What Is Prepreg Used for PCB Manufacturing Process with 5 Tips?
By:PCBBUY 12/20/2021 09:46
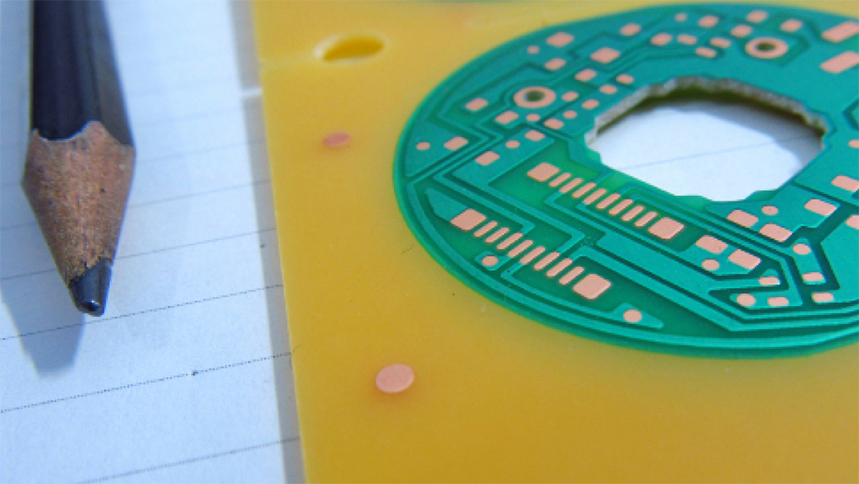
Prepreg, as the name suggests, is a glass fiber weave/cloth impregnated with a resin bonding agent. The glass fibers are interwoven to form a glass fabric. This glass fiber weave is partially dried to form a B-stage material. All prepregs are B-stage materials. During the manufacturing process of prepreg, it is important to follow the grain direction of the material being used since it allows the material to be modified as per requirement. The number of warp and fill counts determines the amount of resin the glass fabric can retain.
During the manufacturing process of PCB, what is the function of Prepreg? Are you going to know the working principles of Prepreg? If you are curious about Prepreg, please check and read the content below for more information in this passage.
1. Why is Prepreg so important?
Prepreg is an integral part of the PCB manufacturing process because:
These are easy to apply and to learn to work with. Getting accustomed to it does not require much technical expertise. With regular use, even a less tech-savvy person can become familiar with Prepreg. Thus, the cost of labor does not shoot up when the prepregs are used.
PCB Prepreg material is very less messy as compared to the wet style layups. Thus, these contribute to waste management during the manufacturing process better, followed in PCB making units.
These are available in various types, such as Kevlar, fiberglass, and hybrid as well. Thus, you name the purpose, and there is a suitable Prepreg available for it. To top it all, the possibility of reducing the weight of the device becomes higher, which is quite essential in some particular types of equipment required for working in unique conditions.
It is worth learning that the PCB Prepreg material displays a better shelf life when these are stored in colder temperatures. It is because its resin part remains deactivated, allowing it to remain intact and usable beyond a chosen timeframe.
2. What are the differences of Prepreg and core?
People often get confused between prepregs and cores due to their similarities. Allow me to clarify it for you. The core is a product of prepreg and lamination. It is more rigid compared to the prepreg. The core is made up of a fiberglass-epoxy laminate which meets the FR4 (Flame Retardant) grade with copper on either side. The core is usually manufactured by a core manufacturer and the company is liable for any faults in the material that might hinder the operation of a PCB. Whereas prepregs, as described earlier, are also made of the same material like the core but are partially dried without lamination and aren’t rigid like the core.
Another major difference between the prepreg and the core when used in stack up is the dielectric constant (Dk ). The Dk for the core does not vary, whereas the prepreg Dk before and after lamination will vary. This is why a few military applications of PCBs don’t use the foil method, instead go for the core method of lamination. I hope this disposes of the ambiguity.
3. What are the applications of Prepreg?
Multi-layered boards
What holds the layers together is the multi-layered board of Prepreg. The user will need to fuse them when they stack all the board’s layers by exposing it to high temperatures. They will then have the similarity between the overall board thicknesses with the Prepreg thickness. When the designers use the Prepreg on a multi-layered board, it must have specific characteristics. The new surface must not have excessive resin powder, cracks, foreign matter, defects, stains, or oil. It must have a smooth feel and look.
Complex PCBs
Engineers will probably have a more complex Prepreg if they have a complex PCB. As a result, they can only achieve the needed thickness for the board and Prepreg to use different types of Prepreg.
4. What is the manufacturing process of Prepreg?
Prepreg is a fiberglass fabric/towel coated with a resin preservative, as the name implies. The glass strands are knitted into a glass tissue. This glass fiber fabric is half-dried into material from the B-stage.
Most prepregs are substances of the B-stage. It is vital to track the volume fraction of the material used throughout the production process Prepreg, as it enables the material to be adjusted according to the demand. The number of repetitions of warp and fill affects the epoxy the glass weave can hold.
5. How to choose Prepreg for PCB?
Depending on the size and other needs, many kinds of prepregs are integrated into PCBs. According to its resin composition, Prepregs are compatible with standard resin (SR), mid resin (MR), or high resin (HR). The more and more resin it holds, the more costly it becomes.
With clear structural differences in the core prepreg materials, it is critical from a circuit design perspective to get an exact value for the electrical conductivity and the return loss. If your signals have minimal growth time, you can usually get away using a user information sheet value. Once your knee and analog signals have reached the GHz range, attention must be taken with the datasheet values, particularly when modeling interconnect behavior and employing resistance-controlled routing.
The difficulty with data source numbers is that the true electrical conductivity determined is based on the test technique, geometric routing, particular frequencies, convention on the law, and the thickness of the material. John Coonrod spoke extensively about this subject in a recent interview. The fabric pattern of PCB core/prepreg components renders them inhomogeneous and anisotropic, meaning that the main material qualities change in space and various directions. This is why we get fiber weaving phenomena such as excitation of the skew and fiber cavity.
Industry Category