What Is SMT Assembly in PCB Manufacturing and What Is Process?
By:PCBBUY 05/11/2022 10:27
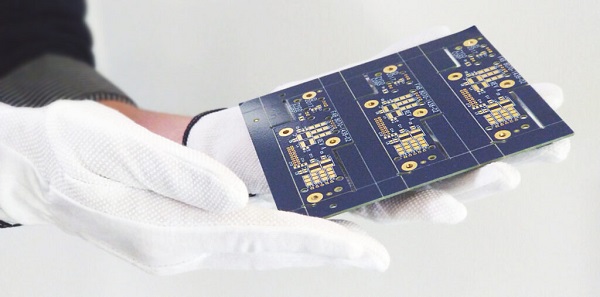
Surface mount technology became known in the 1960s, and the applicability slowly rose in the 1980s. This technology was known as planar mounting in the beginning. The technique of surface mounting involved SMDs or surface mound packages. Components in this board have lead surrounding or underneath.
In this passage, we are providing you all the information of SMT process of PCB. If you are looking for the professional knowledge of SMT process of PCB, please check and read the content below in this article.
What is the definition of SMT of PCB?
What separates surface mount from through-hole technology is that there is no need to drill holes in the circuit board to connect the tracks and the components. Establishing relationships through leads. The ingredients are in direct touch with the PADs of the circuit board And add solder paste to PAD with the help of stencil solder. There is also a pick and place machine responsible for placing the components on the solder paste set initially above the PAD. After setting these components, they have to be placed in a reflow oven or introduced in a vapor phase to be soldered permanently in the surface mount PCB assembly.
What is SMT and its advantages?
Surface Mount Technology is a newer way of arranging components on printed circuit boards. For many years prior, electricians and engineers would use leads to fit circuit board components through holes. Careful preparation was necessary to ensure that all leads were formed in the right way to fit on various types of boards.
SMT assembly is a more efficient process where components are soldered directly onto the board. By eliminating the need for passing leads through PCBs, the process has become faster, more efficient, and cost-effective. SMT assembly also saves space, allowing more components to be housed on a smaller board. This is why many modern devices are smaller but pack lots of features.
SMT is a highly intricate process where each component is strategically positioned and mounted onto electrical boards for optimal functionality. This is one of the reasons why SMT and SMD overlap. Having an effective electrical device requires a combination of proper component selection and mounting strategies. During SMT, calculated amounts of solder paste are applied onto the board before a machine carefully mounts each component.
How does SMT electronics assembly work?
Electronics manufacturing using surface-mount technology (SMT) simply means that electronic components are assembled with automated machines that place components on the surface of a board (printed circuit board, PCB). In contrast to conventional through-hole technology (THT) processes, SMT components are placed directly on the surface of a PCB instead of being soldered to a wire lead. When it comes to electronic assembly, SMT is the most frequently used process in the industry.
Electronic assembly encompasses not only placing and soldering components to the PCB, but also the following production steps:
· Applying soldering paste, which is made of tin particles and flux, to the PCB
· Placing SMT components to the soldering paste on the PCB
· Soldering the boards with a reflow process.
What are measures of process control in solder paste printing?
PCB Quality Control
Sampling inspection should be carried out on all batches of PCBs prior to solder paste printing. Inspection items include:
· Whether deformation occurs on PCB;
· Whether oxidation takes place on PCB pad;
· Whether scratches, shorts and copper exposure takes place on PCB surface;
· Whether printing is evenly smooth or not.
In the process of process control on PCB performance, sufficient attention should be paid from the beginning to the end. Firstly, gloves have to be worn when picking up PCB boards. Secondly, when visual inspection is applied, the distance between naked eyes and inspected boards should be in the range from 30cm to 45cm with the angle about 30° to 45°. PCB boards should be gently dealt with during inspection to avoid collision or falling and they mustn’t be stacked up or kept upright to stop circuits from being cut. Meanwhile, location holes on boards should be inspected to ensure that stencil openings are compatible with pads on PCB.
Application and Storage of Solder Paste
In the process of SMT assembly, validity of solder paste has to be rigorously monitored to maintain its high reliability. Overdue solder paste mustn’t be applied and purchased solder paste should be kept in cold closet of refrigerator. Uncovered solder paste has to be used within one week. In the process of solder paste application, the workshop temperature should be controlled at approximately 25℃ and RH (Relative Humidity) should be controlled within 35% to 75%. Temporarily-not-used solder paste should be placed away from workshop to stop it from being mixed up with in-use solder paste. When “new” solder paste has to be mixed up with “old” solder paste, the mixing ratio should be 3:1.
Some Control Measures in Solder Paste Printing
Successful solder paste printing should be compatible with the following requirement:
· Printing should be complete;
· No bridging takes place;
· Printing thickness should be evenly smooth;
· No turn-down edge occurs on pad;
· No deviation occurs in printing.
Industry Category