The sub-panel is maintained through fab, assembly and test and only broken down once the boards are known to be working up to the standard requirements.
Ok, we’re set up for component placement on the assembly line. But we aren’t. The pick and place machine has a camera that can find a specific set of features on the board. These features are called fiducial marks and they help the robotic arm calibrate on the exact location of the components.
A typical board-level fiducial mark, or fid, will consist of a one millimeter dot of exposed copper surrounded by a three millimeter clearance in the soldermask and other circuit patterns. It is important to have a solid plane on the layer below the fid so that the camera can recognize and register on the dot without the distraction of a circuit pattern underneath. There is no drilling involved though it may look like a hole location for the uninitiated.
What are the challenges of alignment and components for PCB?
Increased density, shrinking footprints, higher data rates, and thermal management are but a few of the challenges affecting the design and fabrication of printed circuit boards (PCBs) in today’s electronic systems. And did I mention cost?
An important, although sometimes overlooked consideration, is these increasingly sophisticated PCBs often require more complex connector systems. Most of the aforementioned design factors also affect connector design and performance, including smaller footprints, diminishing profiles, and the need for increased reliability. And did I mention cost? These strict connector design parameters can create conflicting goals for connector manufacturers, namely balancing the need for increased performance and density while managing costs.
One of the most common connector-related challenges – one that is often not considered until it raises its potentially ugly head – is aligning multiple connector sets between two mated PCBs.
This is a common point of discussion for Samtec Product Engineering and the Interconnect Processing Group (IPG)(1). They have worked with countless Design and Process Engineers on this issue. I spoke with Kevin Meredith, Product Engineer at Samtec, about the challenges of aligning multiple connector sets between two PCBs
What’s So Important about Component Placement?
There’s a common saying that goes something like this – PCB design is 90% placement and 10% routing. This is entirely accurate. Taking the time to precisely place your components will make your life a whole lot easier when it comes time to route everything, while also giving your board its best electrical performance. But what happen if you just slap your components down without care?
· Hours Wasted. You’ll likely create a nightmare for yourself when you find out that some of your parts don’t even have enough space to be routed because you packed them too close together. The worst component placement jobs can lead to an entire board that needs to be started again from scratch.
· Busted Boards. Let’s say you do manage to place down some components and traces and ship your files off to your manufacturer. Next thing you know you might get a board back, that doesn’t work because your parts weren’t soldered correctly (more on this later).
· Ugly Aesthetics. Let’s face it, as engineers we love symmetry and precision, and there’s nothing more unsettling than seeing a board that wasn’t given some proper love and care during its component placement. It’s just plain lazy.
Make sense? Here’s the real kicker – there’s no universally “right” way to do it. Give a schematic to 100 different engineers, and you’ll likely get 100 different layouts back. This is why the PCB layout process is viewed as an artistic process.
Industry Category