What Is PCB Recycling Technology?
By:PCBBUY 12/21/2024 15:49
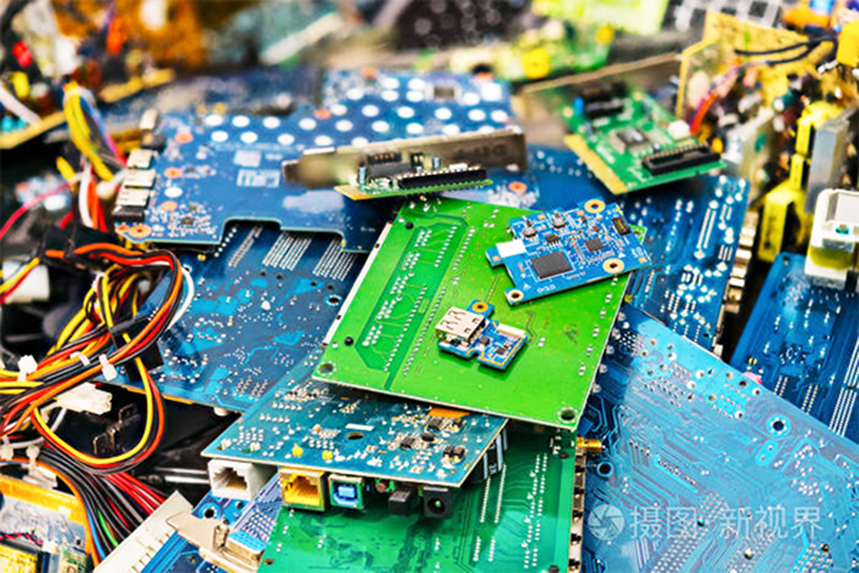
Printed Circuit Boards (PCBs) are integral components in a vast array of electronic devices, from smartphones and computers to medical equipment and industrial machinery. As technology advances and the production of electronic devices increases, so does the amount of PCB waste. This waste poses significant environmental challenges, necessitating effective recycling and reclamation technologies. This article delves into the various methods and technologies involved in the recycling and reclamation of PCBs, focusing on both liquid and solid waste recovery as well as the treatment of obsolete PCBs.
PCB Composition and Environmental Impact
PCBs are composed of various materials, including fiberglass, epoxy resin, and a mix of metals like copper, gold, silver, and palladium. The presence of hazardous substances such as lead and brominated flame retardants further complicates their disposal. Improper handling and disposal of PCB waste can lead to soil and water contamination, posing risks to human health and the environment. Therefore, efficient recycling methods are essential to mitigate these risks and recover valuable materials.
Recycling Processes for Liquid Waste
During the PCB manufacturing process, several liquid wastes are generated, including etching solutions, plating baths, and cleaning solvents. These liquids often contain metals, acids, and other chemicals that can be hazardous if not properly treated. The primary methods for recycling and reclaiming liquid waste from PCB manufacturing are:
Chemical Precipitation: This process involves adding chemicals to the liquid waste to convert dissolved metals into insoluble particles. These particles can then be filtered out, allowing for the recovery of metals such as copper and gold. The remaining liquid can be treated further to neutralize any remaining hazardous substances before discharge.
Electrochemical Recovery: Electrochemical techniques, such as electroplating and electrowinning, are used to recover metals from liquid waste. In electroplating, a direct current is passed through the solution, causing metal ions to deposit onto a cathode. Electrowinning, on the other hand, uses an electric current to reduce metal ions to their solid form, which can then be collected and refined.
Membrane Filtration:
This method employs membranes to separate contaminants from liquid waste. Techniques such as reverse osmosis, ultrafiltration, and nanofiltration are effective in removing metal ions, organic compounds, and other impurities. The concentrated waste can be further processed to recover valuable materials, while the purified water can be reused in the manufacturing process.
Ion Exchange:
Ion exchange resins are used to remove metal ions from liquid waste by exchanging them with non-hazardous ions. This method is particularly effective for recovering precious metals and other high-value materials. The spent resin can be regenerated and reused, making this a cost-effective and sustainable solution.
Recycling Processes for Solid Waste
Solid waste generated during PCB manufacturing includes offcuts, defective boards, and spent materials. The recycling of solid PCB waste involves several steps to separate and recover valuable materials while ensuring the safe disposal of hazardous substances.
Mechanical Processing:
Mechanical methods such as shredding, grinding, and milling are used to reduce the size of PCB waste. This facilitates the separation of different materials based on their physical properties. For instance, metallic particles can be separated from non-metallic components using techniques like magnetic separation and eddy current separation.
Thermal Processing:
Thermal methods involve heating PCB waste to high temperatures to decompose organic materials and recover metals. Pyrolysis, incineration, and gasification are common thermal techniques. Pyrolysis heats the waste in the absence of oxygen, producing char, oil, and gas. Metals remain in the char, which can be processed further to extract valuable metals. Incineration and gasification, on the other hand, involve burning the waste with controlled amounts of oxygen, generating energy and reducing the volume of waste.
Chemical Processing:
Chemical methods use solvents, acids, and other chemicals to dissolve and recover metals from PCB waste. Hydrometallurgical processes involve leaching metals with acids or other solvents, followed by precipitation or electrochemical recovery. This method is particularly effective for recovering precious metals such as gold and palladium. However, it requires careful handling of chemicals and the treatment of waste liquids to prevent environmental contamination.
Biological Processing:
Emerging technologies such as bioleaching use microorganisms to extract metals from PCB waste. Certain bacteria and fungi can oxidize metals, converting them into soluble forms that can be recovered from the solution. Bioleaching is a low-energy, environmentally friendly alternative to traditional chemical methods, though it is currently less common and still under development for large-scale applications.
Treatment of Obsolete PCBs
Obsolete PCBs from discarded electronic devices represent a significant portion of electronic waste (e-waste). Effective treatment and recycling of these PCBs are crucial to recover valuable materials and reduce environmental impact.
Dismantling and Sorting:
The first step in treating obsolete PCBs is dismantling the electronic devices to separate the PCBs from other components. Manual dismantling ensures the recovery of intact PCBs, which can then be sorted based on their material composition and potential value. Automated systems using robotic arms and artificial intelligence are increasingly being used to improve efficiency and reduce labor costs.
Mechanical Recycling:
Once sorted, PCBs undergo mechanical processing to separate different materials. Techniques such as shredding, milling, and screening help to liberate metal particles from the non-metallic matrix. Magnetic and eddy current separators further separate ferrous and non-ferrous metals, while density separation techniques such as froth flotation and air classification can isolate different types of plastics and fiberglass.
Thermal and Chemical Recycling:
To recover metals from obsolete PCBs, thermal and chemical methods are employed. Pyrolysis and incineration can be used to decompose organic materials, leaving behind metal-rich ash. Hydrometallurgical processes, such as acid leaching and solvent extraction, dissolve metals for recovery through precipitation or electrochemical methods. These processes are effective for extracting precious metals and other high-value materials, though they require careful management of waste streams to minimize environmental impact.
Refinement and Purification:
The final step in PCB product recycling involves refining and purifying recovered metals to produce high-purity products. This may involve additional chemical treatments, electrorefining, and smelting. The purified metals can then be sold and reused in the production of new electronic devices, closing the loop in the recycling process.
Regeneration and Recycling of Acidic Etching Solution in PCB Manufacturing
Printed Circuit Boards (PCBs) are essential components in virtually all electronic devices. The manufacturing process of PCBs involves several steps, including the etching of copper layers to form circuit patterns. Acidic etching solutions, typically composed of hydrochloric acid (HCl) and cupric chloride (CuCl₂), are commonly used for this purpose. Over time, these etching solutions become saturated with dissolved copper and other impurities, necessitating their regeneration and recycling to maintain efficiency and reduce environmental impact. This article delves into the processes involved in the regeneration and recycling of acidic etching solutions used in PCB manufacturing, with a focus on the underlying chemical reactions and corresponding equations.
Chemical Composition and Function of Acidic Etching Solutions
The primary components of acidic etching solutions in PCB manufacturing are hydrochloric acid and cupric chloride. The solution operates on the principle of oxidation and reduction reactions, where the copper layer on the PCB is oxidized and dissolved into the solution. The overall reaction can be represented as follows:
Cu (solid) + 2HCl (aq) + CuCl2 (aq)→ 2 CuCl (aq) + 2H+ (aq)
In this process, the copper (Cu) from the PCB reacts with hydrochloric acid (HCl) and cupric chloride (CuCl₂) to form cuprous chloride (CuCl) and hydrogen ions (H⁺).
Saturation and Depletion of Etching Solutions
As the etching process continues, the solution becomes saturated with cuprous chloride, leading to a decrease in etching efficiency. Additionally, the concentration of hydrochloric acid diminishes over time. To maintain the effectiveness of the etching process, the spent etching solution must be regenerated or replaced. Regeneration is preferred as it reduces waste and lowers operational costs.
Regeneration of Acidic Etching Solutions
Regeneration of acidic etching solutions involves oxidizing the dissolved cuprous chloride back to cupric chloride and replenishing the hydrochloric acid. The typical regeneration process can be divided into two main steps: oxidation and acid replenishment.
1. Oxidation of Cuprous Chloride
Cuprous chloride (CuCl) in the spent etching solution is oxidized to cupric chloride (CuCl₂). This can be achieved using various oxidizing agents, such as chlorine gas (Cl₂), hydrogen peroxide (H₂O₂), or oxygen (O₂). The chemical reactions for these oxidizing agents are as follows:
Using chlorine gas:
2CuCl (aq) + Cl2 (g) \rightarrow→ 2CuCl2 (aq)
Using hydrogen peroxide:
2CuCl({aq) + H2O2(aq) + 2HCl(aq) → 2 CuCl2 (aq) + 2H2 O (l)
Using oxygen:
4CuCl(aq) + O2(g) + 4HCl(aq) → 4CuCl2 (aq) + 2H2 O (l)
Each of these reactions effectively regenerates the cupric chloride necessary for continued etching, restoring the oxidizing power of the solution.
2. Acid Replenishment
Hydrochloric acid is consumed during the etching process, leading to a decrease in its concentration. To restore the solution's acidity, additional hydrochloric acid is added. The amount required is determined by the concentration of the spent solution and the desired concentration for optimal etching performance.
Recycling of Acidic Etching Solutions
Recycling involves not only regenerating the spent solution but also recovering and purifying the dissolved copper. This process ensures the continuous use of the etching solution and minimizes environmental impact. The recycling process can be broken down into several steps:
1. Precipitation of Copper
One common method for recovering copper from the spent etching solution is through precipitation. Copper can be precipitated as copper(I) oxide (Cu₂O) or copper(II) hydroxide (Cu(OH)₂) by adjusting the pH of the solution using alkali substances such as sodium hydroxide (NaOH) or calcium hydroxide (Ca(OH)₂). The reactions are as follows:
Precipitation of copper(I) oxide:
2CuCl(aq) + 2NaOH(aq} → Cu2O (s) + 2NaCl (aq) +H2 O (l)
Precipitation of copper(II) hydroxide:
CuCl2(aq) + 2NaOH (aq)→ Cu(OH) 2 (s) + 2NaCl (aq)
The precipitated copper compounds are then filtered out from the solution.
2. Conversion to Metallic Copper
The precipitated copper compounds can be further processed to recover metallic copper. This is typically done through reduction reactions using agents such as hydrogen gas (H₂) or carbon monoxide (CO). The reduction reactions are as follows:
Reduction of copper(I) oxide:
Cu2O (s) +H2 (g) → 2 Cu(s) +H2O (g)
Reduction of copper(II) hydroxide:
Cu(OH)2 (s) +H2 (g) →Cu (s) + 2 H2O (l)
The metallic copper obtained can be reused in various industrial applications, thus closing the loop in the recycling process.
Environmental and Economic Benefits
Regenerating and recycling acidic etching solutions offer significant environmental and economic benefits:
1. Reduction of Hazardous Waste: Proper regeneration and recycling reduce the amount of hazardous waste generated, minimizing the environmental impact and associated disposal costs.
2. Resource Conservation: Recovering and reusing copper and other materials from spent etching solutions conserve valuable natural resources and reduce the demand for raw materials.
3. Cost Savings: Recycling processes can significantly lower the operational costs of PCB manufacturing by reducing the need for fresh etching solutions and raw materials.
4. Regulatory Compliance: Adhering to environmental regulations and implementing sustainable practices help companies avoid penalties and enhance their corporate image.
The regeneration and recycling of acidic etching solutions in PCB manufacturing are essential for maintaining the efficiency of the etching process and minimizing environmental impact. By employing chemical processes to regenerate etching solutions and recover valuable materials, manufacturers can achieve sustainable and cost-effective production. Understanding the underlying chemical reactions and implementing advanced recycling techniques are crucial steps towards a more environmentally friendly and economically viable PCB manufacturing industry.
Challenges and Future Directions
While current recycling technologies offer effective solutions for PCB waste management, several challenges remain. The complexity of PCB material composition, the presence of hazardous substances, and the economic viability of recycling processes are significant hurdles. To address these challenges, ongoing research and development are focused on improving the efficiency and sustainability of recycling methods.
Enhanced Material Recovery: Innovations in mechanical, thermal, and chemical processing aim to increase the recovery rates of valuable materials from PCB waste. Advanced sorting technologies, such as sensor-based sorting and artificial intelligence, can improve the accuracy and efficiency of material separation.
Green Technologies:
The development of environmentally friendly recycling methods, such as bioleaching and solvent-free chemical processes, is crucial to reducing the environmental impact of PCB recycling. These technologies offer potential benefits in terms of lower energy consumption and reduced chemical use, though further research is needed to scale them up for industrial applications.
Economic Viability:
To make PCB recycling economically viable, it is essential to optimize processes and reduce costs. This can be achieved through automation, improved resource efficiency, and the development of new markets for recovered materials. Government incentives and regulatory frameworks can also play a crucial role in supporting the growth of the recycling industry.
Circular Economy:
Moving towards a circular economy model, where products are designed for recyclability and materials are continuously reused, can significantly reduce PCB waste. This involves designing electronic devices with modular components, using recyclable materials, and implementing take-back programs to facilitate the collection and recycling of obsolete products.
PCB recycling and reclamation technologies are vital for managing the growing volume of electronic waste and recovering valuable materials. By employing a combination of mechanical, thermal, chemical, and biological processes, it is possible to efficiently recycle both liquid and solid waste generated during PCB manufacturing and from obsolete electronic devices. Despite the challenges, advancements in technology and a shift towards a circular economy offer promising solutions for sustainable PCB waste management. Through continued innovation and collaboration, the environmental impact of PCB waste can be minimized, contributing to a more sustainable future.
Reference
He Wei, PCB Basic Electrical Information Science and Technology, China Machine Press,416-422
Industry Category